Chemglass CG-1171-20 User Manual
Page 5
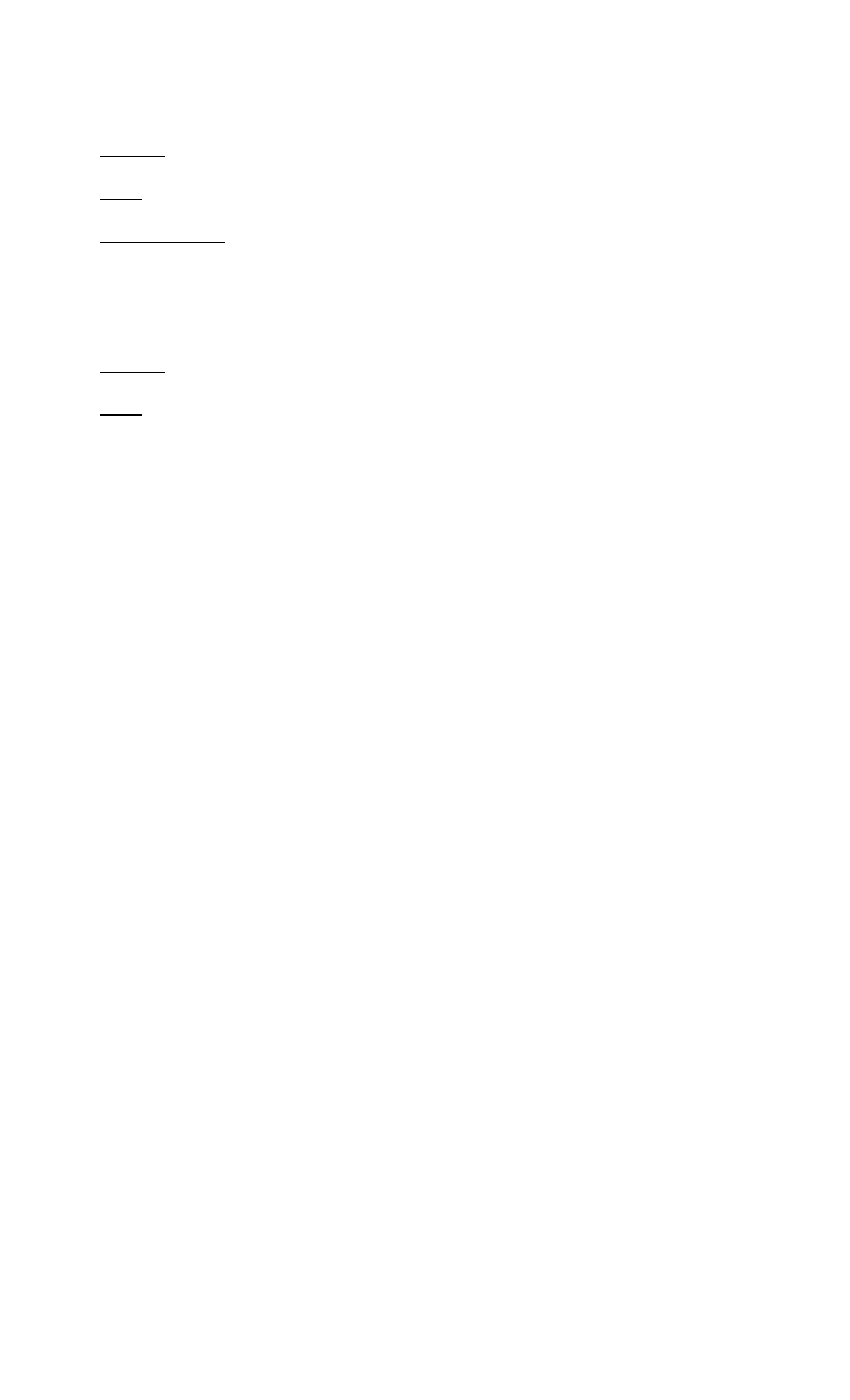
8 Error
Messages
8.1
Possible LED Error Messages
In order to cancel the error message press the On/Off
button.
Error No 1:
LED’s blink, Standby symbol lights up. Pump turns
off after 5 seconds.
Cause:
Pump was running against pressures over the
allowed limit.
Solving the Problem:
➊
Reduce the pressure.
➋
Change the flow rate.
→
If the cause of error No 1 is not removed
within 5 seconds, then the pump goes to
error No 2.
Error No 2:
All LED’s blink, Standby symbol lights up. Pump
turns off.
Cause:
Pump was running against pressures over the
allowed limit.
Solving the Problem:
➊
Reduce the pressure.
➋
Change the flow rate.
➌
Start the pump.
10 Technical
Data
10.1 LIQUIPORT®
Flow Rate
1
(L/min)
0.5 to 3
MAX Suction (ft H
2
0) 10
MAX Pressure Head (PSIG)
14.7
Pump Weight
2
(gram)
1,500
MAX Ambient Temp (°C)
+5 to +40
MAX Temp of Liquid (°C)
+5 to +80
MAX Viscosity of
Liquid
(cSt)
150
Head Material
Polypropylene
Diaphragm Material
PTFE
Valves FFPM
Protection Type
IP65
Protection Class
III
1
Measured with water at 20°C and pressure
0mWg.
2
The weight can vary depending on the individual
version.
10.2 CE-Marking
The LIQUIPORT®-Diaphragm liquid pumps are in
accordance with the following standards:
– EN 61010 – 1
– EN 60529
– EN 61326 – 1
EN
55022
EN
61000-4-6
EN
61000-4-3
EN
61000-4-4
EN
61000-4-2
EN
61000-4-5
EN
61000-4-11
EN
61000-3-2
EN
61000-3-3
9 Troubleshooting
Before working on the pump, ensure the power supply
is isolated.
➨ Motor Fails To Start
■ Pump is not connected to power supply.
■ Power supply is switched off.
■ The pressure in the delivery line from the pump is
too
high.
■ Pump is on “STANDBY“ → ON-/OFF button not
pressed.
■ External controlling is connected without input
signal.
➨ Pump Not Sucking Liquid In
■ Suction side of pump is not connected.
■ Liquid level in container is too low.
■ Hose connections are leaking.
■ A system valve is closed, or blocked.
■ The pump head is filled with gas. The gas
pressure after the pump can not be overcome
because of its compressibility in the working
chamber.
■ Diaphragm and/or valves are worn out or dirty.
➨ Flow Rate, Suction Height, or Pressure Height
Is
Insufficient.
■ The periphery installation contains components
(hoses, valves, filters, etc…) which create too
much
resistance.
■ Hose connectors are not tight.
■ Diaphragm or valves are worn out or are covered
in
dirt.
-- 5 --