Pressure supply, Hydraulic fluid return, Suction strainer – SANDPIPER SB1 1/2-H User Manual
Page 2: Maintenance after use, Check valves, Diaphragms, Caution
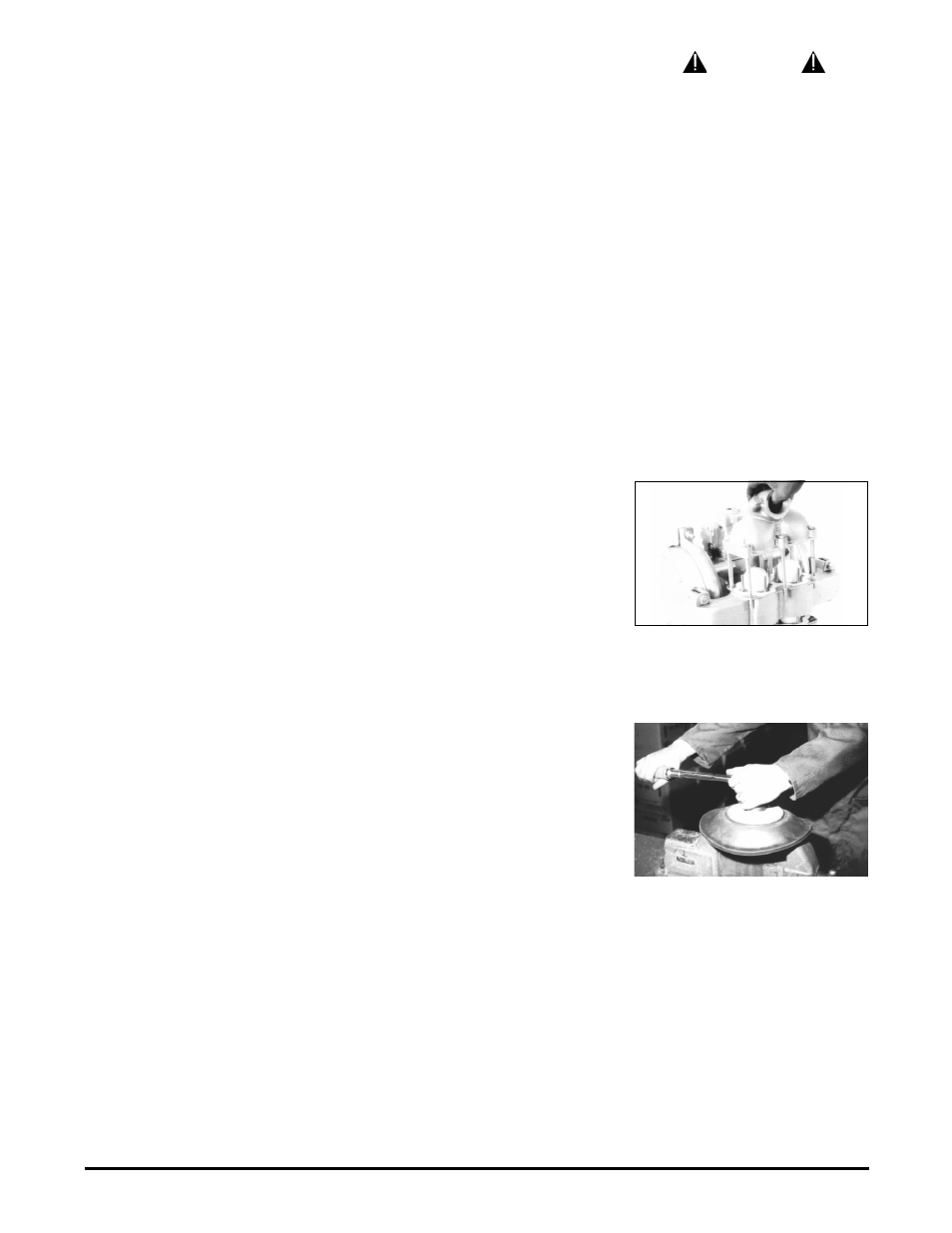
Model SB1½-H Page 2
520-029-000 8/99
PRESSURE SUPPLY
Do not connect the unit to a pressure supply in excess of 125 PSI (8.61 bars).
