Milwaukee Tool 2602-22DC User Manual
Page 3
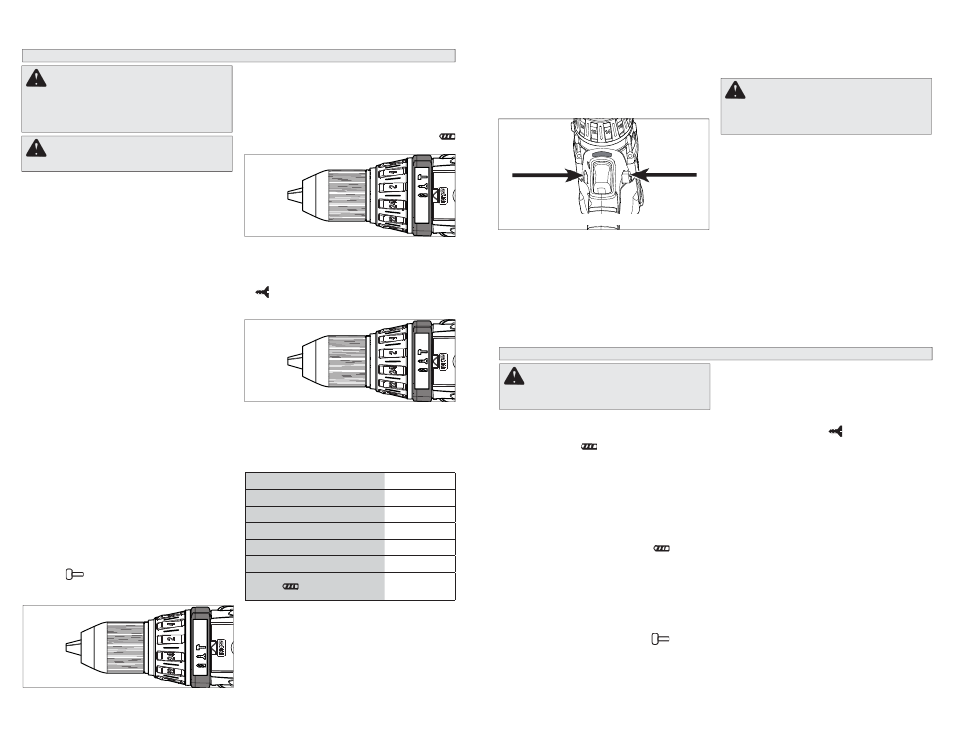
4
5
Using Keyless Chucks
This tool is equipped with a spindle lock. The chuck
can be tightened with one hand, creating higher grip
strengths on the bit.
Always remove the battery pack or lock the trigger
before inserting or removing bits.
1. To open the chuck jaws, turn the sleeve in the
counterclockwise direction.
When using drill bits, allow the bit to strike the
bottom of the chuck. Center the bit in the chuck
jaws and lift it about 1/16" off of the bottom.
When using screwdriver bits, insert the bit far
enough for the jaws to grip the hex of the bit.
2. To close the chuck jaws, turn the sleeve in the
clockwise direction. The bit is secure when the
chuck makes a ratcheting sound and the sleeve
can not be rotated any further.
3. To remove the bit, turn the sleeve in the coun-
terclockwise direction.
NOTE: A ratcheting sound may be heard when the
chuck is opened or closed. This noise is part of the
locking feature, and does not indicate a problem
with the chuck’s operation.
Selecting Speed
The speed selector is on top of the motor housing.
Allow the tool to come to a complete stop before
changing speeds. See “Applications” for recom-
mended speeds under various conditions.
1. For Low speed (up to 450 RPM), push the speed
selector to display “1”.
2. For High speed (up to 1700 RPM), push the
speed selector to display “2”.
Selecting Hammer, Drill or Drive Action
MILWAUKEE Hammer-Drills have three operating
modes: drilling with hammering action, drilling only,
and driving screws. To set the operating mode,
rotate the application selector collar and torque
selector collar to the desired symbols.
1. To use the hammer-drilling mode, rotate
the application selector collar until the hammer
symbol
appears in line with the arrow. Ap-
ply pressure to the bit to engage the hammering
mechanism.
Torque selector collar setting
Torque
1 - 5
0 - 16 in. lbs.
6 - 10
17 - 27 in. lbs.
11 - 15
28-37 in. lbs.
16 - 20
38-46 in. lbs.
21-24
47-60 in. lbs.
Drill
1 Low
2 High
550 in. lbs. *
150 in. lbs.
Fig. 1
To Hammer
Fig. 2
To Drill
Fig. 3
To Drive Screws
OPERATION
WARNING
Always remove battery
pack before changing or removing acces-
sories. Only use accessories specifically
recommended for this tool. Others may be
hazardous.
WARNING
To reduce the risk of injury,
wear safety goggles or glasses with side shields.
Using Control Switch
The control switch may be set to three positions:
forward, reverse and lock. Due to a lockout mecha-
nism, the control switch can only be adjusted when
the ON/OFF switch is not pressed. Always allow
the motor to come to a complete stop before using
the control switch.
