Digiflight 100 initial checkout, Initial checkout – TruTrak Digiflight Install Manual User Manual
Page 9
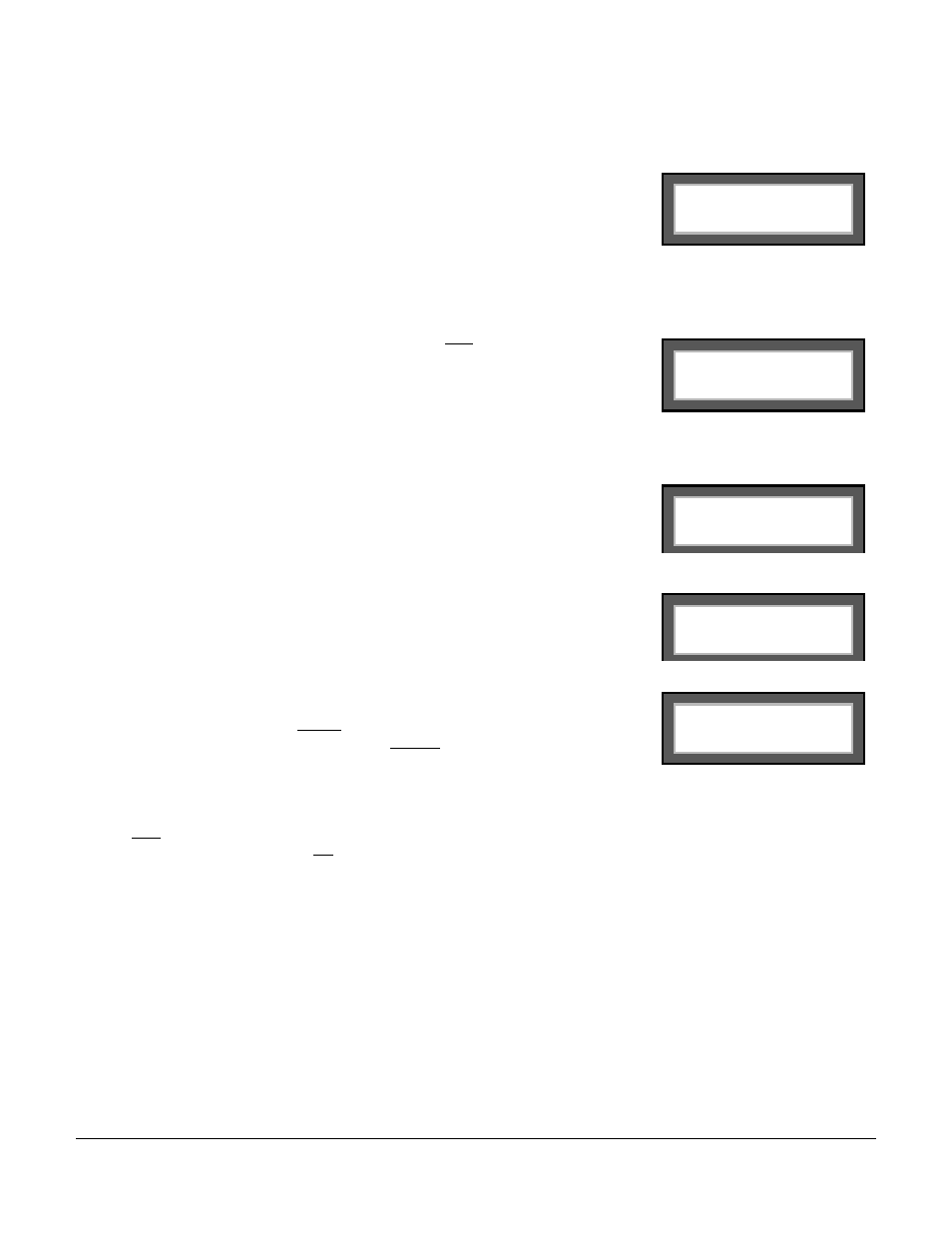
TruTrak Flight Systems
DigiFlight Autopilot Installation Manual
7
March 2002 Printing
DigiFlight 100 Initial Checkout
Once wiring is completed the autopilot should be tested in the aircraft while on the ground. The first step is to enter the setup
mode on the autopilot and set all parameters to their correct values. Apply power to the autopilot programmer.
