Air exhaust, Between uses, Flap valve servicing – SANDPIPER HDF2 User Manual
Page 10: Diaphragm servicing, Reassembly
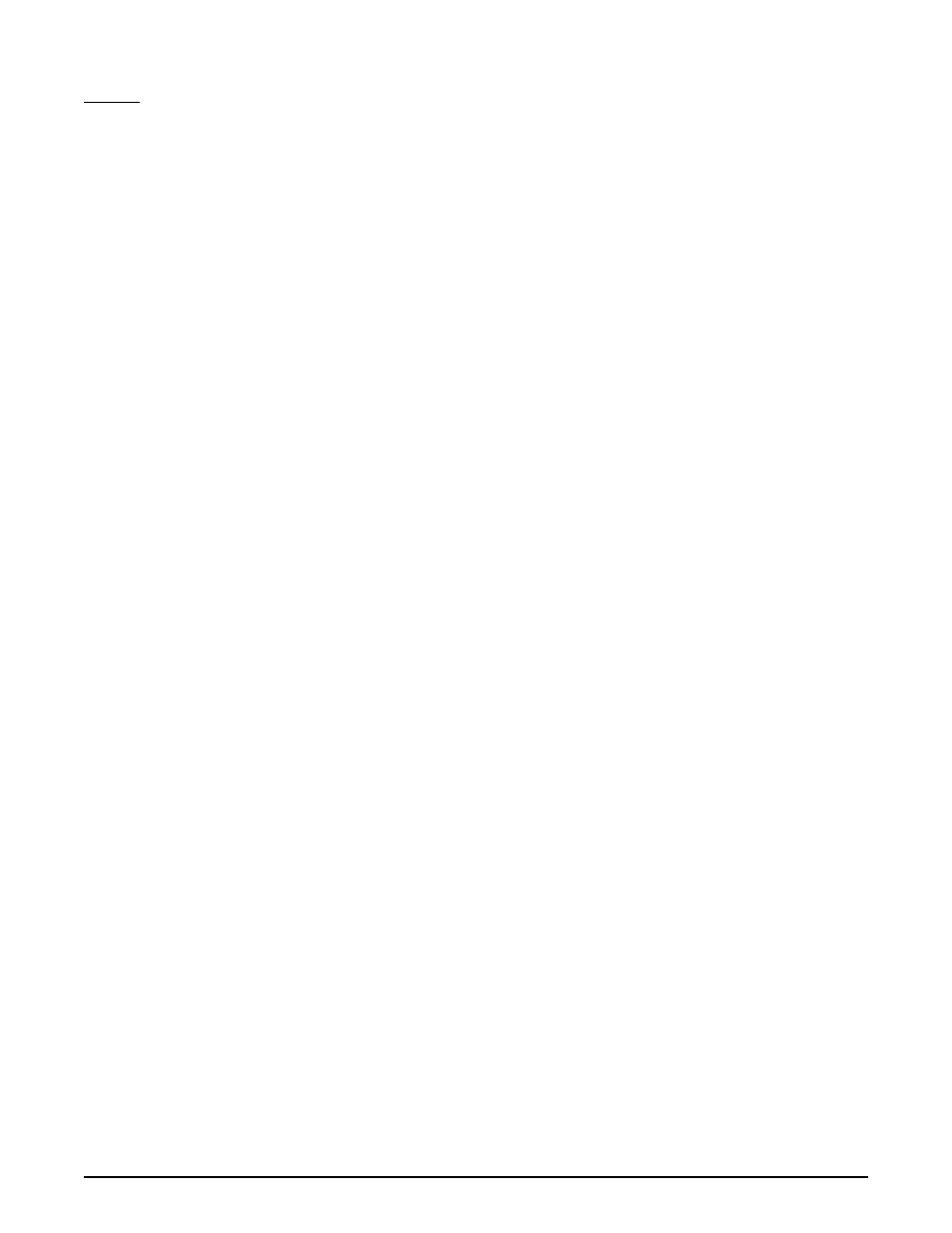
hdf2dl6sm-rev0614
Model HDF2 Page 8
rings on the sleeve with an o-ring assembly lubricant or lightweight oil (such as 10 wt. air line lubricant).
Re-install one end cap, gasket and bumper on the valve body. Using the arbor press or bench vise that was used in disassembly,
carefully press the sleeve back into the valve body, without shearing the o-rings. You may have to clean the surfaces of the valve
body where the end caps mount. Material may remain from the old gasket. Old material not cleaned from this area may cause
air leakage after reassembly. Take care that the bumper stays in place allowing the sleeve to press in all the way. Reinstall the
spool, opposite end cap, gasket and bumper on the valve body. After inspecting and cleaning the gasket surfaces on the valve
body and intermediate, reinstall the valve body on the pump using new gaskets. Tighten the four hex head capscrews evenly
and in an alternating cross pattern.
