Maintenance, Operating procedures (cont'd) – DeVilbiss MG5-OLSTAT-3A User Manual
Page 10
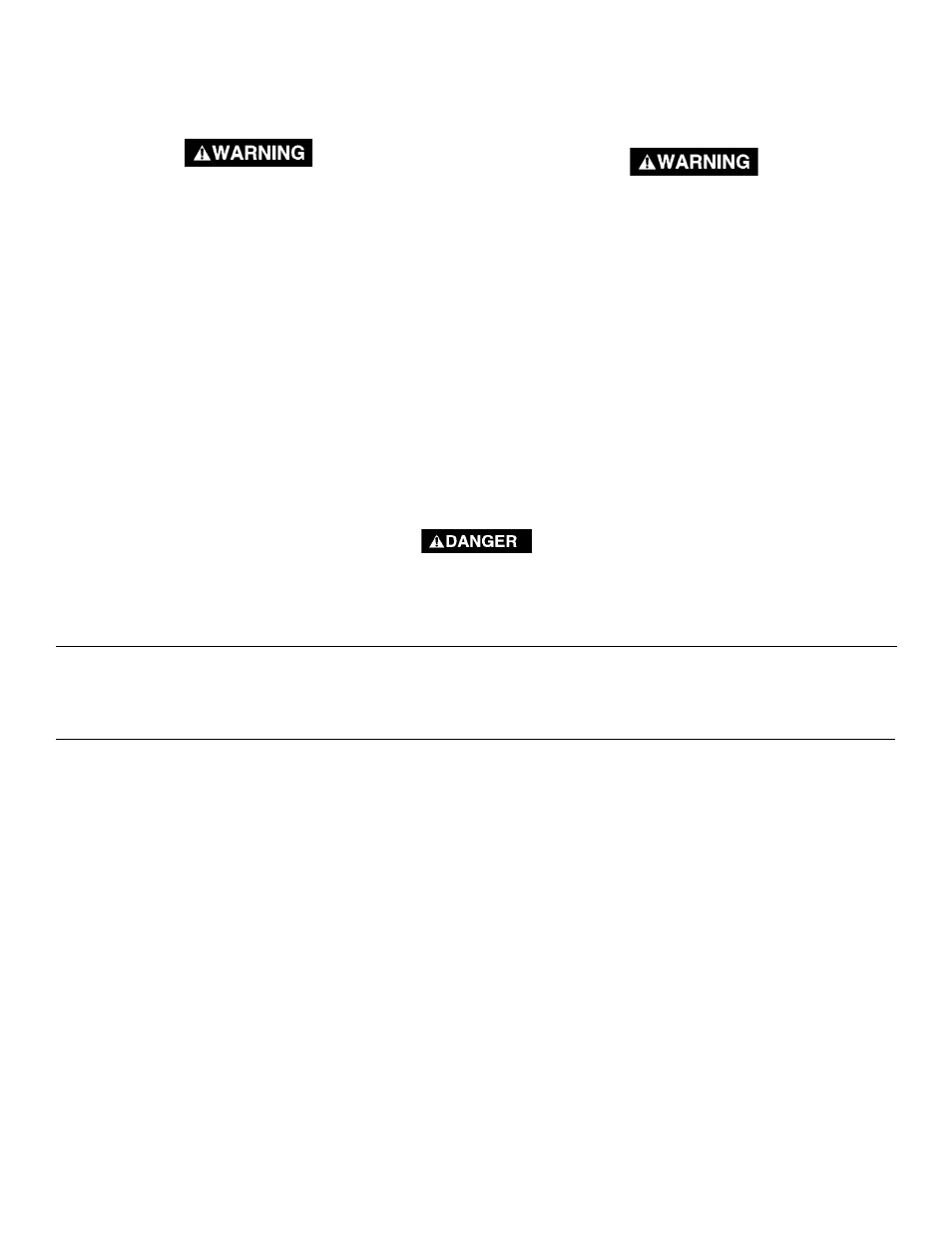
10
UNIT CYCLES AUTOMATICALLY WHEN POWER IS ON. DURING MAINTENANCE, YOU COULD BE EXPOSED TO VOLTAGE
SOURCES, COMPRESSED AIR OR MOVING PARTS. PERSONAL INJURIES CAN OCCUR. UNPLUG THE UNIT AND BLEED OFF ALL
AIR TANK PRESSURE BEFORE DOING ANY MAINTENANCE OR REPAIR. NEVER OPERATE THE UNIT WITH THE BELT GUARD
REMOVED.
2. Increase frequency of oil changes if humidity or operating
conditions are extreme.
Every 160 Hours of Operation:
1. Check drive belt tension; adjust if necessary. (Refer to SER-
VICE INSTRUCTIONS in this manual.)
2. Inspect air lines and fittings for leaks; correct as necessary.
3. Check the alignment of the motor pulley to the flywheel. If
necessary, align to within 1/32 inch on center line.
Each Year of Operation or if a Problem
is Suspected:
Check condition of air compressor pump intake and exhaust
valves. Replace if damaged or worn out.
MAINTENANCE
Normal Operation (cont'd)
TOO MUCH AIR PRESSURE CAUSES A HAZ-
ARDOUS RISK OF BURSTING. CHECK THE
MANUFACTURER'S MAXIMUM PRESSURE
RATING FOR AIR TOOLS AND ACCESSORIES.
THE REGULATOR OUTLET PRESSURE MUST
NEVER EXCEED THE MAXIMUM PRESSURE
RATING. ON MODELS HAVING ONLY A SHUT-
OFF VALVE, YOU MUST INSTALL A REGULA-
TOR BEFORE USING ACCESSORIES RATED AT
LESS THAN 125 PSIG.
3. Turn the pressure switch lever to the "ON-AUTO" position and
allow tank pressure to build. The motor will stop when tank
pressure reaches cut-out pressure. Slowly release air pres-
sure from globe valve.
4. The compressor is now ready for use.
6. After the water has been drained, close the drain cock. The air
compressor can now be stored
.
NOTE
If the drain cock valve is plugged, release all
air pressure. The valve can then be removed,
cleaned and reinstalled.
DRAIN TANK DAILY. WATER WILL CONDENSE
IN THE AIR TANK. IF NOT DRAINED, WATER
WILL CORRODE AND WEAKEN AIR TANK,
CAUSING A RISK OF AIR TANK RUPTURE.
OPERATING PROCEDURES (cont'd)
5. When You Are Finished: drain tank pressure at approxi-
mately 20 PSI, open the drain valve and allow moisture to drain.
Routine Maintenance Schedule
Daily:
1. Check oil level. Add if necessary.
2. Drain water from the air tank, any moisture separators or
transformers.
3. Check for any unusual noise and/or vibration.
4. Manually check all safety valves to make sure they are
operating properly.
5. Inspect for oil leaks and repair any leaks found.
6. Inspect air filter, replace if necessary.
Every 40 Hours of Operation:
1. Inspect condition of drive belt; replace if necessary
Every 100 Hours of Operation:
1. Drain and refill compressor crankcase with 16 fluid ounces
(473.2 ml) of clean compressor oil such as Castrol Heavy Duty
30 weight.
To ensure efficient operation and longer life of the air compressor outfit, a routine maintenance schedule should be prepared and followed.
The following routine maintenance schedule is geared to an outfit in a normal working environment operating on a daily basis. If necessary,
the schedule should be modified to suit the conditions under which your compressor is used. The modifications will depend upon the hours
of operation and the working environment. Compressor outfits in an extremely dirty and/or hostile environment will require a greater
frequency of all maintenance checks.