Component range, Vision capability, Feeder capacity placement speed and accuracy – MYDATA MY200LX User Manual
Page 2: Board handling, System features, High precision mounthead – midas, High speed mounthead – hydra z8l (optional), Electrical verifier (optional), Linescan vision system (optional), Feeder capacity 8 mm tape
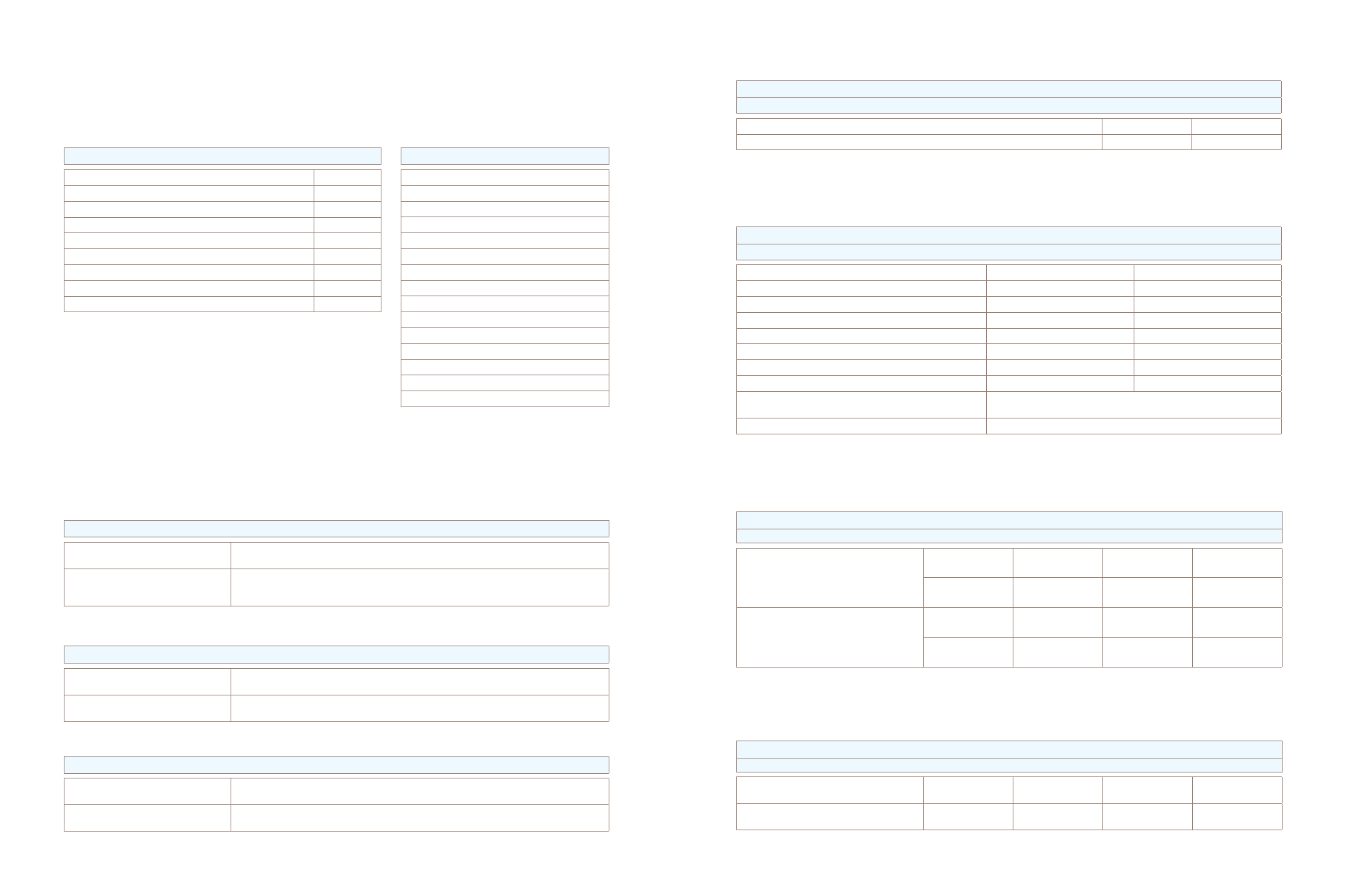
MY200-SerieS P&P SPecificatioN – MY200LX
coMPoNeNt raNge
high PreciSioN MouNthead – MidaS
component range
chip (from 01005)
(1)
, Soic, PLcc, tSoP, QfP, Bga, flip chip, odd-shape, surface-mount
connectors, through-hole components, cSP, ccga, dPaK, alcap, tantalum.
component Specification
Min: 0.4 x 0.2 mm (0.016” x 0.008”) (01005)
Max: 56 x 56 x 15 mm (2.20” x 2.20” x 0.59”)
Max: component weight: 140 g
(2)
1) requires dual vision system (dVS) or line scan vision system (LVS). Standard vision system (SVS) chip from 0402.
