Troubleshooting, Safet y op era tion m aintenan c e setu p – Harbor Freight Tools ITEM 60738 User Manual
Page 17
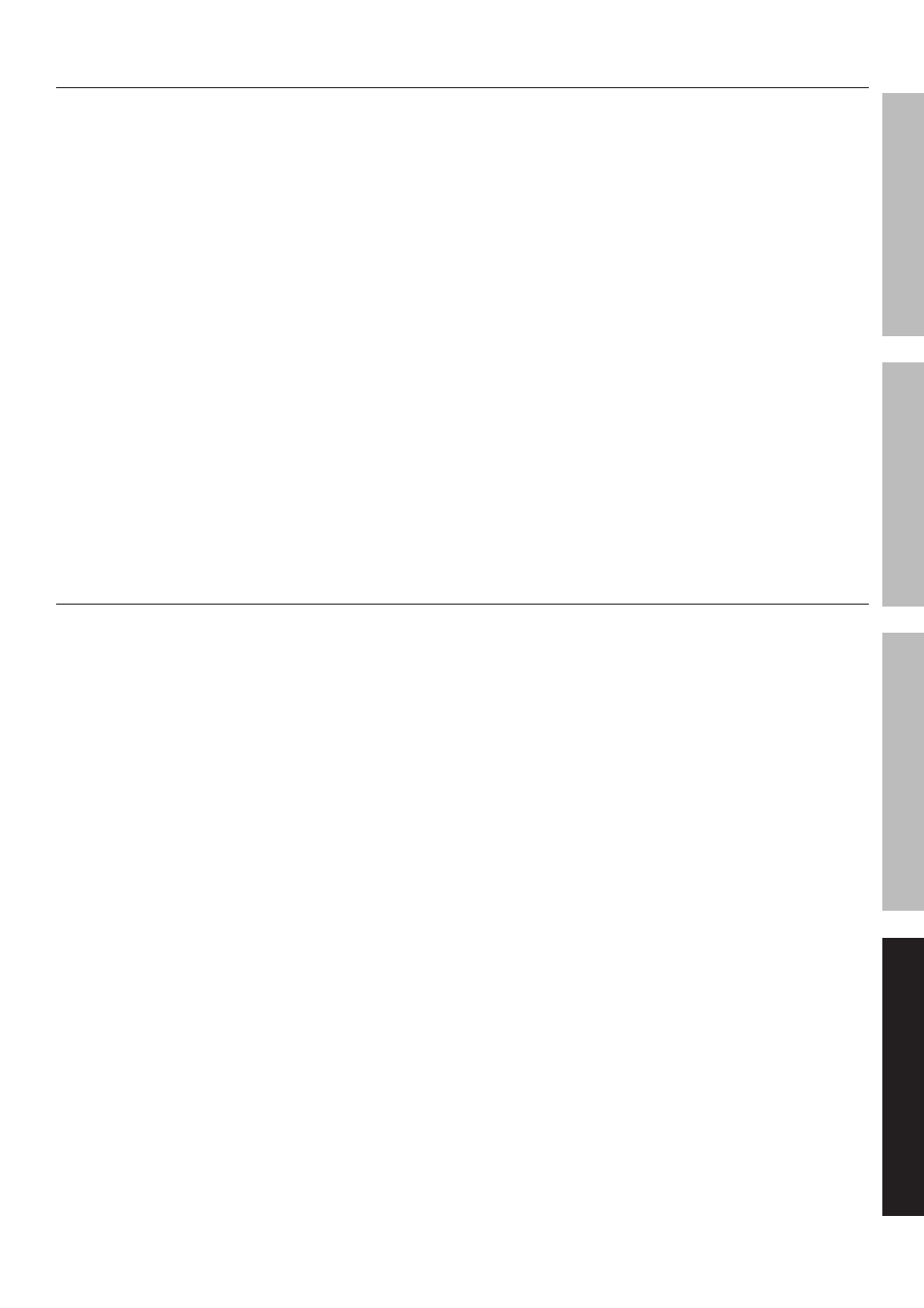
Page 17
For technical questions, please call 1-800-444-3353.
