Technical data – Crown Equipment Cushion Tire Lift Trucks MAX50 User Manual
Page 5
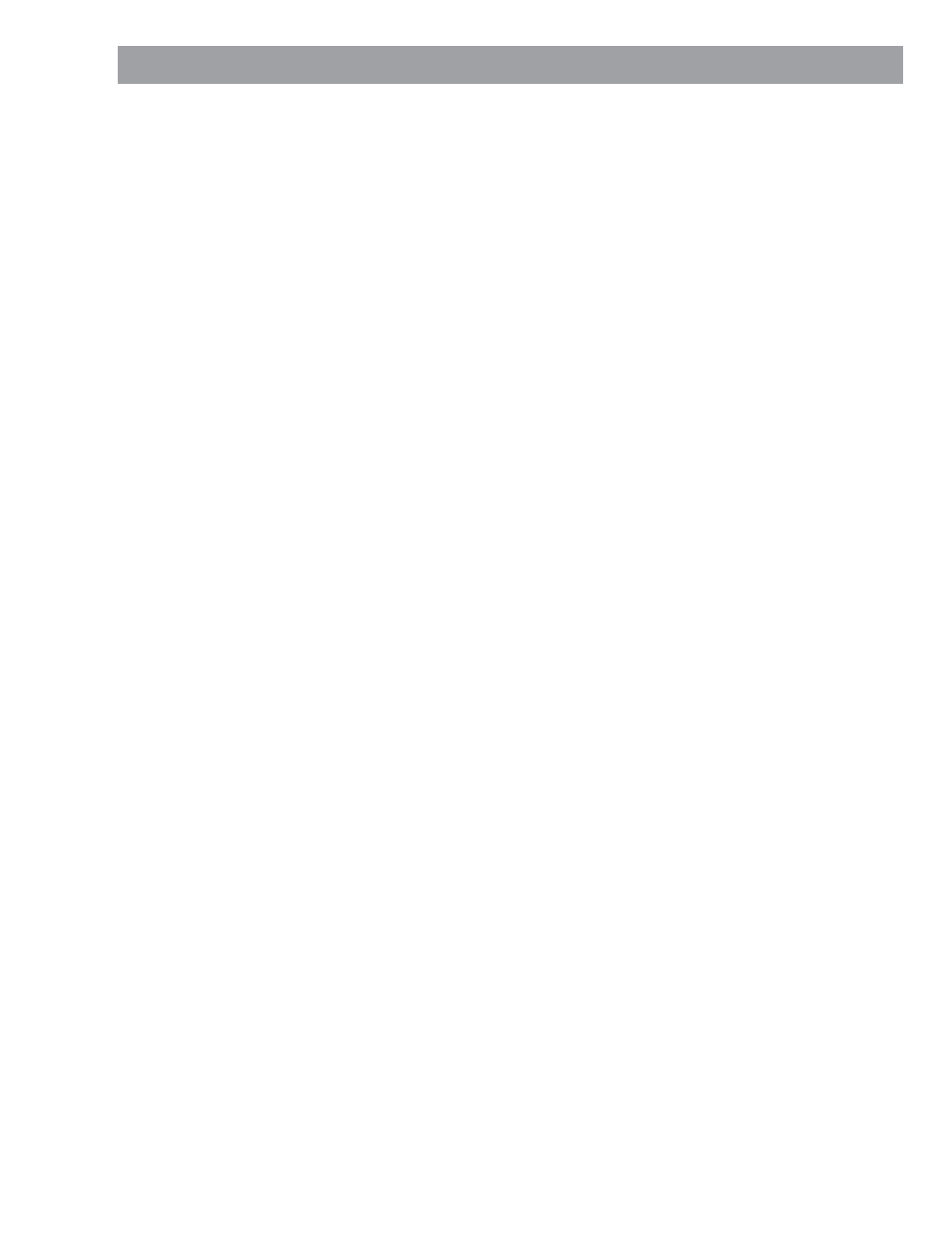
FUEL SYSTEM
Gasoline, LPG, or Dual-Fuel systems are
available. The gasoline fuel tank is integral to
the truck frame.
• In-tank mounted gasoline fuel delivery
pump, fuel-level sensing unit, pressure
regulator and fi lter are standard.
• LPG fuel system uses single-point, throttle
body fuel injection. A removable 33 lb.
fuel tank is available with a fold back tank-
mounting bracket.
COOLING SYSTEM
The high-capacity aluminum radiator is
designed with an effi cient thermal transfer
fi n and integral oil cooler for the transmis-
sion torque converter.
• High-volume cooling fan uses fl exible plastic
blades and shroud for maximum air volume
and noise abatement.
ELECTRICAL SYSTEM
Standard instrument package and operator
conveniences:
• 12-volt electrical system
• 50A alternator with built-in IC regulator
• Key-lock, anti-restart ignition switch
• High-torque, low-amp starter motor with
planetary gear reduction
• Waterproof electrical connectors
• Electric fuel gauge, water temperature
gauge, LCD hour meter
• Indicator lights for Neutral/Return to
Neutral, Low Oil Pressure, Low Battery/
Alternator Output, Check Engine Warning,
Hydraulic Lock (Operator Presence), and
ECCS Status Code
• ECCS Service Support Tool connector for
rapid system diagnostics
HYDRAULIC SYSTEM
The Hydraulic System features an integral
reservoir, direct drive gear pump and fully
fi ltered system.