2) depending on mounthead, mount tool, package, and production altitude.
high SPeed MouNthead – hYdra z8L (oPtioNaL)
component range
chip (from 0201)
, So8, So14, Sot23, MeLf.
component Specification
Min: 0.6 x 0.3 mm (0.02 x 0.01”) (0201)
Max: 8.70 x 8.70 x 5.60 mm (0.34” x 0.34” x 0.22”)
eLectricaL Verifier (oPtioNaL)
component range
resistor, capacitor, unipolar capacitor, diode (forward voltage, reverse current),
zener diode (voltage drop), transistor (current gain)
Verification time
on-the-fly
LiNeScaN ViSioN SYSteM (oPtioNaL)
component
type
camera
max
active
field
of
view
min
pitch
min
lead
width
Leaded components
LVc
(1)
56 x 56 mm
(2.2” x 2.2”)
0.20 mm (8 mil)
0.10 mm (4 mil)
Bumped components
LVc
(1)
56 x 56 mm
(2.2” x 2.2”)
0.30 mm (12 mil)
0.15 mm (6 mil)
ViSioN caPaBiLitY
StaNdard ViSioN SYSteM, duaL ViSioN SYSteM (oPtioNaL)
component
type
camera
max
active
field
of
view
min
pitch
min
lead
width
Leaded components
SVc
(1)
56 x 52 mm
(2.20” x 2.04”)
0.40 mm (16 mil)
0.20 mm (8 mil)
hrc
(2)
15 x 15 mm
(0.59” x 0.59”)
0.10 mm (4 mil)
0.05 mm (2 mil)
Bumped components
SVc
(1)
56 x 52 mm
(2.20” x 2.04”)
0.50 mm (20 mil)
0.25 mm (10 mil)
hrc
(2)
15 x 15 mm
(0.59” x 0.59”)
0.16 mm (6.3 mil)
0.08 mm (3.1 mil)
1) Standard vision camera in standard/dual vision system (SVS/dVS).
2) high resolution camera in dual vision system (dVS).
1) Line scan vision camera.
feeder caPacitY
PLaceMeNt SPeed aNd accuracY
PLaceMeNt SPeed aNd accuracY – MY200LX 10/14
rated Speed
(1)
16 000 cPh
iPc 9850 chip Net throughput
(2,3)
13 800 cPh
iPc 9850 chip tact time
(3)
0.250 s
iPc 9850 chip repeatability 3s (X, Y, theta)
(3,6)
45 µm, 1.8°
iPc 9850 chip accuracy @ cpk = 1.33 (X, Y, theta)
(5,7)
75 µm, 2.6°
iPc 9850 fine Pitch Net throughput
(2,4,8)
3 200 cPh
iPc 9850 fine Pitch tact time
(4)
0.958 s
iPc 9850 fine Pitch repeatability 3s (X, Y, theta)
(4)
21 µm, 0.05º
iPc 9850 fine Pitch accuracy @ cpk = 1.33 (X, Y, theta)
(4,5)
35 µm, 0.09º
the above specification achieved with a machine configuration including high precision mounthead (Midas),
high speed mounthead (hYdra z8L), line scan vision system (LVS) and inline conveyor t3.
the iPc 9850 net throughput and accuracy numbers are obtained simultaneously, with the same machine settings.
the rated speed value is obtained under conditions optimized for speed.
1) depending on component and application.
2) according to iPc 9850. Net throughput = (no of parts x 3600) / (board build time + board transfer time).
3) according to iPc 9850 0402c verification panel.
4) according to iPc 9850 QfP64/QfP100 verification panel.
5) according to iPc 9850 cpk 1.33 = 4s + offset.
6) chip repeatability with high precision head 36 µm, 1.5°
7) chip accuracy with high precision head, 63 µm, 2.2°
8) fine pitch net throughput 2 250 cPh and tact time 1.423s with SVS/dVS.
feeder caPacitY 8 MM taPe
t3 t4
MY200LX-10
112
96
MY200LX-14
176
160
Board haNdLiNg
iNLiNe coNVeYor
t3 t4
Maximum Board Size
443 x 508 mm (17.4” x 20”)
575 x 508 mm (22.6” x 20”)
Maximum Board Size with ML adaptor
(1)
419 x 443 mm (16.5” x 17.4”)
554 x 443 mm (21.8” x 17.4”)
Minimum Board Size
(2)
70 x 50 mm (2.7” x 2”)
70 x 50 mm (2.7” x 2”)
Board thickness range
0.4 - 6.0 mm (0.016” - 0.24”)
0.4 - 6.0 mm (0.016” - 0.24”)
Board edge clearance top and Bottom
3.2 mm (0.13”)
3.2 mm (0.13”)
top Side clearance (max)
15 mm (0.59”)
15 mm (0.59")
Bottom Side clearance (max)
32 mm (1.25”)
32 mm (1.25")
Maximum Board Weight
5 kg (11 lbs)
8 kg (17 lbs)
Board transfer height
conforms to SMeMa standard for board transfer height.
height adjustable from 880 to 975 mm (34.6” to 38.4”).
operation Mode
inline, manual, inline odd-board, left-to-right / right-to-left
1) optional. Suitable for irregular sized and odd shaped boards.
2) recommended board train specification: 90 x 50 mm (3.5” x 2”) board size, 1.6 mm (0.06”) thickness.
SYSteM featureS
SYSteM featureS MY200LX
on-the-fly mount order optimization
Vision autoteach with snap-to-grid
automatic illumination settings
intelligent feeder concept – agilis
automatic feeder and component recognition
on-the-fly feeder loading
dynamic feeder positions
automatic board stretch compensation
automatic conveyor width adjustment
intelligent surface impact control
tool collision avoidance
Multi-user, multi-tasking system software
open software interfaces for factory integration
SQL database engine
Programmable light settings fiducial camera