The initial screen should be displayed, along with the words PWR UP in the lower-right of
the display. After approximately ten seconds, the autopilot is ready to be set up for
operation, indicating AP OFF on the display.
Many of the operations of the autopilot are initiated or confirmed by a press and release of
the knob (without rotating it). This is referred to as the ENTER operation. Special setup
operations and disengaging of the autopilot are done by holding the knob in for an
extended period of time. Any time there is an underlined field showing on the autopilot
screen, rotating the knob will cause the underlined active field to change.
Engage the autopilot by pressing ENTER. Then press and hold the knob in for about eight
seconds until the first setup screen, showing LAT ACTIVITY and LAT TORQUE is
displayed. (During this time the screen will change to indicate “AP OFF” but continue
holding in the knob.) Once the activity setup screen is on the display, rotate the knob as
necessary to set the lateral activity value to a value of 1 or 2. Press and release the knob to
enter that value and advance to the lateral torque field. Insure that the value displayed is
somewhere close to the maximum value of 250. Once that is done, press ENTER to enter
that value and advance to the next screen.
Rotating the knob, select a value for BAUD RATE which is compatible with the panel-
mount GPS receiver connected to pin 25. The value of 9600 is the most commonly used
rate. Once baud rate selection is done, press ENTER to enter that value and advance to
the next screen.
The next screen gives the option for calibrating the internal backup magnetometer. To the
MAG CALIBRATE? Question, answer N (no) at this time. This operation will be done at
a later time.
Press ENTER. The DigiFlight 100 display will now return to the main screen.
The next step in the check-out procedure is to verify that the servo runs, and in the correct
direction. The roll servo should be responding at this time, moving the controls in such a
way as to turn the aircraft from the current heading (shown as a 3-digit number after the
word MAG in the upper-left of the display) to the selected heading (shown as a 3-digit
number after the word SEL in the lower left of the display). The initial value of the
selected heading is the current heading of the aircraft at the moment of engagement, but
the knob can be used to modify the selected heading. When the heading shown as SEL agrees with the heading of the aircraft
shown in the top line as MAG, the roll servo should stop or run only very slowly. If the knob is rotated clockwise, to a selected
heading right of the current heading, the control yoke or stick should move in such a way as to roll the aircraft to the right.
Conversely, a selected heading to the left of the current heading will move the controls in the opposite direction to attempt a
roll towards the left. If servo direction is not correct, the wires going to pins 4 and 5 of the roll servo (pins 32 and 33 on the
main connector) must be reversed to achieve the correct response. If the servo does not move at all, double-check the LAT
TORQUE setting to make sure it is at least 240. If a servo jitters but does not actually rotate, check the wiring on the four servo
drive lines to that servo for continuity and correctness. If the servo does not seem to have any torque, check the roll torque
control line for continuity and correctness.
At this time, check that the servo arm or capstan is properly operating the controls. For servo installations using an arm, check
that as the controls go from limit to limit the arm of the servo remains in the operating range of the servo (a maximum of 100
degrees total rotation) and that when the controls are centered, the connecting pushrod is approximately perpendicular to the
arm of the servo. For capstan systems, insure that the cabling remains at proper tension and is properly secured as the servo
moves the controls from stop to stop. Insure that the servo remains secure in its mounting and does not flex its mounting
bracket as it drives the control to its stops. For installations using an arm, insure that as the servo moves the control towards
the end of control travel it does not cause the main control’s torque tube to flex in any way that could cause control system
lockup at the extremes of servo travel. Insure that any “lost motion” in the linkages is eliminated or minimized, in order to
maximize the performance of the autopilot. Lost motion (dead zone) will result in wandering or slow “hunting” behavior in
flight.
MAG 005
AP OFF
LAT ACTIVITY 2
LAT TORQUE 240
BAUD RATE 9600
MAG CALIBRATE? N
MAG 005
SEL 005 AP ON