Caution – S&S Cycle Pinion Shafts for Big Twin User Manual
Page 2
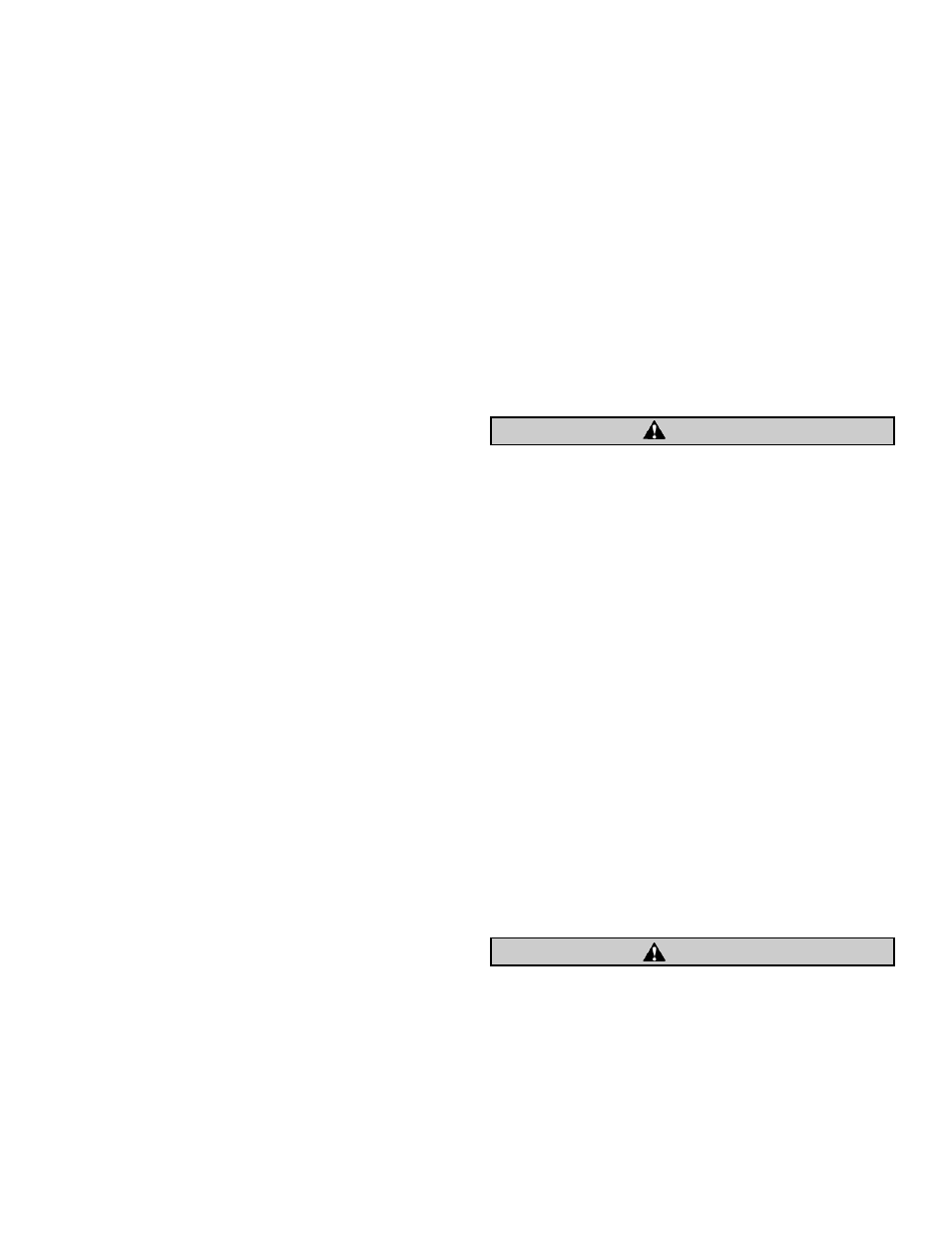
PRODUCT INFORMATION
S&S
®
pinion shaft kit, PN 33-2024, has been designed
as a composite replacement and is made to fit stock
Harley-Davidson
®
flywheels and S&S SE and L style
flywheels in 1958 to early 1981 big twin engines. It
can also be used in 1954 to 1957 engines, if
crankcases are modified. S&S PN 33-2024 shaft
effectively replaces Harley-Davidson
®
#24006-54A,
24006-58 and 24006-73.
