Triton ETA 100 User Manual
Page 10
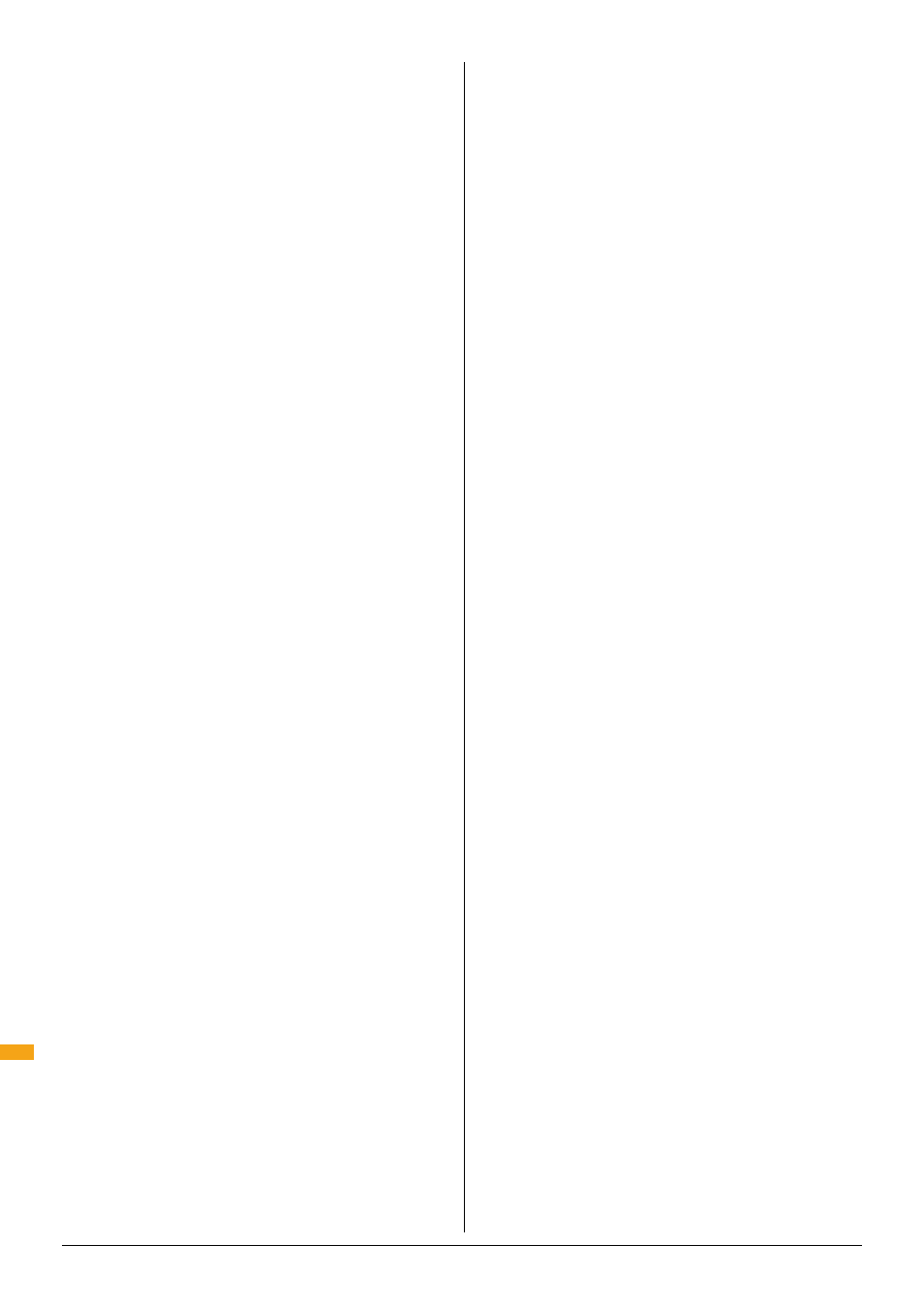
10
GB
end panel flanges. Use the brackets as a drill guide,
centre punching the hole positions toward the top
of the slotted hole in the bracket. Drill 6.5mm or
1
⁄
4
" holes.
Fit the inner track to the Workcentre by locating
the coach bolt heads through the keyholes in the
end panel brackets. Make sure that the tabs on
the bottom of the support brackets engage into the
slots on the end panel brackets. Tighten the round
knobs and then temporarily tighten the four nyloc
nuts (24) holding the inner track to the brackets.
Fig. 7
Aligning the Tracks on a Workcentre
STEP 12W
On Series 2000 Workcentres, push the legs
diagonally outwards to ensure it is fully stable.
Position the outer track parallel to the inner track
approximately 28" away from it. Place the table
onto the tracks with the inner (smaller) bearings on
the inner track. Always fit the table this way. Slide
the table to each end of its travel and adjust the
position of the outer track. The lengthened outer
bearings make this a non-critical adjustment.
STEP 13W
Next it will be necessary to fine-tune the height of
the inner track. Fit the extension table fence to the
sliding table and extend it across the Workcentre
table. Loosen the bolts and screws attaching the
end panel bracket, adjust the height of the brackets
until the bottom of the fence is around
1
⁄
32
" above
the Workcentre table, front and rear. Tighten the
bolts and Phillips screws holding the brackets to
the end panels.
STEP 14W
Next, adjust the height of the outer track until the
fence is level across the Workcentre table.
Check the sliding table throughout its travel for
diagonal rocking on the tracks, and fine tune the
height of the outer track if necessary. Adjust the
height stops on the outer track legs to lock-in the
correct height.
With the sliding table positioned midway along the
tracks, engage the front and rear locking latches
(Fig.10). Adjust the self-tapping screws on the
inner bearings until the heads enter the rectangular
windows and the table cannot be lifted. (It will be
necessary to unlock the latches and lift the table
clear to make these adjustments).
STEP 15W
The last step is to fine-tune the inner track position
in the horizontal plane, to ensure that the extension
table scales are accurate.
Series 2000 Workcentres: With the extension
table fitted and locked, and the rip fence removed,
insert the standard Workcentre rip fence and set it
to 16" using the end panel calibration marks. Prior
to sighting down the front face of the Workcentre
rip fence, loosen the four nyloc nuts on the inner
track support brackets. Adjust the inner track
sideways until both front and rear scales read
exactly 16”. Retighten the four nuts and remove the
Workcentre rip fence.
MK3 Workcentres: Extend the extension table
fence across the Workcentre until the tip is level
with the left-hand edge of the saw slot. Check for
parallel by sliding the extension table so that the
fence tip runs the length of the saw slot. Loosen
the four nyloc nuts on the inner track support
brackets and adjust the position of the track until
the fence tip aligns perfectly with the saw slot at
both ends of the table travel.
To ensure the correct scale reading, position the
extension table with the front scale level with
the front of the saw blade and measure from the
blade teeth to check the scale reading. Adjust the
position of the inner track if necessary until the
scales are accurate, ensuring the track is moved by
exactly the same amount at each end.
Finally, double check the parallel alignment and
scale accuracy by repeating the above steps, or by
making a test cut.
Your Sliding Extension Table is now fully assembled
and ready for use. Skip to the 'Operating' section.
FITTING TO A COMPACT SAW TABLE
STEP 10C
Loosely tighten the TCA/RSA Brackets (38) onto
the two inside brackets on the Inner Track using
the short Coach Bolts (40), Washers (13) and Nyloc
Nuts (24) with a 10mm spanner, as shown in Fig.
4. Note the orientation of the brackets in regard to
the long overhang of the inner track (marked "X"
in Fig. 8).
Assembly