Air supply, Externally serviceable air distribution system, Caution – SANDPIPER MP07D User Manual
Page 2: Danger
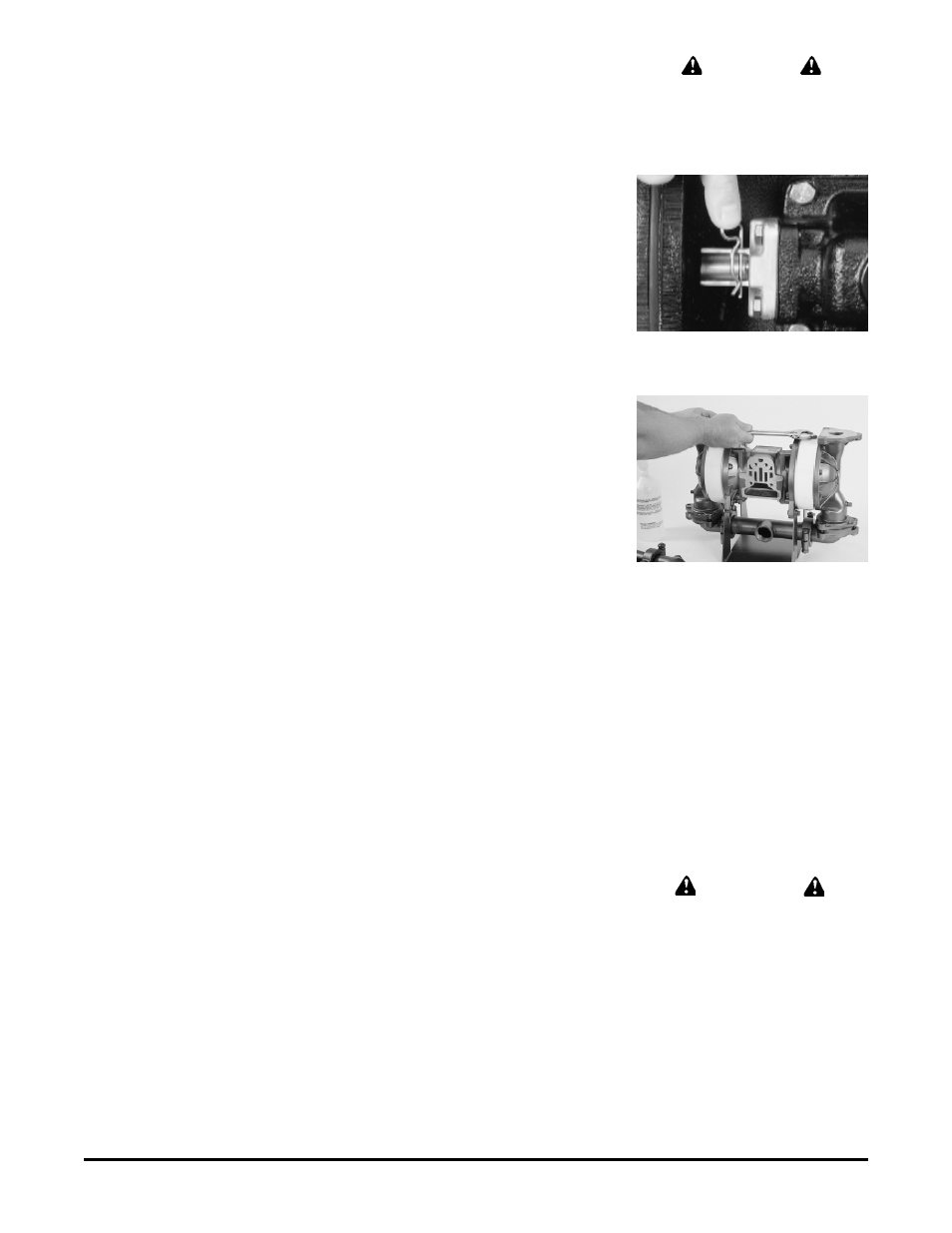
Model MP07D Design Level 3 Type 4 Page 2
520-134-000 3/03
1. Filling is accomplished through the pipe plugs at the top of the liquid driver
chamber. Remove the plugs.
2. Remove the entire discharge manifold assembly exposing the ports in the
outer diaphragm chambers.