*All reference to Harley-Davidson
®
part numbers is for
identification purposes only. We in no way are implying that any
of S&S Cycle’s products are original equipment parts or that they
are equivalent to the corresponding Harley-Davidson
®
part
number shown.
To use S&S pinion shaft 33-2024 in 1954 to1957 crankcases,
perform the following operations:
1.
Remove pressed-in bearing race in the right crankcase.
2.
Bore cast-in bearing retainer out to 2.125" to accept
larger diameter later 1958 to 1981 press-in race.
3.
A shim must be fabricated to space later pressed-in
bearing race out to earlier bearing race position.
The S&S pinion shaft kit, PN 33-2027, is designed to fit
stock Harley-Davidson
®
flywheels from late 1981 to 1989
and S&S SL and BL style flywheels for late 1981 and later
engines. S&S PN 33-2027 replaces Harley-Davidson
®
#24006-80, 24006-83 and 24006-87. S&S pinion shaft kits,
parts 33-2028 and 33-2029, are identical to 33-2027 in
design and application except they have bearing surface
diameters of +.001" and +.002" oversize respectively. S&S
Shaft 33-2028 replaces Harley-Davidson
®
#24020-87 and
shaft 33-2029 replaces Harley-Davidson
®
#24021-87.
NOTE: When using S&S 33-2027 pinion shaft in 1990 and
later engines with S&S flywheels, pre-1989 oil pump drive
gear and pinion gear must be used as stock gears for 1990
and later style, straight pinion shaft will not fit S&S shaft.
INSTALLATION PROCEDURE
1.
Thoroughly clean shaft and blow air through oil holes
in both ends of shaft to insure no foreign material is
trapped in oil passageway.
2.
33-2024 only - Press brass plug in gear cover end of
shaft until it bottoms against shoulder in hole. For
engines 1954 to 1972 with side oiling gear covers, use
solid plug. For 1973 to early 1981 engines with end
oiling gear covers, use plug with
3
⁄
32
" hole.
NOTES:
●
When S&S pinion shaft 33-2024 is used in 1973 to 1981
engines with end oiling gear covers, side oiling feed
hole for 1954 to 1972 engines does not have to be
plugged. Amount of oil lost through side oil feed hole
in bearing surface of shaft is insignificant if gear cover
bushing is fit correctly to end of pinion shaft.
●
In 1954 to 1972 engines, oil is fed to connecting rods
once per revolution, through an oil hole inside of
pinion shaft bearing surface. Oil hole in pinion shaft
aligns with oil feed hole in pinion shaft bushing pressed
in gear cover. Later engines, 1973 to present, feed oil
continuously to connecting rods through a hole in end
of pinion shaft. Before proceeding, check your gear
cover to determine which of these oiling systems your
engine uses. Early engines from 1954 to 1972 which
have been converted with a special gear cover bushing
to oil connecting rods using 1973 to present style oiling
methods require brass plug with drilled oil metering
hole - follow instructions for 1973 and later engines.
●
If a 1972 or earlier gear cover is converted to end feed
style oiling, or if a groove is machined around bearing
surface of pinion shaft to allow oil to feed
continuously, low oil pressure will result unless
crankcase and oil pump are also updated to 1973 and
later oiling system.
●
Low oil pressure due to use of 1973 and later style
end oiling pinion shaft in 1972 and earlier engines
may cause overheating, premature wear, and
damage to engine components.
●
Installing solid end plug in 1973 and later engines will
result in insufficient oil flow to connecting rods,
causing premature wear and damage to connecting
rod bearings and other internal engine components.
3.
Inspect key ways and oil holes in flywheels for burrs.
Remove burrs if necessary.
NOTE: S&S does not recommend lapping tapers to remove
burrs. This practice tends to distort the taper by removing
material unevenly around the circumference. This makes
flywheels difficult if not impossible to true. In addition the
lapping process work hardens the surface of the taper. The
resultant hard surface makes it very difficult to pull shaft
into taper. Lapped flywheel tapers are also very difficult to
resurface if repairs are ever needed.
4.
Check keys in key ways of shaft. Keys should be light
hand press fit in key ways. If key is too tight in key
way, sand side of key with fine sand paper on a metal
plate or other flat surface. Do not hammer key into
key way.
Hammering tight key into key way may result in
irreparable damage to shaft.
2
CAUTION
CAUTION