Dake Elecdraulic - 905 series User Manual
Page 12
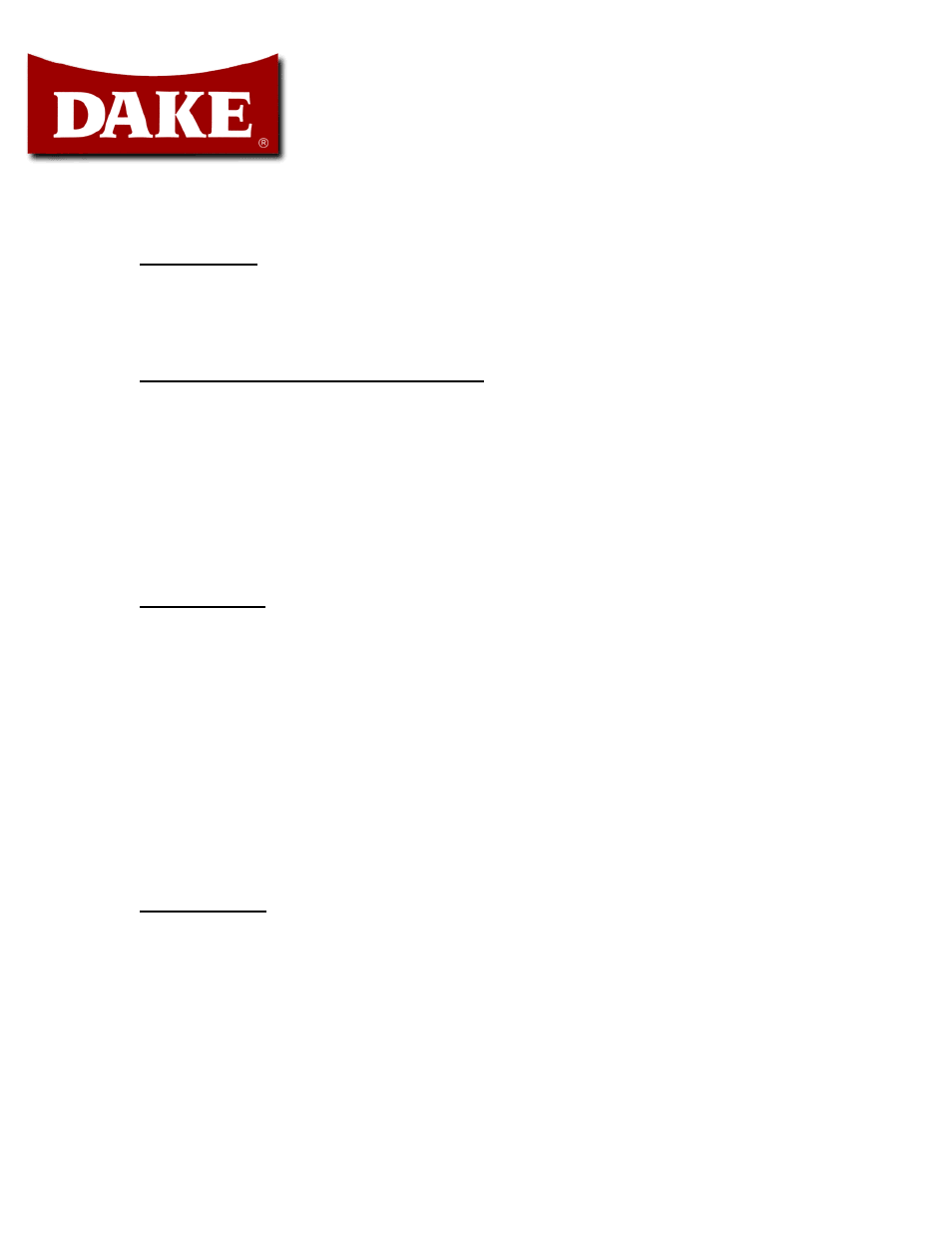
Model 5-025, 5-050, 5-075 & 5-150
12
INSTRUCTIONS AND PARTS LIST FOR
Models 50-101
¾ GPM Hydraulic Pump
Variable volume – stem control
I.
DESCRIPTION
This unit is a five-piston axial type piston pump designed for heavy-duty industrial application up to
6000 psi continuous and 8000 psi intermittent. The pump should be coupled directly to the driving
source and can be rotated in either direction.
II.
TYPICAL VARIABLE VOLUME CONTROLS
A. Stem control – with control stem out (spring return), output delivery is zero gpm – pushing in on
control stem increases pump delivery from zero to maximum gpm.
B. Knob control – With control knob adjusted out (counter-clockwise rotation), output delivery is
zero gpm – turning control knob clockwise increases pump delivery from zero to maximum gpm.
C. Pressure compensated – Circuit operating pressure is controlled by setting of compensator
valve mounted on pump. Turning adjusting knob clockwise increases circuit pressure, counter-
clockwise decreases circuit pressure. Output delivery of pump at zero circuit pressure is
maximum gpm – when circuit pressure reaches the setting of compensator valve, pump output
automatically decreases to supply the exact flow rate required by the system.
III.
INSTALLATION
A. Rotation – Pump shaft rotation can be in either direction.
B. Shaft alignment and pump mounting – The alignment of the pump and motor is critical, having a
direct relation to pump bearing and shaft seal life as well as coupling life. A flexible coupling
should always be used.
C. Fluid connections – Pressure and intake line piping should correspond to port sizes to keep fluid
velocities in an n acceptable range. Do no bush down to smaller sizes.
D. Safety valves – The high-pressure line must have a relief valve close to the high-pressure outlet
to prevent damage to pump. In a circuit using the pressure compensated pump, the relief valve
should be set several hundred psi above compensator pressure to minimize transient pressures
due to compensator overtravel.
E. Filtration – Cleanliness of fluid and components is of extreme importance in high-pressure
hydraulic circuits. A suction strainer of 140 microns or less and twice pump capacity should be
used in the pump inlet line.
IV.
MAINTENANCE
A. Minor repairs – Minor repairs are considered those that do not involve total disassembly of
pump. External leaks around the pump, for example, can usually be eliminated by tightening
screws and/or fittings around the leakage area. Replacement of leaking shaft or o-ring seals is
a minor repair that can be done in the field. The Dake service manual should be consulted for
the necessary part numbers.
B. Major repairs – Major field repairs can be accomplished in an emergency. However, it is
recommended that the Dake factory be contacted for necessary parts and assistance. Dake
pumps are built to give long-term dependable service. If they should eventually require
overhaul, factory rebuilding is recommended when possible since disassembly and assembly
can damage many parts. This minimizes replacements, with net savings to the user.