Transmitter adjustment, Fault diagnostics, 3 electrical connection 0 v output signal – WIKA T91.20 User Manual
Page 2: 4 electrical connection 4 ma-loop, 2 thermocouple input, 1 preparation, 2 adjustment of the 0 … 10 v output signal, 3 adjustment of the 4 … 20 ma output signal, 4 closing steps
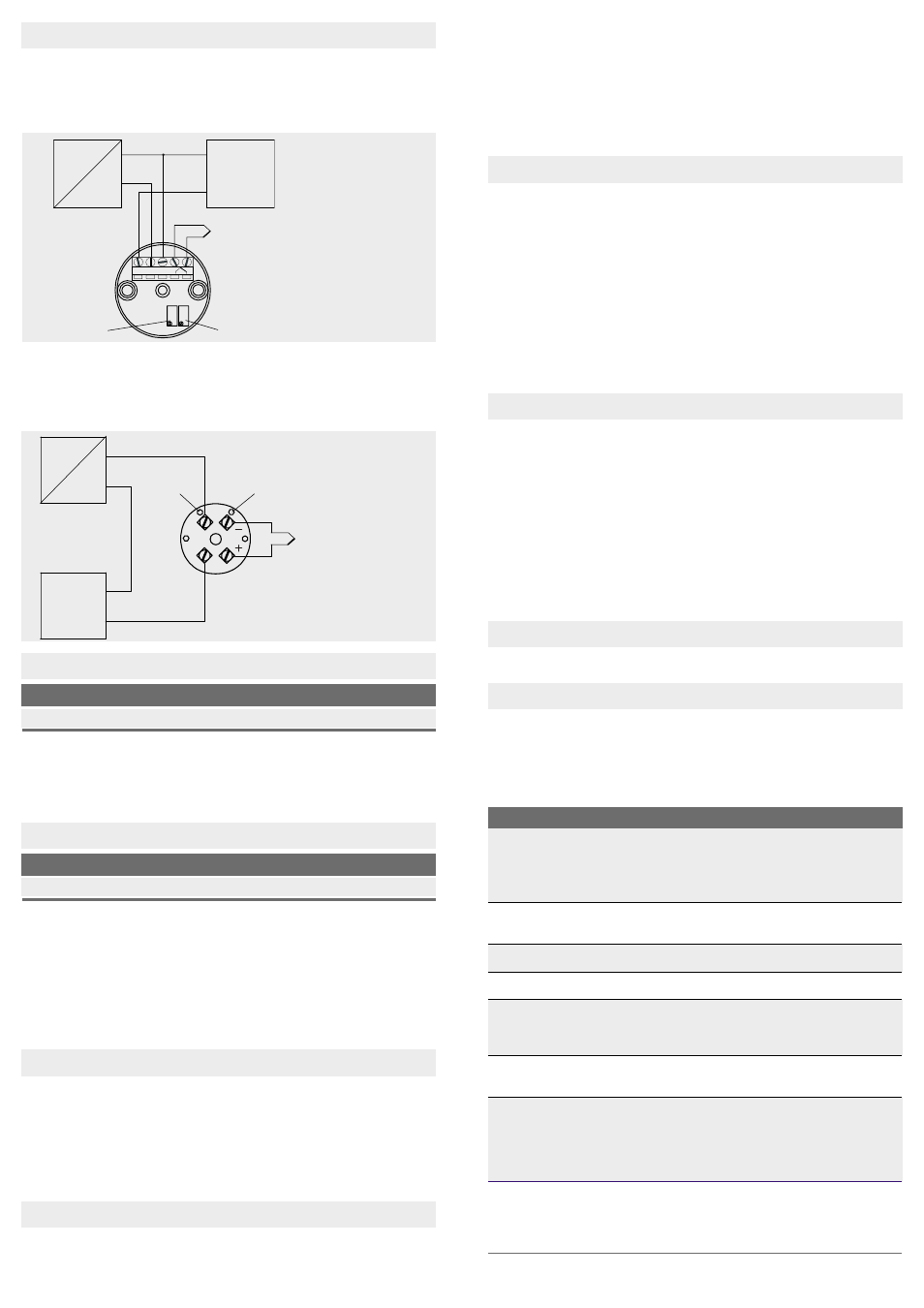
-
-
-
+
+
+
0..10V
+24V GND
1 2 3
4 5
+
-
230 VAC
24 VDC
Load
(PLC, PC)
Thermocouple
C_102.01
Zero
Span
230 VAC
24 VDC
Load
(PLC, PC)
Thermocouple
C_141.01
Span
Zero
-
-
+
+
Loop
4.3 Electrical connection 0 ... 10 V output signal
Model
Terminals
T91.10
1 (+signal), 2 (+24 V), 3 (-GND)
4.4 Electrical connection 4 ... 20 mA-loop
Model
Terminals
T91.20
loop + / -
4.2 Thermocouple input
Model T91.10.102
The positive lead of the thermocouple is connected to terminal
TC+ on the transmitter and the negative lead to terminal TC-.
