Lake Monitors FlowStat ES Sensor (Plastic) User Manual
Page 3
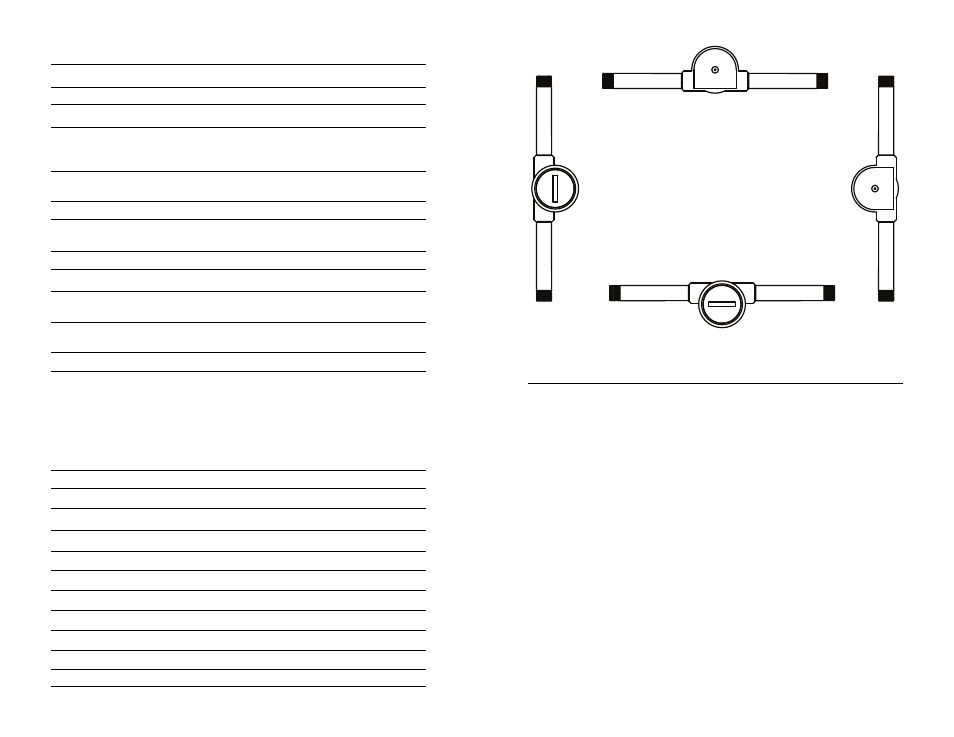
Mechanical Specifications
FLOW SENSOR WITH STAINLESS STEEL BODY
Maximum pressure:
200 PSI clear cover, 500 PSI SS cover
Maximum temperature: 225ºF
Measuring range*
1/2" NPT Ported:
0.5 - 15 GPM
3/4" & 1" NPT Ported:
1.5 - 50 GPM
Wetted materials:
316SS, acetal copolymer, Buna, PEEK
and polycarbonate
Non-wetted materials:
Epoxy, Lexan
®
and PVC
FLOW SENSOR WITH POLYPROPYLENE BODY
Maximum pressure:
150 PSI
Maximum temperature: 150ºF
Measuring range*
1/2" NPT Ported::
0.5 - 15 GPM
Wetted materials:
316SS, acetal copolymer, Buna, PEEK,
polycarbonate and polypropylene
Non-wetted materials:
Epoxy, Lexan
®
and PVC
*Important: Chose a maximum flow rate. For 1/2": 5 - 15 maximum GPM.
For 3/4" and 1": 15 - 50 maximum GPM. Minimum flow rate will
be 10% of maximum flow rate. Example: If your maximum flow
rate is 8 GPM, the minimum flow rate would be .8 (8 x .1 = .8).
Thus, the correct flow range would be .8 - 8.0 GPM.
Electronic Specifications
ALL VERSIONS WITH 4-20 MA CIRCUIT
Power requirements:
12-35V
DC
, 20mA
Load driving capacity:
Max. Load (
Ω
) = 50(Power Supply Voltage - 12)
Trans. Distance:
limited only by wire resistance & supply voltage
LED:
provides power indication
Flow rate accuracy:
±2% of full scale
Repeatability:
±0.5% of scale
Resolution:
infinite
Response time:
2 seconds to 90%
Over-current protection: self limiting at 30mA
Fail safe indication:
4 mA
(10)
Installation - Mechanical
1. The FlowStat has NPT (National Pipe Thread) plumbing con-
nections. Lake Monitors recommends that a paste type pipe
sealant be used on these threads. [Thread sealant can
be used as long as it is applied in such a way that it will not enter
the flow stream. Pieces of thread seal tape can wrap around the
turbine and impede its rotation.]
2. The recommended mounting orientation would be any plane that
will place the axis of the turbine horizontal with respect to the
ground. See Illustration 1. The unit will operate satisfactorily with
its axis at angles other than horizontal, but side loading of the
bearing surfaces will lead to premature wear of the rotating parts.
3. For the best flow measurement results, place the inlet (See Note 1)
of the flow sensor at least 10 straight pipe diameters down-
stream from any fitting, valve, elbow, reducer, etc. that causes
non-stable flow conditions. Ideally, 5 straight pipe diameters should
be placed at the outlet of the sensor. If the sensor must be placed
closer to a source of non-stable flow than these recommended dis-
tances, some instability of the output signal may result. The aver-
age signal will be accurate.
(3)
Illustration 1:
Mounting Instructions