Connect the pump inlet port, denoted by a P on the end cap, to a hydraulic supply of
sufficient capacity and pressure as required for desired performance.
HYDRAULIC FLUID RETURN
The SandPIPER pump has two return ports. One is on the intermediate and the
other is on the end cap, denoted by a T. Both ports must be connected to the
hydraulic reservoir, either separately or manifolded into a common line. Piping for
the return should not be smaller than 1" pipe size.
SUCTION STRAINER
When pumping liquids that may contain solids larger than
1
/
4
" (.635 cm) in diam-
eter, a suction strainer should be installed to avoid clogging of ball valves.
MAINTENANCE AFTER USE
When SandPIPER is used to handle materials that settle out or transform from
liquid to solid form, care must be taken after each use and during idle periods to
remove and flush these materials as required.
To drain liquid from pump, turn the unit over on the suction and discharge mani-
fold side. This position puts the chamber ports down and allows ball checks to fall
away from the seats to permit complete drainage of the unit. This procedure is
important to insure complete draining in freezing weather.
On permanent installations, chambers can be drained by removing the pipe plugs
in the outer chambers.
CHECK VALVES
For best priming and most efficient pumping performance, it is important to main-
tain check valves and valve seats in good condition for proper sealing. Need for
inspection or service ot ball valves is usually indicated by poor priming, unstable
cycling, reduced performance, or when the pump cycles but will not pump.
Inspection and service of check valves requires the removal of six bolts which
provides access to all four ball valves and both suction and discharge valve seats.
New rubber ball check valves are 2
1
/
4
" (5.715cm) diameter and will require replace-
ment when worn to approximately 2" (5.08 cm) diameter (Fig. 1).
DIAPHRAGMS
Need for inspection or service of a diaphragm is usually indicated when the unit
pumps from one chamber only and hydraulic fluid is discharged out the pump dis-
charge port or when liquid being pumped is discharged through the hydraulic return
line. To service diaphragms, remove the V-Band clamp and two hex nuts which
secure the chamber port to the manifold. To remove diaphragms, loosen the dia-
phragm assembly (outer plate, diaphragm, inner plate) by turning out of the shaft
using a wrench. A 1" (2.54 cm) square lug is provided on the outer plate for this
purpose. Removal of the opposite outer chamber will permit removal of the second
diaphragm assembly and shaft as a unit. To disassemble the diaphragm assem-
blies, clamp the inner diaphragm plate around the outer diameter between the jaws
of a vise while you turn the outer diaphragm plate loose using a wrench. Interior
components consisting of shaft seals and sleeve bearings are now accessible for
service if required.
All procedures for reassembling the diaphragms are in reverse of previous in-
structions for disassembly. The diaphragms are to be installed with their natural
bulge outward or toward the outer diaphragm plate. Make sure the inner plate is
installed with the flat face against the diaphragm (Fig. 2).
After all components are in position in the vise and hand tight, tighten with a
wrench to approximately 40 ft. Ibs. (5.53 kilograms/meters) torque. After each dia-
phragm assembly has been made, thread one assembly into the shaft (hold the shaft
near the middle in a vise having soft jaws to protect finish). Install this sub assembly
into the pump and secure by placing the outer chamber on the end with the dia-
phragm. This will hold the assembly in place while the opposite side is installed.
Make sure the last diaphragm assembly is torqued to 30 ft. Ibs. (4.147 kilograms/
meters). This final torquing will lock the diaphragm assemblies together. Place the
remaining outer chamber on the open end and secure. Snug the flange bolts of the
chamber to port manifold to square the flanges before the final tightening of the V-
CAUTION
Should a diaphragm fail, the product
and/or fumes from the product being
pumped can enter the hydraulic side of
the pump or the hydraulic fluid can enter
the product side of the pump depending
on which side offers the least
resistance. The hydraulic fluid should
be periodically checked for pumped
product contaminants and/or a
changing of the hydraulic fluid level in
the reservoir. Shut off valves should be
installed on all piping, hydraulic and
product sides, to and from the pump.
These valves should be closed when the
unit is going to be idle for an extended
time to ensure that a siphoning effect
does not develop.
Figure 2: Torquing the diaphragm plate.
Figure 1: Inspection of check valves.