Dynon Avionics RV-6 Roll Kit User Manual
Page 4
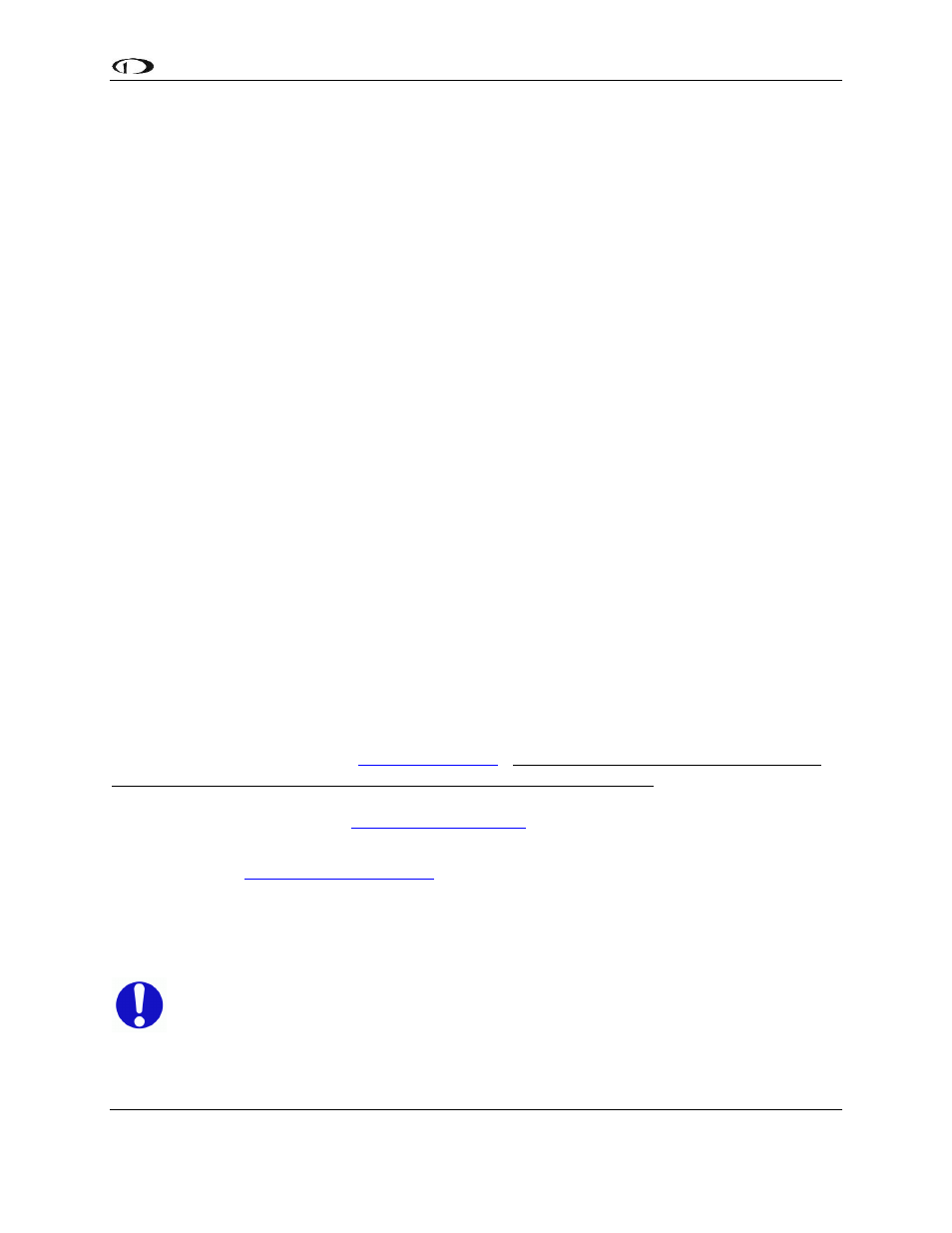
DYNON AVIONICS
Servo Mounting Instructions – RV-6 Roll Kit
3
101046-001 Rev F
With the servo installed, the linkage needs to be assembled. Refer to the illustration and follow
proper rod end installation techniques. Screw at least half of the threads on each rod end into the
push rod. To prevent the possibility of the servo arm going over-center, the servo arm
must not travel more than a total of +/-60º from neutral throughout the control system's range of
travel. The linkage should be installed as close to the Dynon recommendation as possible, as
changes will affect geometry. Dynon suggests installing the linkage at the outer-most hole of the
servo arm. Changing this location will affect servo torque output, servo arm travel, control surface
resolution, and the amount of force required to shear the safety screw, and should only be changed
if the installer has an understanding of these implications. See the diagram on the following page
which illustrates the linear travel and available force for each mount point on long-arm servos.
Standard mounting of the linkage to the servo arm will include the AN3H-10A bolt, AN970-3 large
diameter flat washer (for capturing the rod end bearing), 2 AN960-10 flat washers on each side of
the servo arm itself, and the AN365-1032A lock nut. The other end of the linkage will require the
same type of stack-up, but will need the included .600" spacer and longer bolt to clear the existing
push tube. Some trimming around push tube holes in ribs may be required over full travel to clear
the supplied linkage.
The distance between the servo arm and the control system attachment point must allow for the
angle between the servo arm and the push rod to be at approximately 90º when the controls are at
neutral. Use the adjustability in the rod ends to achieve this, and then tighten the jam nuts to lock
the rod ends in place. The illustrations show the control stick, linkage, and arm at one end of
the range of motion for clarity when viewing the servo part stack-up.
Installers should always keep in mind the range of motion of the servo. Total servo arm travel is
limited, but verify the arm/linkage do not interfere with anything during the full motion of the
control stick. The built-in control stops of the aircraft will limit the servo arm travel when installed
correctly. We recommend the use of the optional Range of Motion Limiting Bracket, supplied with
the servo to eliminate the chance of the servo arm going over-center. This bracket should not be
used as a normal stop; the aircraft's built-in stops should always be the primary range limit.
Your servo(s) and AP74/76 (if ordered) came with a CD containing the latest documentation for all
Dynon products (also available a
understand the wiring and configuration process for your Autopilot system. We also maintain a
collaborative set of this documentation, which is often updated with new information by both
Dynon and fellow builders. Vis
version of these documents.
You can also visit
suggestions with other builders.
Neglecting to properly install and/or use Dynon autopilot hardware
may result in failures which could cause loss of aircraft control
resulting in aircraft damage, personal injury or death.