Haltech HT051400 User Manual
Page 16
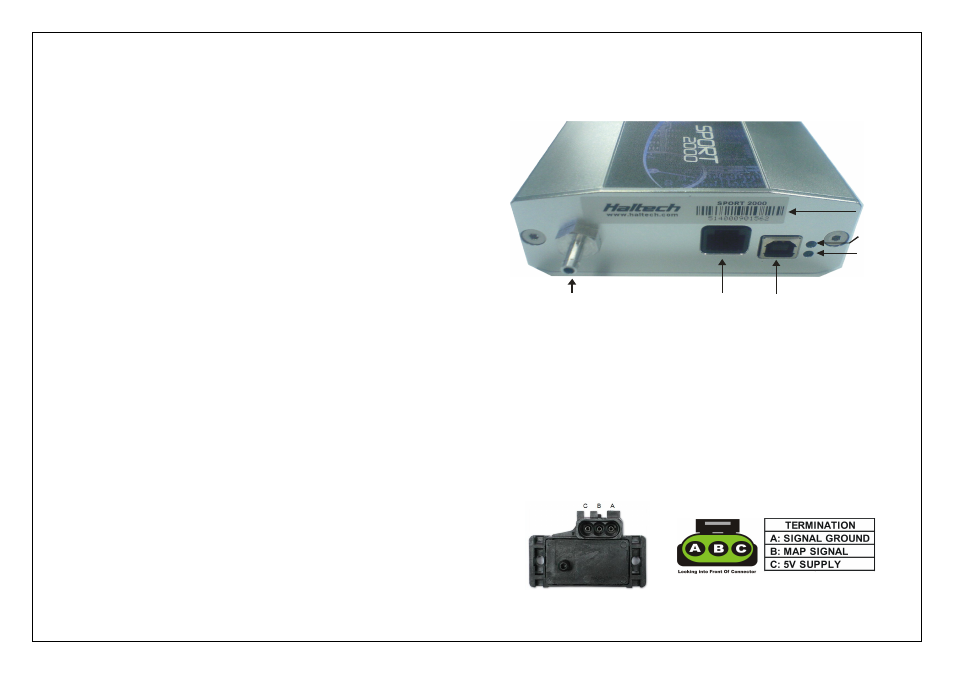
Initial Software Setup
Main Setup (Basic) Page
Set the basic engine parameters in the main setup page, number of cylinders ,
firing order, load source and map source (enable or disable the use of the internal map sensor)
Trigger Setup Page
Set the crank and cam (trigger and home) angle sensor type and description in the
Trigger setup page. If using a hall effect or optical style crank sensor then set trigger
type to hall effect.
In most stand alone applications the trigger pullup will need to be set to ON when
using a hall effect crank sensor. In a piggy back application the pullup will be set to
off. Trigger pullup will be set to off for all reluctor (sine wave) style trigger inputs.
Ignition Setup Page
Setting the base timing needs to be done with the ignition setup page open. Base
timing is the process of synchronising the ECU’s operations with the engines.
This needs to be done so that the ECU knows what the engine is doing at any point in
time. This is required for accurate fuel delivery and spark timing.
First, go to the fuel setup page and disable the fuel injectors (at this stage it is not
desired that the engine attempts to start). To reduce stress on started motor it is also
advisable to remove the spark plugs to help the engine crank more freely when
setting base timing.
Set lock timing to ON and lock timing angle to 10 degrees. Crank engine, using a
timing light connected to ignition lead for number 1 cylinder. Adjust the tooth offset
and trigger angle until timing reads 10 degrees as viewed with a timing light on
crank pulley. Tooth offset gives large changes to timing, trigger angle is used to fine
tune timing to exactly 10 degrees (any angle can be set as the lock timing angle; in
this example 10 degrees was used). It is however possible to set the lock timing to
zero degrees (or any other positive number) and adjust tooth offset and trigger
angle until the crank pulley shows this value when viewed with a timing light.
If there is no RPM being displayed in the software check for correct trigger setup, correct
sensor wiring, correct trigger type, pull ups enabled / disabled, trigger edge falling / rising.
Fuel Setup Page
Set the basic fuel parameters, injection mode, fuel pump prime time and injector resistance.
Injector resistance can be measured across the injector pins with a multimeter on the ohms
setting. Three settings are available in the software: 1-3 ohm , 3-8 ohm and high(above 8ohm).
After base timing has been set – (See ignition setup) ensure that the fuel injectors are
enabled in this setup page.
MAP Sensors
The Platinum Sport Series ECU's are fitted with an internal MAP sensor rated to
22PSI (150 kPa). Connect the internal sensor to the inlet manifold* via vacuum
hose to the external fitting on the ECU. * Tap into a high point on the inlet manifold
to avoid fuel entering the vacuum line, as damage to the sensor will occur.
Figure 4 – Internal Map Sensor Fitting
Alternatively an external MAP sensor can be fitted via the harness allowing higher
manifold pressures.
The External MAP sensor when used are usually mounted high on the engine bay
firewall or inner guard using two screws and with the hose nipple facing outwards.
Connect the sensor to the inlet manifold via a short length of vacuum hose and fasten
with either hose clamps or nylon cable ties. Connect the sensor to the main wiring
harness using the appropriate plug and harness branch. Avoid mounting the sensor
below the level of the fuel injectors, because fuel may collect in the vacuum hose and
run down into the sensor. The sensor assembly is weatherproof but it is good practice to
mount the sensor in a protected position away from moisture and heat.
Haltech can supply 1 – 5 Bar Map sensors depending on your application , alternatively
OEM map sensors can be used as long as you have the calibration information to
calibrate the sensor in the ECU Manager Software.
Figure 5 – Manifold Absolute Pressure Sensor and harness Termination
Internal Map Sensor
Vaccum Hose Fitting
CAN
Connector
USB
Connector
Blue Power
LED
Red Status
LED
Serial Number
Label