Replacement parts, Theory of operation, 2 replacement parts – B&C Technologies HE Series Commercial User Manual
Page 11: 3 theory of operation
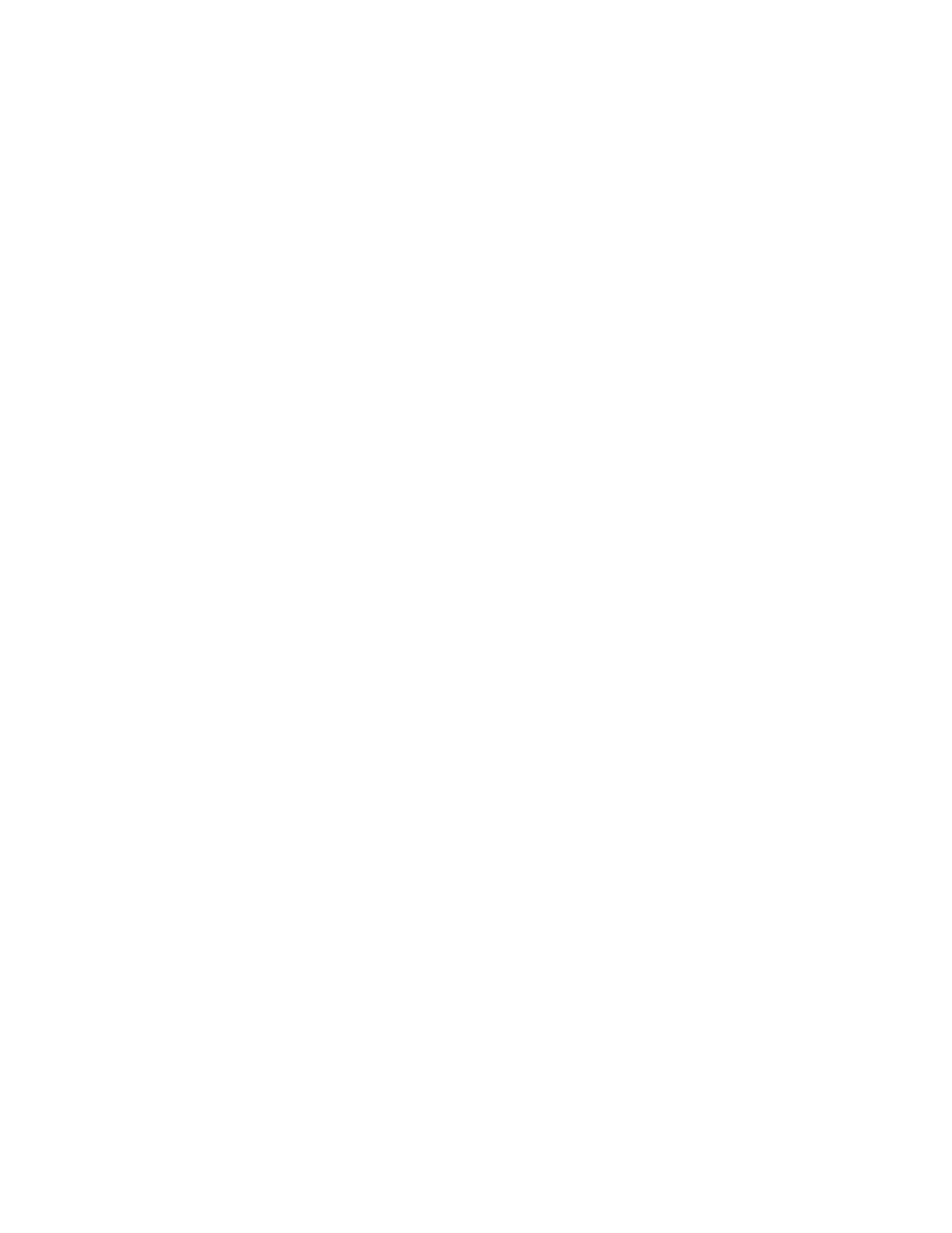
2.2
Replacement Parts
In the event that literature or replacement parts are required, contact the local distributor of the
equipment, or contact B&C Technologies at the above phone numbers/internet addresses.
2.3
Theory of Operation
The HE models use a single-speed motor to drive the cylinder via V-belts in all speeds. The cylin-
der is supported by two spherical roller bearings located in a bearing housing made of cast iron.
The motor is controlled by the computer control located in the front and the AC inverter drive
located in the rear panel. Wash and extract speeds are fixed. Any temperature between 70F to
200F (20-95C) can be programmed. The water level is fixed, with a low level and a high level pro-
vided (medium level is included with the A computer). The computers will automatically provide
safety levels for steam injections and door operations. The AC Drive performs balance detection
to ensure that excessively out of balance loads do not damage the machine or floor. A catastrophic
failure sensor is also provided to stop the machine in the event of a severe malfunction.
Water entry into the machine is through an air gap vacuum breaker utilizing electro-magnetic wa-
ter valves controlled by the computer. By utilizing the air gap vacuum breaker, backflow into the
water supply is impossible. The computer also controls the drain, supply dispenser, any external
liquid supplies, steam injection and any other vital functions of the wash program.
The steam, if installed, is injected in the bottom of the shell via a steam injector. The steam is
controlled by a steam valve that is programmed by the micro computer.
The cylinder is perforated, allowing water to pass through and drain from within during drain
and extract steps. Lifting ribs inside the cylinder lift the load from the wash solution and allow
the load to tumble and falling back into the solution when the load reaches the approximate 10-11
o’clock or 1-2 o’clock positions. This mechanical action removes soil from the fabric. Furthermore,
the lifters are perforated on the top so that water can cascade over the goods and wet them quickly.
This reduces water consumption as water is picked up at the cylinders lowest point and lifted and
splashed over the goods at the highest point as the cylinder rotates.
A stainless steel door is provided for loading and unloading. A door lock system prevents op-
eration of the machine when the door is open. The door is locked during operation utilizing an
electronic solenoid and a latch for safety reasons. The door lock is provided with magnetic sensor
to indicate that the door is closed and locked and allows for start of the machine when the door is
closed and locked.
The AC drive, circuit overload protectors, input power supply connections, external supply con-
nections, and control transformer are behind a cover on the rear of the machine.
The supply dispenser is mounted on the front of the machine and is accessed by opening the cover
door. Supplies, both liquid and powder, may be added by pulling the dispenser cups out and
placing the appropriate supply in each. Supplies are flushed into the machine at the proper time
in the cycle, controlled by the micro computer.
7