Operational precautions, Maintenance – Duff-Norton EM1050-200 (TAP) User Manual
Page 7
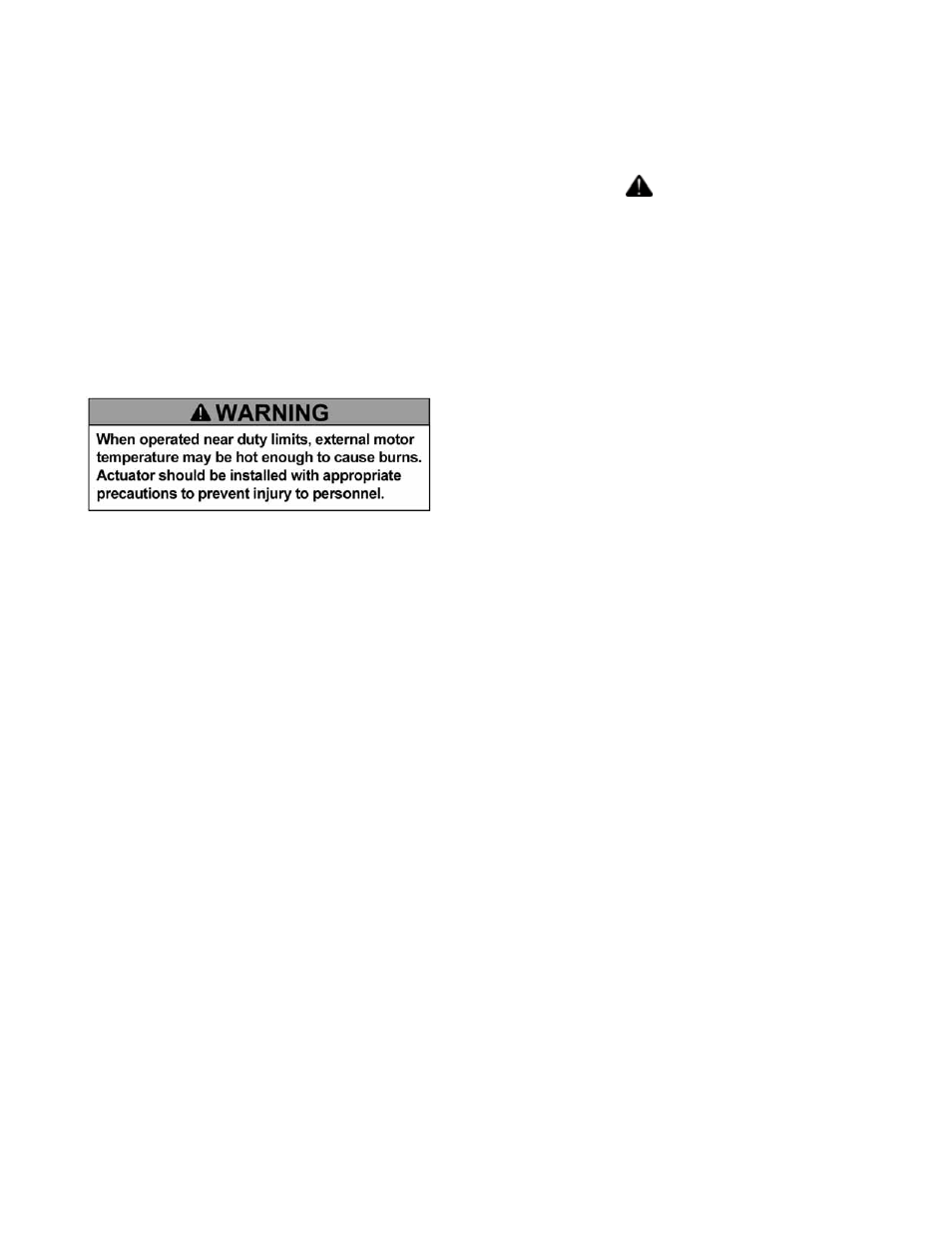
7
Section III
Operational Precautions
3-1. Motor
The motor used on this actuator has a very high
power output for its size. Consequently, heat
generation in the motor is more rapid than in more
conventional motors. Duty cycle limitations must be
recognized at all times, whether or not the actuator is
loaded.
Motors are equipped with thermal protectors to
guard against winding burnout. Once tripped , it may
take 10 – 15 minutes for the motor to cool sufficiently
to reset the thermal protector. Repeated thermal trips
can be an indicator of excessive load or duty, low
voltage, or weak capacitor(AC only).
3-2. Clevis
Pins
The clevis pins must be maintained parallel to each
other during the full stroke of the actuator. Side
loading or torquing as a result of non-parallel clevises
can cause serious actuator damage. Any creaking
noise at the clevises is an indication that pins need
lubrication to prevent pin wear.
3-3. Jamming
Actuators with limit switches have no inherent
mechanical overload protection. Repeated jamming of
the actuator, internally or against an external stop, will
result in very rapid wear and eventual failure. Be sure
that limit switches are functioning properly to stop the
actuator within its stroke limits.
No-load operation will produce additional drift. Limit
switches should be set far enough from ends of stroke
to accommodate this if no-load operation is
anticipated.
Actuators with clutches have a degree of protection
against internal or external jamming or overloading;
however, extended slipping of the clutch will cause
accelerated wear and premature actuator failure. To
provide acceptable long-term operation at rated load,
clutches are set somewhat above rated load. Do not
depend on the clutch to gage an acceptable load.
Clutches are not adjustable for wear.
Section IV
Maintenance
4-1. Lubrication
The load bearing and the screw and translating tube
are adequately lubricated for the life of the unit.
Gearing receives a light brush coat of grease at the
factory. If the actuator is removed for repair or
inspection, the gear lubricant may be replenished by
filling the gear tooth spaces with a heavy, tacky gear
grease. A few drops of oil should be placed on the
porous bronze bearings at the same time.
4-2. Disassembly
Remove the one Phillips head screw from the gear
housing and the four hex head screws from the tube
flange. Separate housing and housing plate. All
mechanical parts should now be accessible. The lifting
nut is threaded and staked to the translating tube.
Disasssembly of the screw and translating
tube assembly is not possible nor anticipated to be
necessary, due to the expected long life of the screw
and lifting nut.
4-3. Load Bearing
The bearing is permanently lubricated and not readily
relubricated. A bearing which shows any sign of
roughness should be replaced. Clamp screw in a vise
with soft jaws and remove retaining nut. Use thread
locking adhesive on nut when replacing bearing.
4-4. Reassembly
Assembly is the opposite of disassembly, with no
special techniques required. Tube flange screws are
self-tapping style and should be started by hand to
avoid possible cross-threading.
CAUTION