Transmitter output signal: 0 ... 10 V / 3-wire design
Model T91.20.141
The positive lead of the thermocouple is connected to terminal
TC+ on the transmitter and the negative lead to terminal TC-.
Transmitter output signal: 4 ... 20 mA / 2-wire design
Maximum power supply: 15 …35 VDC
(reverse-polarity protected)
The output voltage follows the applied input signal linearly. Please
note that the output can only be regulated to within approx. 0.002
V at the lower supply voltage. (model T91.10.424 approx. 0.02 V).
Maximum power supply: 10 …35 VDC
(reverse-polarity protected)
In the current loop the transmitter and the indicator/processor are
connected in series. The transmitter regulates the current in
proportion to the input signal. The load can be connected either to
the positive or negative terminals of the transmitter. With the load
connected to the positive terminal, the power supply and load
may not have a common earth.
5. Transmitter adjustment
Zero point and Span adjustment is carried out via potentiometers.
These are on the upper face of the transmitter.
The potentiometers are protected against accidental alteration.
The zero-point potentiometer can be adjusted to make small
corrections. After any adjustment of the span potentiometer,
a complete adjustment of the transmitter is necessary.
5.1 Preparation
Connect a suitable simulation source to the input of the T91
(Pt100 or thermocouple simulator). When simulating a Pt100,
connect the simulator in a 2- or 3-wire configuration. We re-
commend the use of passive resistances.
When simulating a thermocouple, the actual terminal temperature
of the transmitter must be pre-set on the simulator (Cold Junction
Compensation).
T
Connect a mA meter in the 4 ... 20 mA-loop or a multimeter to
the 0 … 10 V output signal
T
Connect a suitable power supply to the transmitter
5.2 Adjustment of the 0 … 10 V output signal
1) Set the simulator with approx. 1 V offset from the lower limit of
the measuring range (e.g. -20 °C = 1 V for measurement range
-30 ... +70 °C)
2) Turn the zero potentiometer Z, until the output signal (in our
example -20 °C = 1 V output signal) matches the desired value
3) Set the end value of the measurement range with the simulator,
e.g. +70 °C for measurement range -30 ... +70 °C
4) Turn the span potentiometer S, until the output signal (in our
example 70 °C = 10 V) matches the desired value.
5) Repeat step 1 and check signal (1 V)
6) Repeat step 3 and check signal (10 V)
5.3 Adjustment of the 4 … 20 mA output signal
1) Set the lower value of the measurement range with the
simulator, e.g. -30 °C for measurement range -30 ... +50 °C
2) Turn the zero potentiometer Z , until the output signal shows
the desired value
3) Set the end value of the measurement range with the simulator,
e.g. +50 °C for measurement range -30 ... +50 °C
4) Turn the span potentiometer S, until the output signal shows
the desired value
5) Repeat step 1 and check output signal of zero point
6) Repeat step 3 and check output signal of span
5.4 Closing steps
Disconnect the simulator, the multimeter and the power supply
6. Fault diagnostics
When measuring with resistance thermometers or thermocouples,
factors arising from the design and measuring technology used
can falsify the results measured. The most important effects that
can lead to faults are listed below:
Error
Possible cause
No voltage output
- No supply voltage
- Display unit not working
- Circuit interruption in the supply line
- 4-20 mA output: polarity in the loop is
not correct
Output signal
1) 0 V / < 4 mA
- Short circuit in the Pt100
2) corresponds to room temperature
- Short circuit in the thermocouple
Output signal
- Sensor break
> 10 V / > 20 mA
Temperature read out
- Poor lead insulation resistance
too low/fluctuates
Read out obviously
- Moisture in the sensor or in the senor
too high or too low
wire
- Not correct compensation wire or
incorrect thermocouple
If the measuring point is
- Thermocouple polarity incorrect
heated up the output signal
reduces
When only one pole of the
- Electromagnetic disturbances are
thermocouple is connected,
coupled to the input lead
a value is still displayed
- Through poor galvanic isolation, and
poor insulation, parasitic voltages are
present, e.g. through the thermal
insulation
Displayed value obviously
- Electromagnetic disturbances are
incorrect
coupled to the input lead
- Parasitic galvanic voltages, e.g. as a
result of moisture in the compensation
cable insulation