3. With 5-10 PSI of air pressure at inlet, lock the spool to one side with locking pin
(safety clip; item 61) (Fig. 1). You will fill the opposite side diaphragm from the
“Locked Area.”
4. Fill with 2500MI. (84.53 fl. oz.) by volume with the driver liquid. It is imperative
that the driver liquid chambers be filled with the correct amount of driver liquid as too
little or too much will cause premature diaphragm failure and erratic pumping.
5. After filling with the proper amount of liquid, if the liquid does not come to the
top of the fill hole, pressure should be applied to the Teflon diaphragm with a blunt
tool through the material flow port in the outer chamber until it does come to the top.
Relieving air pressure will relax diaphragms at this point.
6. When the driver fluid rises to the top of the fill plug hole, screw the boss plug,
with o-ring installed, into the chamber. (Do not overtighten.) (Fig. 2) Remember to
keep pressure on the Teflon diaphragm until the boss plug is tight to prevent air from
drawing back into the chamber.
7. Filling the opposite side is accomplished in the same manner as described.
AIR SUPPLY
Do not connect the unit to an air supply in excess of 125 PSI (8.61 bars). Install
a shutoff valve in the air supply line to permit removal of the unit for servicing. When
connecting an air supply of rigid piping, mount a section of flexible line to the pump
to eliminate piping strain. In permanent installations, an air line filter is
recommended.
A NOTE ABOUT AIR VALVE LUBRICATION
The Marathon pump’s pilot valve and main air valve assemblies are designed to
operate WITHOUT lubrication. This is the preferred mode of operation. There may
be instances of personal preference, or poor quality air supplies when lubrication of
the compressed air supply is required. The pump air system will operate with
properly lubricated compressed air supplies. Proper lubrication of the compressed
air supply would entail the use of an air line lubricator (available from Marathon) set
to deliver one drop of 10 wt., non-detergent oil for every 20 SCFM of air the pump
consumed at its point of operation. Consult the pump’s published Performance
Curve to determine this.
It is important to remember to inspect the sleeve and spool set routinely. It
should move back and forth freely. This is most important when the air supply is
lubricated. If a lubricator is used, oil accumulation will, over time, collect any debris
from the compressed air. This can prevent the pump from operating properly.
Water in the compressed air supply can create problems such as icing or
freezing of the exhaust air causing the pump to cycle erratically, or stop operating.
This can be addressed by using a point of use air dryer (available from Marathon) to
supplement a plant’s air drying equipment. This device will remove excess water
from the compressed air supply and alleviate the icing or freezing problem.
EXTERNALLY SERVICEABLE AIR
DISTRIBUTION SYSTEM
Please refer to the exploded view drawing and parts list in the Service Manual
supplied with your pump. If you need replacement or additional copies, contact your
local Marathon Distributor, or the Marathon factory Literature Department at the number
shown below. To receive the correct manual, you must specify the MODEL and TYPE
information found on the name plate of the pump.
MODELS WITH 1" SUCTION/DISCHARGE OR LARGER,
AND METAL CENTER SECTIONS:
The main air valve sleeve and spool set is located in the valve body mounted on the
pump with four hex head capscrews. The valve body assembly is removed from the
pump by removing these four hex head capscrews.
With the valve body assembly off the pump, access to the sleeve and spool set is
made by removing four hex head capscrews (each end) on the end caps of the valve
body assembly. With the end caps removed, slide the spool back and forth in the sleeve.
The spool is closely sized to the sleeve and must move freely to allow for proper pump
operation. An accumulation of oil, dirt or other contaminants from the pump’s air supply,
CAUTION
If the pump has been subjected to
freezing temperatures, do not operate
until the unit is completely thawed.
Fig. 1 Safety clip.
Fig. 2 Tighten the boss plug.
DANGER
Before doing any maintenance on
the pump, be certain all pressure is
completely vented from the pump,
suction, discharge, piping, and all
other openings and connections.
Be certain the air supply is locked
out or made non-operational, so that
it cannot be started while work
is being done on the pump. Be
certain that approved eye protection
and protective clothing are worn
at all times in the vicinity of the
pump. Failure to follow these
recommendations may result in
serious injury or death.