Bendix, Ad-rp, Air dryer troubleshooting chart – Bendix Commercial Vehicle Systems AD-RP PuraGuard Oil Coalescing Remote Purge Air Dryers User Manual
Page 22
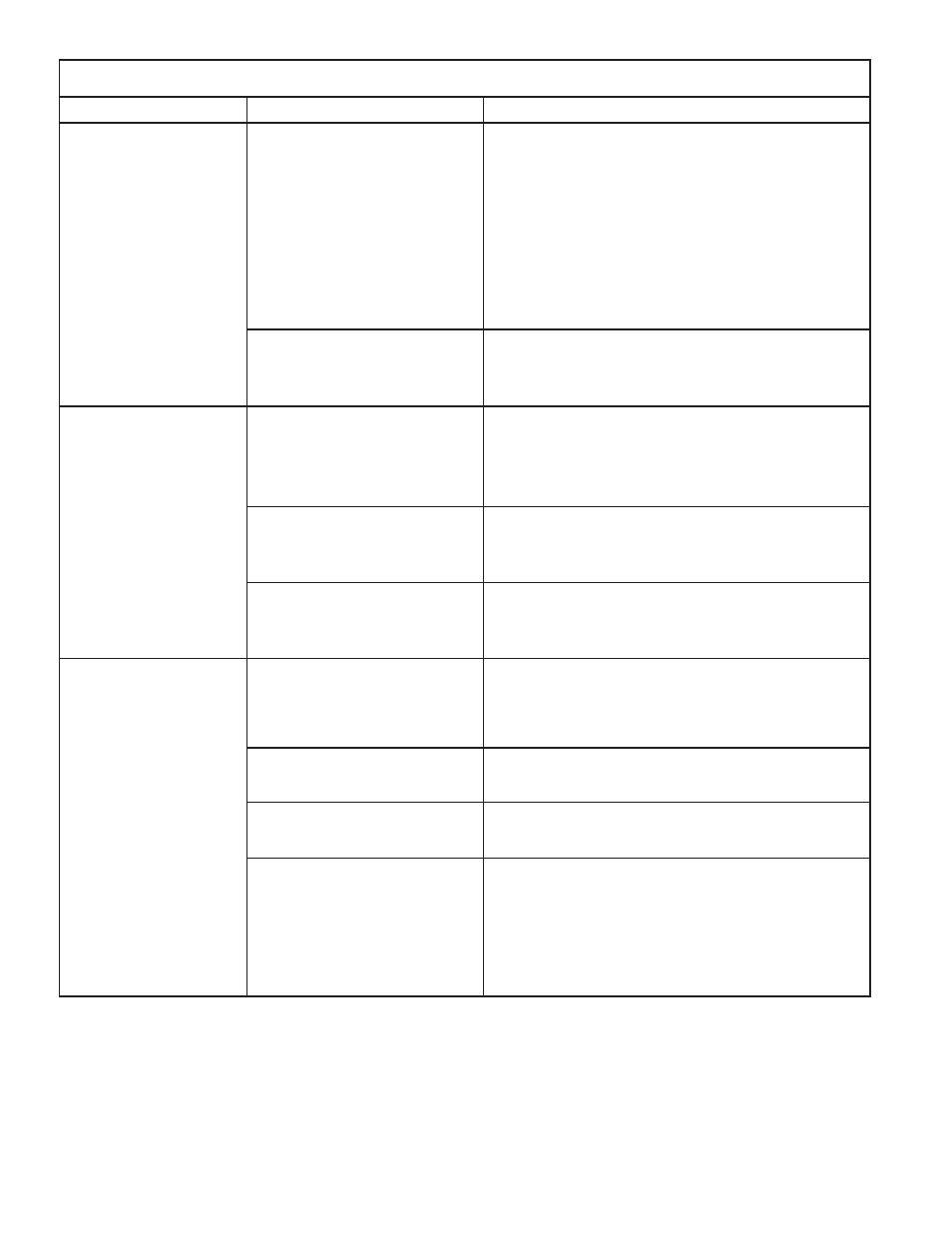
22
Bendix
®
AD-RP
™
AIR DRYER TROUBLESHOOTING CHART
SYMPTOMS
CAUSE
REMEDY
4. Air is escaping from
air dryer exhaust
during the charge
cycle, but is able
to build system
air pressure.
(Compressor
pumping.) (continued)
D. Air fl ow to the supply
reservoir is restricted.
D. Kinked, plugged, damaged hose tubing or fi ttings:
Check to determine if air is reaching the fi rst reservoir.
Inspect for kinked tubing or hose. Check for undrilled
fi ttings
or restricted hose or tubing fi ttings. Repair or
replace as necessary.
Desiccant cartridge plugged: Check compressor
for excessive oil passing and/or correct compressor
installation. Repair or replace as necessary. Replace
the desiccant cartridge.
E. Excessive pressure
pulsations from compressor.
(Typical single cylinder type.)
E. Increase the volume in the discharge line by adjusting
the length or size of line, or add a ping tank.
5. Air escaping from air
dryer exhaust port
during entire purge
cycle. (Compressor
not running.)
A. Leaking turbo cut-off valve in
Bendix
®
AD-RP
™
air dryer.
A. Note the dash gauges to verify the purge cycle has
ended. Perform the air dryer “Operation & Leakage
Tests” specifi ed in this manual. Repair or replace as
necessary.
B. Leaking purge piston o-ring
in the AD-RP air dryer.
B. Perform the Air Dryer “Operation & Leakage Tests”
specified in this manual. Repair or replace as
necessary.
C. Leaking delivery check
valve.
C. Perform the Air Dryer “Operation & Leakage Tests”
specified in this manual. Repair or replace as
necessary.
6. Unable to build air
system pressure and
air is not escaping
from the AD-RP air
dryer exhaust during
the charge cycle.
(Note: This is not the
same as symptom
4.)
A. Frozen discharge line.
A. Inspect the discharge line installation for water traps
that could freeze. Refer to “Connecting The Air Lines”
section in manual. Repair or replace as necessary.
B. Compressor unloader
mechanism malfunction.
B. Test the compressor unloader mechanism for proper
operation. Repair or replace as necessary.
C. Governor malfunction.
C. Test the governor for proper operation. Repair or
replace as necessary.
D. Air fl ow to service brake
system is restricted or
plugged. Air pressure on one
dash gauge normal with no,
or low pressure on the other
gauge.
D. Check for kinked, plugged, damaged hose tubing or
fi ttings in the air line between the supply reservoir
and low pressure service reservoir.
(continued)