Alpine VOLUME 1.3 User Manual
Page 11
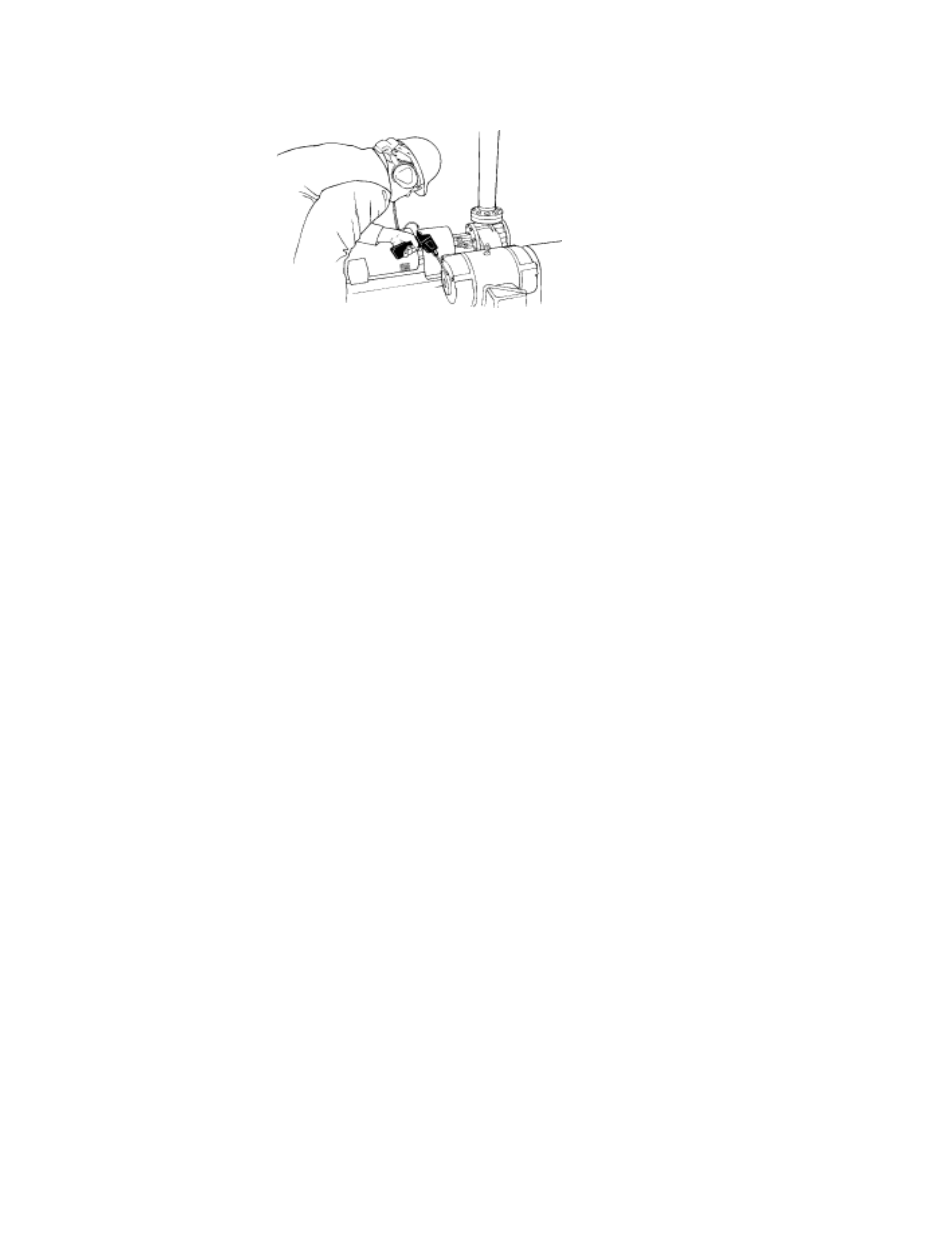
3. DETECTING BEARING WEAR
Ultrasonic inspection and monitoring of bearings is by far the most reliable method for detecting incipient bearing
failure. The ultrasonic warning appears prior to a rise in temperature or an increase in low frequency vibration
levels. Ultrasonic inspection of bearings is useful in recognizing:
a. The beginning of fatigue failure.
b. Brinelling of bearing surfaces.
c. Flooding of or lack of lubricant.
In ball bearings, as the metal in the raceway, roller or ball bearing begins to fatigue, a subtle deformation begins to
occur. This deforming of the metal will produce an increase in the emission of ultrasonic sound waves.
Changes in amplitude of from 12 to 50 times the original reading is indication of incipient bearing failure. When a
reading exceeds any previous reading by 12 db, it can be assumed that the bearing has entered the beginning of the
failure mode.
This information was originally discovered through experimentation performed by NASA on ball bearings. In tests
performed while monitoring bearings at frequencies ranging from 24 through 50 kHz, they found that the changes
in amplitude indicate incipient (the onset of) bearing failure before any other indicators including heat and vibra-
tion changes. An ultrasonic system based on detection and analysis of modulations of bearing resonance frequen-
cies can provide subtle detection capability; whereas conventional methods are incapable of detecting very slight
faults. As a ball passes over a pit or fault in the race surface, it produces an impact. A structural resonance of one of
the bearing components vibrates or "rings" by this repetitive impact. The sound produced is observed as an in-
crease in amplitude in the monitored ultrasonic frequencies of the bearing.
Brinelling of bearing surfaces will produce a similar increase in amplitude due to the flattening process as the balls
get out of round. These flat spots also produce a repetitive ringing that is detected as an increase in amplitude of
monitored frequencies.
The ultrasonic frequencies detected by the Ultraprobe are reproduced as audible sounds. This "heterodyned"
signal can greatly assist a user in determining bearing problems. When listening, it is recommended that a user
become familiar with the sounds of a good bearing. A good bearing is heard as a rushing or hissing noise. Crack-
ling or rough sounds indicate a bearing in the failure stage. In certain cases a damaged ball can be heard as a
clicking sound whereas a high intensity, uniform rough sound may indicate a damaged race or uniform ball damage.
Loud rushing sounds similar to the rushing sound of a good bearing only slightly rougher, can indicate lack of
lubrication. Short duration increases in the sound level with "rough" or "scratchy" components indicate a rolling
element hitting a "flat" spot and sliding on the bearing surfaces rather than rotating. If this condition is detected,
more frequent examinations should be scheduled.
-9-
bearing shot