Energenics 150 Low Profile Lint Filters 2007 User Manual
Page 14
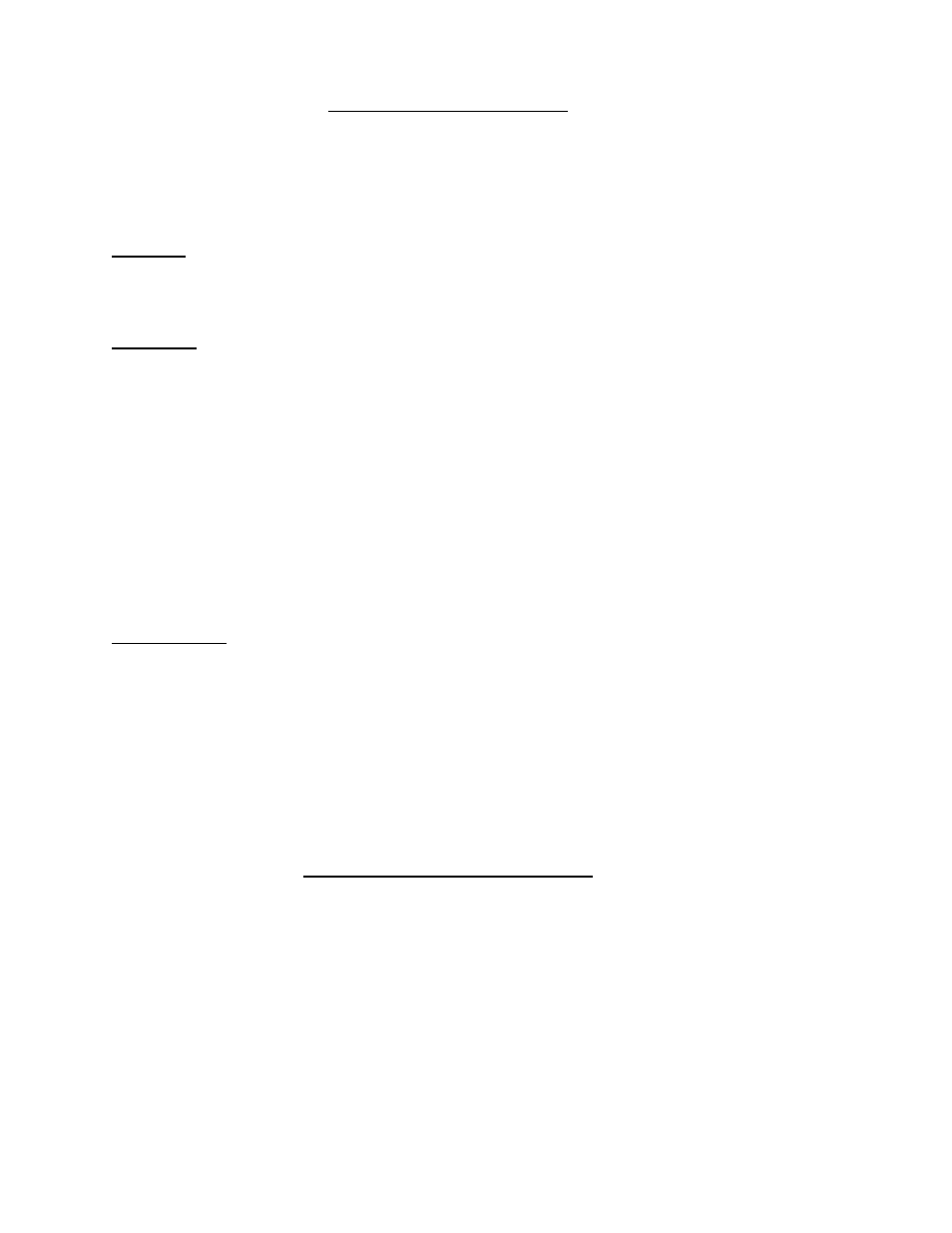
14
Maintenance Requirements
The frequency of your maintenance requirements depends upon the number of hours of
operation and upon variances in your product output. For a single-shift operation,
without special problems, the frequency recommended below should suffice. You
should set your own schedule based on your experience.
1. WEEKLY
Visually inspect the filter inside and outside, its controls and their operation. At time
of such inspection, note and correct any discrepancies from normal operation.
2. MONTHLY
Check the static pressure. Disconnect the lower pressure hose, and then use a
magnehelic gauge, manometer, or U-tube to measure and record the resistance.
This will show the pattern of operation of your system. If pressure exceeds 1 inch
W.C., insure the rotor is correctly turning and cleaning the screen.
Watch the air pressure gauge on the filter. Record the drop in pressure during the
blow down cycle. A normal pressure is from 100psi at the start to 80psi after six
seconds. The minimum pressure is 80psi. Any less will not reliably clean the
screen. If the pressure were to fall from 100psi to 40psi, the air supply is inadequate
or obstructed.
3. QUARTERLY
On filters using fire protection control, carefully test the Fenwall fire sensor accessed
through the inspection door. First disconnect the initiator/solenoid leads from the
panel and connect a 24 VDC bulb to initiator terminals in the control unit. Heat the
Fenwall fire sensor with a heat lamp or other convenient source. When the bulb in
the control unit changes state, remove heat source and allow Fenwall fire sensor to
cool. Reset control unit. Test lamp must change state and stay changed after
system is reset. Do not reconnect initiator/solenoid leads until all Fenwall fire
sensors have cooled below set point as indicated by test lamp.
FILTER SCREEN MAINTENANCE
Chemicals present in the laundry uniforms, shop towels or other linen may
eventually clog the filter screen. When this occurs, try the following:
1. Spray with an engine degreaser like GUNK. Allow soaking per the instructions
for cleaning an auto engine. Spray clean with water.
2. Operate one dryer without a load to blow hot air through the filter to dry it.
3. Restart the dryer. Operation should be perfectly normal. It should not be
necessary to replace the screen unless it is punctured.