4a.1 heating system piping: hot supply connections – LAARS SUMMIT SMW-250 - Install and Operating Manual User Manual
Page 8
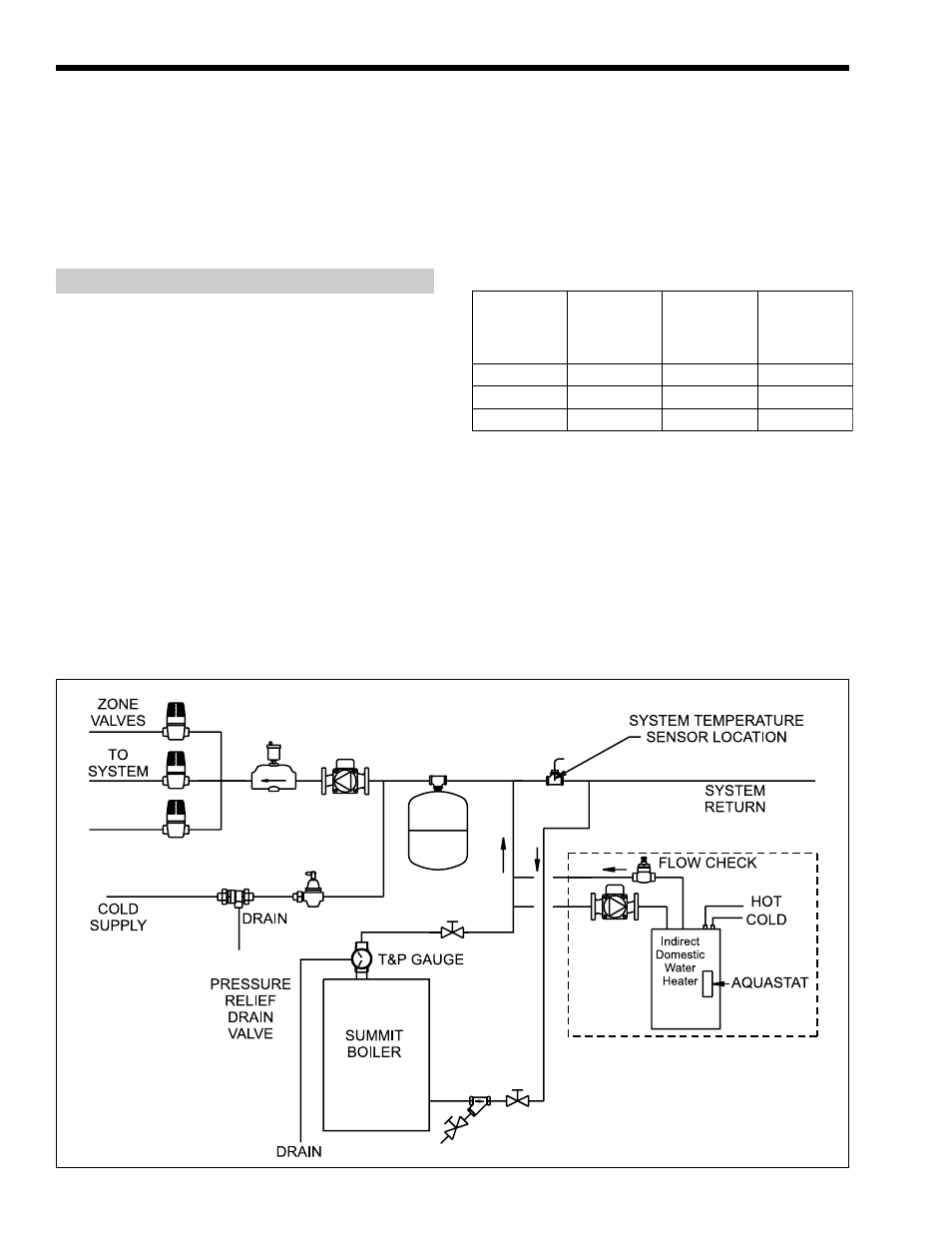
Page 8
LAARS Heating Systems
and Throttle Adjustment for the proper method
of verification.
11.
Before operating the appliance, the complete gas
supply system and all connections must be tested
for leaks using a soap solution.
SECTION 4A.
Water Connections
SMB-200/250 Boiler
4A.1 Heating System Piping:
Hot Supply Connections
NOTE: This appliance must be installed in a
closed pressure system with a minimum of 10 psi
static pressure.
Hot water piping should be supported by suitable
hangers or floor stands, NOT by the appliance. Due to
expansion and contraction of copper pipe,
consideration should be given to the type of hangers
used. Rigid hangers may transmit noise through the
system resulting from the piping sliding in the
hangers. It is recommended that padding be used
when rigid hangers are installed.
SUMMIT boilers must not be direct connected
to a heating system utilizing oxygen permeable tubing,
(see warranty). Provide a water to water heat
exchanger between systems to prevent corrosion of
internal pump, pump flanges, buffer tank (if installed)
or other components.
THE SUMMIT BOILER MUST BE
CONNECTED IN A PRIMARY/SECONDARY
TYPE SYSTEM OR WITH A FULL SIZED
BYPASS.
1.
Connect the 1¼" supply connection on the
appliance to the system bypass. Size the
combined length of supply and return to the loop
using Table 3.
Figure 7. Piping for Heating and Optional Domestic Hot Water.
Table 3. Water Pipe and Tube Sizing.
Copper tube or
pipe size
Maximum
allowable tubing
length
Amount
deducted for
each additional
90° elbow
Amount
deducted for
each additional
45° elbow
1¼"
40' (12m)
2' (0.6m)
1½' (0.5m)
1½"
120' (37m)
2' (0.6m)
1½' (0.5m)
2"
270' (82m)
2' (0.6m)
1½' (0.5m)
2.
Pipe the discharge of the relief valve, full size, to
a drain or in a manner to prevent injury in the
event of pressure relief.
3.
Install an air purger, an air vent, a diaphragm
type expansion tank, and a hydronic flow check
in the system supply loop. Minimum fill pressure
must be 12psig.
4.
Install shutoff valves where required.