Troubleshooting, Important, Warranty – SANDPIPER EB80M User Manual
Page 4
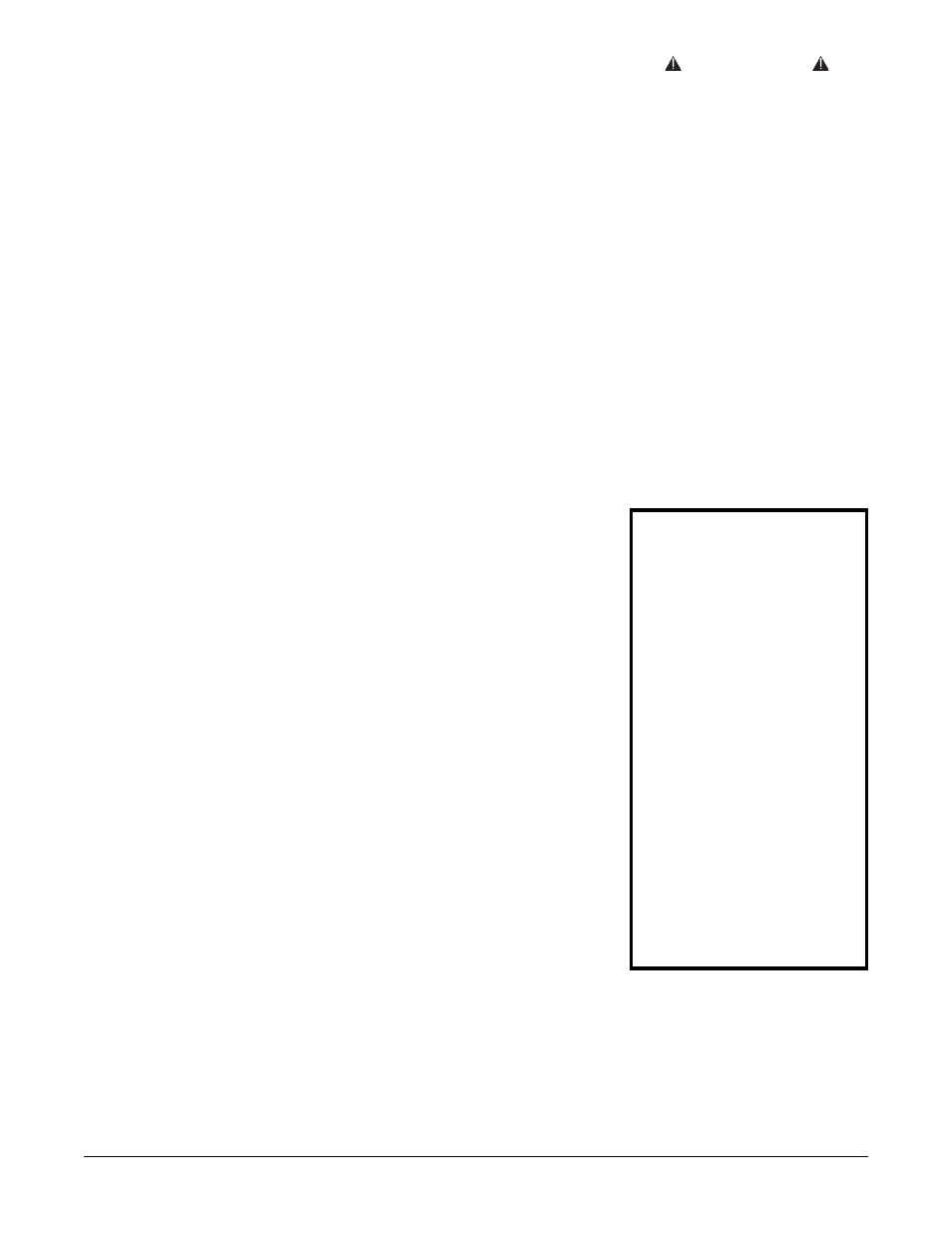
Page 4 Models EB3-M/EB4-M/EB80M
520-143-000
8/00
RECOMMENDED
WARREN RUPP
ACCESSORIES
TO MAXIMIZE PUMP
PERFORMANCE:
• Tranquilizer
®
Surge Suppressor:
For nearly pulse-free flow.
• Warren Rupp Filter/Regulator:
For modular installation and
service convenience.