Item 60738
SAFET
y
Op
ERA
TION
M
AINTENAN
c
E
SETU
p
Troubleshooting
1.
Blast Gun. After 10 to 12 hours of blasting time,
the Nozzle (2D, 2E) should be checked. It it
shows uneven wear it should be turned 1/4 turn
every 10 hours of use. Replace as needed.
2.
caking of media. Media caking is caused by
moisture in the air supply or from oily or greasy parts.
If this is not corrected the media will not flow evenly
and will plug up in the Metering Valve (13) and Blast
Gun (4B). Check the air supply. If water is present,
install a quality moisture trap. If oily or greasy parts
are being blasted, degrease and dry the part first.
3.
Reverse pressure. If the media stops flowing
occasionally, use an object to plug the Nozzle
(2D, 2E) and press the Foot Pedal (11) down for
about two seconds. This will cause the system to
back blast through the Blast Gun (4B) and up the
media hose. This will help loosen any clogs.
4.
Blast Gun air pressure drop. Turn the Air
Regulator Knob (9) and set the air pressure to 80 PSI
as indicated on the Pressure Gauge (8). Push the
Foot Pedal (11) while holding the Blast Gun (4B), and
observe if the gauge pressure drops significantly. If
the pressure drops, this indicates there is a restriction
in the air supply line. This could indicate the air
supply hose is too small, a reducer or quick coupler,
or other piping that doesn’t allow enough air through.
Also, if the air compressor is too far away from the
Blast Cabinet a pressure drop will result. The air
supply line should be 1/2″ diameter or larger.
5.
poor visibility (excessive dust). Make
sure the Quick Coupler on the Air Regulator
(9) is allowing air to the Cabinet (22).
6.
poor visibility (viewing window). The Glass
Window (17) is equipped with a clear plastic protector
on it and may become pitted. If necessary, replace
the plastic protector and/or Glass Window.
7.
poor media flow. Check for moisture as discussed
in Step #2 of this section. Holes in media hose will
cause poor media delivery. If necessary, replace
hose. Debris in media. Replace or screen media.
Maintaining Suction Efficiency
The most common problem operators have when using a suction (venturi) Blast Cabinet is a decrease in production
rates. When production rates fall the operator can usually locate the problem by checking the following:
1.
Air supply. If the Pressure Gauge (8) on the Air
Regulator (9) shows an adequate no-load supply
(when the Blast Gun (4B) is not running), press the
Foot Pedal (11). If the pressure drops more than a
few PSI the air supply is restricted or inadequate.
Clean filters and moisture separators all the way
back to the air compressor. Straighten any kinked
hoses. Use a master gauge (not included) to check
the air pressure, or replace the existing Pressure
Gauge if you suspect it is giving you false readings.
2.
Blast Gun. The Nozzle (2D, 2E) will wear out
eventually. Replace the Nozzle if its opening
measures 1/16″ over its original size or if it shows
uneven wear. Adjust as needed for different
media and conditions. A properly working Blast
Gun (4B) will pull 15 to 17 inches of mercury
on a manometer.
(See Assy. Diagram.)
3.
Media. Use quality blast media sized to the
job. Damp or dirty media can bring blasting to an
instant halt. Store media in a dry area and load the
appropriate quantity (up to 15 pounds). Add enough
media through the Grate (39) within the Cabinet
(22) to have 6 inches deep of media on top of the
Metering Valve (13). If you run out of media as you
are blasting, add enough so it keeps circulating to
the Blast Gun (4B). The media will eventually break
down or get too contaminated to use. The less there
is in the system, the less you will have to replace.
4.
Media delivery. Replace any media hose that
has soft spots or visible wear. Adjust the Metering
Valve (13) to provide adequate flow. A mixture
that is too rich will cause pulsating at the Blast
Gun (4B). An unusually loud noise while blasting
means the mixture is too lean. A rich mixture
can result in lower impact velocities, while a
lean mixture reduces the number of impacts.