• Large hydraulic fl uid reservoir integral to
the truck frame reduces heat buildup in
the system.
• Load sensing valve in the hydraulic circuit
reduces the fl ow of oil to the power steer-
ing system when steering wheel is idle.
FRAME
An all-welded assembly with heavy-gauge
steel and integral hydraulic and fuel tanks
provide exceptional durability.
• Welded front cross-member and bolted
drive axle increase frame rigidity.
• Loads are transferred directly from the mast
to the drive axle and onto the fl oor without
being transmitted through the frame,
reducing frame stress.
• Wide, open step is designed into the
frame assembly without compromising the
structure.
DRIVE AXLE
A heavy-duty, cast steel drive axle housing
supports the load and chassis without placing
a load on the free-fl oating axle shafts.
A fl ange is mounted to the truck frame to
improve load distribution and reduce
frame fl exing.
TRANSMISSION
Hamech single-speed, powershift transmis-
sion is specifi cally designed for industrial
applications.
• Column-mounted electrical shift lever gives
the operator easy directional control without
removing a hand from the steering wheel.
• Optimized stall ratio for torque converter
provides high torque without sacrifi cing
travel speed.
• A modulating control valve absorbs initial
pressure spikes during initial engagement
and directional change. This improves shift-
ing capabilities and prolongs the life of the
entire drive train.
• Transmission oil is double-fi ltered by a 125-
micron mesh on pickup, and a 35-micron
cartridge on the return line.
• Transmission oil cooler is integral with
the radiator.
• Inching control and auxiliary brake pedal
combination allows the operator precise
truck positioning with positive control.
BRAKES
Hydraulic brakes are self-energizing and
self-adjusting.
• Brake fl uid reservoir is located under the
console cover for fast, easy inspection and
maintenance.
• Heavy-duty brake backing plate and thick
brake drum provide reliable braking action
and reduced heat.
• Mechanical parking brake has two-stage
latching mechanism for positive engagement.
STEER AXLE
Fully Hydrostatic Power Steering is standard.
• Heavy-duty fabricated steer axle has dou-
ble-acting, double-ended power steering
cylinder and no drag links or tie rods.
• Steering stops are machined into the
steering cylinder to reduce stress impact
on steering linkages.
• Grease fi ttings on all linkages are acces-
sible without lifting the truck.
MAST, CARRIAGE, LBR AND FORKS
High-visibility mast assembly has a 4-roller
carriage that is available in two-, three-, and
four-stage Free Lift, Free View designs.
• Sealed bearings require no maintenance.
• Angle-mounted bearings and a shaped rail
fl ange prevent excessive wear and friction,
while maintaining correct side thrust
clearance.
• ITA Class II carriages accept a variety of fork
sizes and common load-handling attachments.
• 48-inch-high load backrest is standard for in-
creased load control and operator protection.
• Single or double auxiliary hydraulic-function
internal hose routing is available.
OPERATOR COMPARTMENT
A unique suspension compartment isolates
the operator from the fl oor surface and from
engine vibration, for greater operator
comfort and productivity.
• Comfort seat has built-in lumbar support,
retractable seat belt, lateral restraint sys-
tem, and fore and aft adjustment.
• Hydraulic control levers are positioned for
optimum access and ease of use. Inter-
national symbols on the contoured grips
indicate the function.
• Tilting steering console has small-diameter
steering wheel and electronic instrumen-
tation. Tilt is infi nitely adjustable, with
extended room between the engine cover
and console.
• Wide-open fl oorboard has suspended
brake and inching pedals with ribbed rub-
ber pads for comfort and safety. Integral
accelerator mechanism has a transfer roller
for smooth operation.
• Full-width rubber fl oor mat provides a
large, non-slip surface and reduces noise,
vibration and heat.
• Open step in the frame with a traction
surface and a large handgrip provide easy
entry and exit for the operator.
• Standard headlight/turn indicator control
lever is mounted on the steering column
for easy use.
• Full-width overhead guard provides excel-
lent visibility for high stacking and meets or
exceeds ITSDF requirements.
SERVICEABILITY
The engine and transmission can be easily
accessed for daily inspection without the use
of any tools.
• Single-piece, all-steel engine cover and
seat support is fully insulated to reduce
noise and heat transfer.
• Engine cover has gas-fi lled cylinder with
an automatic locking device to assist in
opening and to prevent the cover from
unexpectedly closing.
• Engine cover is shaped for easy access
into the engine area for maintenance
and service.
COMPLIANCE, APPROVALS AND
ENVIRONMENTAL CONCERNS
Designed for maximum recycling at end
of life, with special attention to materials
and construction. Counterweight designed
for breakup during recycling process.
Transmission case is recyclable aluminum.
Hamech lift trucks meet or exceed
American National Standard Institute,
ITSDF B56.1-Part III Safety Standards for
Powered Industrial Trucks.
Compliant with UL 558 for the appropriate
truck type. Contact your dealer for applica-
tion-specifi c requirements. Meets or exceeds
current EPA emissions standards.
TECHNICAL DATA