Fig. 4
Push for
Forward
Push for
Reverse
PUSH TO CENTER TO LOCK
For forward (clockwise) rotation, push in the control
switch from the right side of the tool. Check the
direction of rotation before use.
For reverse (counterclockwise) rotation, push in the
control switch from the left side of the tool. Check
direction of rotation before use.
To lock the trigger, push the control switch to the
center position. The trigger will not work while
the control switch is in the center locked position.
Always lock the trigger or remove the battery
Starting, Stopping and Controlling Speed
1. To start the tool, grasp the handle fi rmly and pull
the trigger.
NOTE: An LED is turned on when the trigger is
pulled.
2. To vary the speed, increase or decrease the
pressure on the trigger. The further the trigger
is pulled, the greater the speed.
3. To stop the tool, release the trigger. Make sure
the bit comes to a complete stop before laying
the tool down.
Drilling
Place the bit on the work surface and apply fi rm
pressure before starting. Too much pressure will
slow the bit and reduce drilling effi ciency. Too little
pressure will cause the bit to slide over the work
area and dull the point of the bit.
If the tool begins to stall, reduce pressure slightly
to allow the bit to regain speed. If the bit binds,
reverse the motor to free the bit from the workpiece.
NOTE: The number selected on the torque collar
has no effect on operation of the drill in hammer
mode. NOTE: When using carbide bits, do not
use water to settle dust. Do not attempt to drill
through steel reinforcing rods. This will damage
the carbide bits.
2. To use the drilling only mode, rotate the ap-
plication selector collar until the drill symbol
appears in line with the arrow.
NOTE: The number selected on the torque collar
has no effect on operation of the drill in drilling
mode.
3. To use the driving screws mode rotate the
application selector collar until the drive symbol
appears in line with the arrow. Then rotate
the torque selector collar until the desired clutch
setting appears in line with the arrow.
The adjustable clutch, when properly adjusted, will
slip at a preset torque to prevent driving the screw
too deep into different materials and to prevent
damage to the screw or tool.
The torque specifi cations shown here are ap-
proximate values.
* Max developed torque when using Milwaukee XC
battery pack.
NOTE: Because the above settings are only a
guide, use a piece of scrap material to test the dif-
ferent clutch positions before driving screws into
the workpiece.
APPLICATIONS
WARNING
To reduce the risk of elec-
tric shock, check work area for hidden pipes
and wires before drilling or driving screws.
fl ow of dust indicates the proper drilling rate. Do not
let the bit spin in the hole without cutting. Do not
use water to settle dust or to cool bit. Both actions
will damage the carbide.
Driving Screws and Nut Running
Drill a pilot hole when driving screws into thick or
hard materials. Select the
driving screws mode.
Set the torque selector collar to the proper position
and set the speed to low. Use the proper style and
size screwdriver bit for the type of screw you are
using. With the screwdriver bit in the screw, place
the tip of the screw on the workpiece and apply fi rm
pressure before pulling the trigger. Screws can be
removed by reversing the motor.
Overloading
Continuous overloading may cause permanent
damage to tool or battery pack.
Bit Binding
A high rotational force occurs when a bit binds. If
the bit binds, the tool will be forced in the opposite
direction of the bit rotation. Bits may bind if they are
misaligned or when they are breaking through a
hole. Wood boring bits can also bind if they run into
nails or knots. Be prepared for bit binding situations.
To reduce the chance of bit binding:
• Use sharp bits. Sharp bits are less likely to bind
when drilling.
• Use the proper bit for the job. There are bits that
are designed for specifi c purposes.
• Use caution when drilling pitchy, knotty, wet or
warped material or when drilling in material that
may contain nails.
WARNING
To reduce the risk of injury,
always use a side handle when using this tool.
Always brace or hold securely. Ensure side
handle is tightened securely before each use.
pack before performing maintenance, changing
accessories, storing the tool and any time the tool
is not in use.
Drilling in Wood, Composition Materials and
Plastic
When drilling in wood, composition materials and
plastic, select the
drill-only operating mode.
Start the drill slowly, gradually increasing speed as
you drill. When drilling into wood, use wood augers
or twist drill bits. Always use sharp bits. When using
twist drill bits, pull the bit out of the hole frequently
to clear chips from the bit fl utes. To reduce the
chance of splintering, back work with a piece of
scrap wood. Select low speeds for plastics with a
low melting point.
Drilling in Metal
When drilling in metal, select the
drill-only
operating mode. Use high speed steel twist drills
or hole saws. Use a center punch to start the hole.
Lubricate drill bits with cutting oil when drilling in iron
or steel. Use a coolant when drilling in nonferrous
metals such as copper, brass or aluminum. Back
the material to prevent binding and distortion on
breakthrough.
Drilling in Masonry
When drilling in masonry, select the
hammer-
drill operating mode. Use high speed carbide-tipped
bits. Drilling soft masonry materials such as cinder
block requires little pressure. Hard materials like
concrete require more pressure. A smooth, even