Duff-Norton Ball Screw Translating User Manual
Page 6
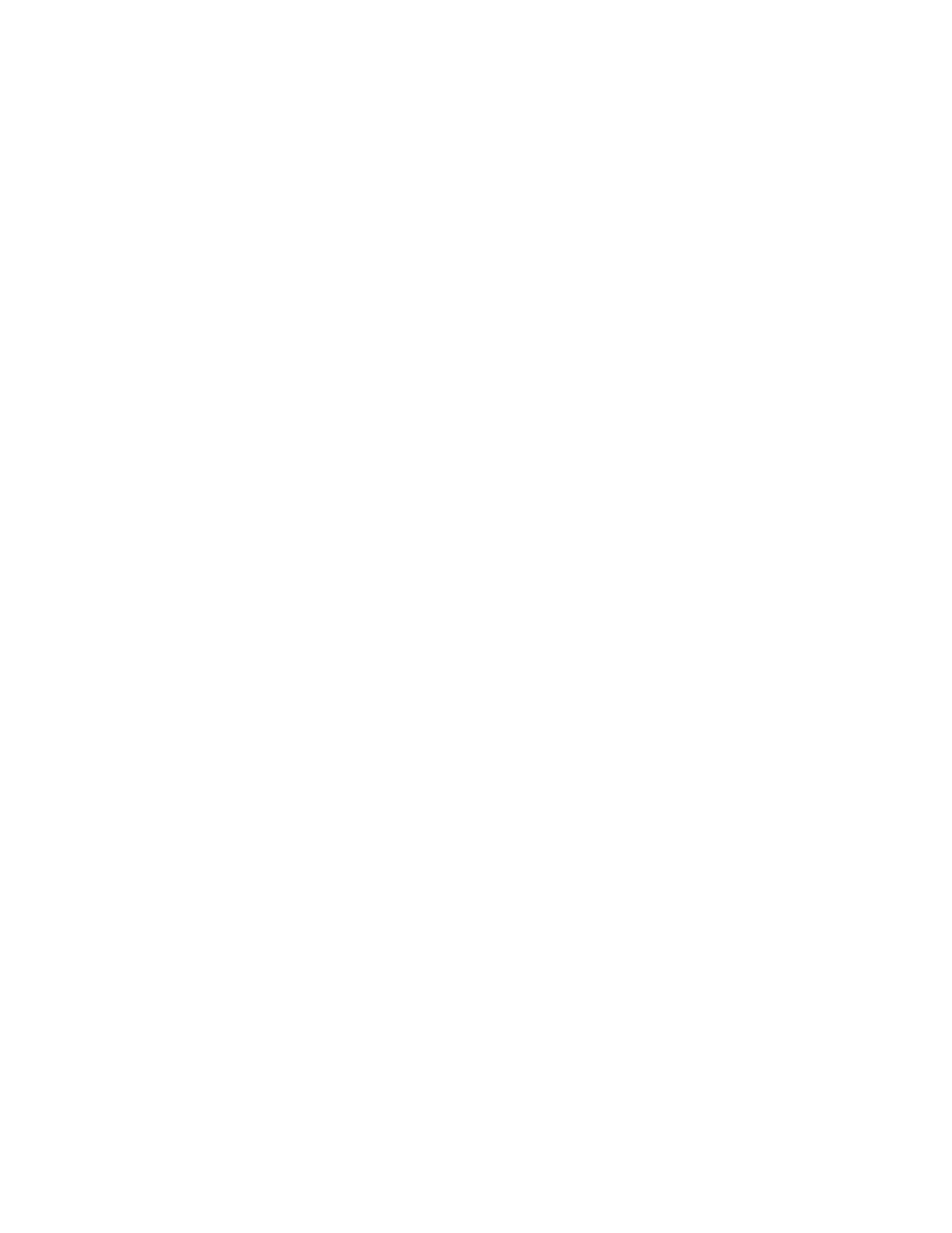
6
pressed air.
Note
Before installing new parts, remove any rust
preventive, protection grease, etc.
2-6. Inspection
1. Make a visual inspection of shell (3) for broken,
cracked or distorted areas. Check threads of all
bores for burrs or broken threads.
2. Check shell cap (2), bottom pipe (5), worm gear
assembly and flanges (16) for burrs or scratches
on their working or mating surfaces.
3. Check small common components (screws, etc.)
and replace as required.
4. Check bearings (4), (8), and (20) for seizure,
galling or play and replace as required.
5. Inspect the ball nut assembly (7) and ball screw
(6) as follows:
A. Lubricate the ball nut assembly and ball
screw. See paragraph 2-1.
B. Inspect the ball screw grooves for signs of
excessive wear, pitting, gouges, corrosion,
spalling or brinelling. It is usually less expen-
sive to replace the ball screw when any of
the above conditions exists. If you feel,
however, that it can be reworked, return it to
Duff-Norton for final evaluation.
C. If none of the above conditions exist, check
backlash. Secure the ball screw in a table
clamp or similar fixture. Make sure that the
screw shaft cannot rotate. Push firmly on the
ball nut assembly, first in one direction and
then in the opposite direction. This axial
movement of the ball nut assembly is the
backlash. While making sure that neither
member rotates, measure the backlash with
a dial indicator.
Note
Measure backlash at points of maximum
usage. Backlash of .001" to .010" is accept-
able.
D. If the backlash is over .010" and the ball
screw appears usable, order a replacement
ball nut.
2-7. Assembly
1. Press worm bearings (20) onto worm shaft (19)
making sure bearings are seated properly. When
roller bearings are used, the small end of the
cone should point to the worm end.
Note
If tapered roller bearings are used, tap worm
bearing cups into place in the shell.
2. Position worm (19) in shell (3).
3. Press oil seals (18) into worm flanges (16).
Note
The sealing elements should point inward.
4. Position worm flanges (16), with shims (17), and
bolt in place.
5. Strike each end of worm shaft sharply with a
soft face hammer to seat bearings properly.
Check flange bolts for tightness. Worm should
turn freely with minimum drag and end play. If
too much end play is present, remove shims as
required. If worm does not turn freely, add shims
as required.
6. Drop bottom load bearing (8) into shell (3).
Note
If the ball nut assembly (7) has not been re-
moved from the ball screw (6), go on to step 8. If
the ball nut assembly has been removed from
the ball screw, proceed with step 7.
7. The ball nut assembly (7) should be on the ball
screws (6). To assemble the worm gear (10) on
the ball nut, remove the retaining disc (13) from
the ball screw. Slip the worm gear onto the ball
screw. Slip the worm gear onto the ball screw
with the threaded counterbore facing the mating
thread on the ball nut.
8. Replace the retaining disc (13) on the ball screw
(6).
9. With the ball nut assembly (7) clamped in a
table clamp, screw the worm gear (10) onto the
ball nut assembly and draw up tight.
10. Tighten the worm gear set screws (9).
Note
If new parts have been installed, or if parts are
not tightened to the original factory setting, it will
be necessary to respot holes for these screws.
11. Install worm gear-ball nut and screw assembly
into the shell. Be sure the gear is seated prop-
erly in the bottom load bearing (8).
12. Screw bottom pipe (5) into shell (3) (upright
models) or into shell cap (2) (inverted models).
13. Fill housing approximately half-full with grease
and brush a very light coat of lubricant on ball
screws (6). See paragraph 2-1.
14. Remove tape from end of the ball screws (6)
and slide top bearing (4) onto the screw. Be