• Warren Rupp Speed Control:
For manual or programmable
process control. Manual
adjustment or 4-20mA reception.
For more detailed information on
these accessories,
contact your local Warren Rupp
Factory-Authorized Distributor,
or Warren Rupp corporate
headquarters.
diaphragm plate. Install the inner plate with the flat face against the diaphragm.
After all components are in position in a vise and hand tight, tighten with a wrench
to approximately 50 ft. lbs. (67.79 Newton meters) torque. After both diaphragm
assemblies have been assembled, thread one assembly into the shaft (hold the shaft
near the middle in a vise with soft jaws, to protect the finish). Install this sub assembly
into the pump and secure by placing the outer chamber on the end with the diaphragm.
This holds the assembly in place while the opposite side is installed. Torque the last
diaphragm assembly to 40 ft. lbs. (54.23 Newton meters). This final torquing will lock
the diaphragm assemblies together. Place the remaining outer chamber on the open
end and loosely tighten the bolts. Replace the manifold assemblies to square the
flanges before final tightening of the remaining bolts. Alternating for progressive
tightening, the eight capscrews that secure outer chamber to inner chamber.
TROUBLESHOOTING
1. Pump will not cycle
A. Check to make sure the unit has enough pressure to operate and that the air inlet
valve is open.
B. Check the discharge line to insure that the discharge line is neither closed nor
blocked.
C. If the spool in the air distribution valve is not shifting, check the main spool. It must
slide freely.
D. Excessive air leakage in the pump can prevent cycling. This condition will be
evident. Air leakage into the discharge line indicates a ruptured diaphragm. Air
leakage from the exhaust port indicates leakage in the air distribution valve. See
further service instructions.
E. Blockage in the liquid chamber can impede movement of diaphragm.
2. Pump cycles but will not pump
A. Suction side of pump pulling in air. Check the suction line for air leaks and be sure
that the end of the suction line is submerged. Check flange bolting. Check valve
flanges and manifold to chamber flange joints.
B. Make certain the suction line or strainer is not plugged. Restriction at the suction
is indicated by a high vacuum reading when a vacuum gauge is installed in the suction
line.
C. Check valves may not be seating properly. To check, remove the suction line and
cover the suction port with your hand. If the unit does not pull a good suction (vacuum),
the check valves should be inspected for proper seating.
D. Static suction lift may be too high. Priming can be improved by elevating the suction
and discharge lines higher than the check valves and pouring liquid into the unit
through the suction inlet. When priming at high suction lifts or with long suction lines
operate the pump at maximum cycle rate.
3. Low performance
A. Capacity is reduced as the discharge pressure increases, as indicated on the
performance curve. Performance capability varies with available inlet air supply.
Check air pressure at the pump inlet when the pump is operating to make certain that
adequate air supply is maintained.
B. Check vacuum at the pump suction. Capacity is reduced as vacuum increases.
Reduced flow rate due to starved suction will be evident when cycle rate can be varied
without change in capacity. This condition will be more prevalent when pumping
viscous liquids. When pumping thick, heavy materials the suction line must be kept
as large in diameter and as short as possible, to keep suction loss minimal.
C. Low flow rate and slow cycling rate indicate restricted flow through the discharge
line. Low flow rate and fast cycling rate indicate restriction in the suction line or air
leakage into suction.
D. Unstable cycling indicates improper check valve seating on one chamber. This
condition is confirmed when unstable cycling repeats consistently on alternate
exhausts. Cycling that is not consistently unstable may indicate partial exhaust
restriction due to freezing and thawing of exhaust air. Use of an anti-freeze lubricant
in an air line lubricator should solve this problem.
For more information, consult the Warren Rupp Industrial Troubleshooting Guide.
©2000 Warren Rupp, Inc. All rights reserved.
®Warren Rupp,SandPIPER, and Tranquilizer are
registered tradenames of Warren Rupp, Inc.
Printed in U.S.A.
IMPORTANT
Before pump operation, all external
gasketed fasteners must be inspected
for looseness caused by gasket creep
after leaving the factory. Retorque loose
fasteners to insure against leakage.
Follow recommended torques where
called out. (A card is attached to each
new pump stating this fact.)
This pump is pressurized internally with
air pressure during operation. Always
make certain that all bolting is in good
condition and that all of the correct
bolting is reinstalled during assembly.
WARRANTY
This unit is guaranteed for a period of
five years against defective material
and workmanship.