AIR EXHAUST
If a diaphragm fails, the pumped liquid or fumes can enter the air end of the pump, and be exhausted into the atmosphere.
When pumping hazardous or toxic materials, pipe the exhaust to an appropriate area for safe disposition.
This pump can be submerged if materials of construction are compatible with the liquid. The air exhaust must be piped above
the liquid level. Piping used for the air exhaust must not be smaller than 1" (2.54 cm). Reducing the pipe size will restrict air flow
and reduce pump performance .When the product source is at a higher level than the pump (flooded suction), pipe the exhaust
higher than the product source to prevent siphoning spills.
Freezing or icing-up of the air exhaust can occur under certain temperature and humidity conditions. Use of an air dryer unit
should eliminate most icing problems.
BETWEEN USES
When used for materials that tend to settle out or transform to solid form, the pump should be completely flushed after each
use, to prevent damage. Product remaining in the pump between uses could dry out or settle out. This could cause problems
with valves and diaphragms at re-start. In freezing temperatures, the pump must be drained between uses in all cases.
FLAP VALVE SERVICING
Valve inspection requires removal of 3/8" hex nuts and elbows. When the top suction elbows are removed, the valve and
seat are connected as an assembly. When the bottom discharge elbows are removed, the valve and seat stay with the outer
chamber. Visual inspection and cleaning is possible. If parts are to be replaced, remove the self-locking nuts and all parts
are accessible.
DIAPHRAGM SERVICING
Diaphragms can be inspected or the diaphragm assembly removed without removing the suction and discharge flanges.
Remove (8) nuts around the chamber flange, and the housing assembly will pull off. Flap valves can be inspected for proper
seating at this point as well as the diaphragm. Use care to keep foreign matter from behind the diaphragm. The opposite dia-
phragm may be inspected by the same procedure. If either diaphragm has to be replaced, follow closely these steps:
Pull the outer diameter of one diaphragm off the (8) capscrews. NOTE: One side only! On the free diaphragm assembly, use a
3/8" allen wrench to turn the assembly (diaphragm, plates and screw) loose from the shaft. Once the assembly has turned, it
will turn out by hand by use of the diaphragm. Now the opposite diaphragm assembly and the drive shaft will pull free from the
capscrews and pump
intermediate assembly. The interior components consisting of sleeve bearings, rod seals, and pilot valve actuator bushings
are now accessible for service if required. Hold the shaft in a clamping device making sure to protect surface of shaft so as
not to scratch or mar it in any way. The diaphragm assembly will turn loose. To disassemble the components, turn a 1/4"-20
capscrew by hand into the tapped hole in the inner plate. This keeps the plate from turning while the socket head capscrew
is removed. To do this, place assembly in a vise so the two protruding ends of screws are loose in the vise jaws (about 3/4"
apart). Turn the center screw loose from the back plate and the assembly will come apart.
REASSEMBLY
All procedures for reassembling the pump are the reverse of the previous instructions with further instructions as shown:
1. The diaphragm assemblies are to be installed with the natural bulge outward or toward the head of the center screw. Make
sure both plates are installed with outer radii against the diaphragm. After all components are in position in a vise and hand
tight, set a torque wrench for 480 inch pounds (40 ft. pounds) (54.23 Newton meters) or, 600 inch pounds (50 ft. pounds)
(67.79 Newton meters) for Santoprene, using a (3/8") allen head socket. After each diaphragm sub assembly has been
completed, thread one assembly into the shaft (held near the middle in a vise having soft jaws to protect the finish) making
sure the stainless steel washer is in place on the capscrew.
Make sure 1/4"-20 mounting screw has been removed and that the bumper (Item #19 on drawing) is in place in the shaft.
Install this sub assembly into the pump and secure by placing the outer chamber housing and capscrews on the end with
the diaphragm. This will hold the assembly in place while the opposite side is installed. Make sure the last diaphragm assem-
bly is torqued to 30 ft. lbs. (40.67 Newton meters) before placing the outer diaphragm over the capscrews. If the holes in the
diaphragm flange do not line up with the holes in the chamber flange, turn the diaphragm assembly in the direction of tighten-
ing to align the holes so that the capscrews can be inserted. This final torquing of the last diaphragm assembly will lock the two
diaphragm assemblies together. Place remaining outer chamber on the open end and tighten down the securing nuts
gradually and evenly on both sides.
Caution should be used while reassembling Flap valves. The valves are designed for some preload over the retainer hinge
pad. This is done to insure proper face contact with the seat. After all parts are in place, tighten the lock nuts down on the as-