Pumptec 207V SERIES User Manual
Page 3
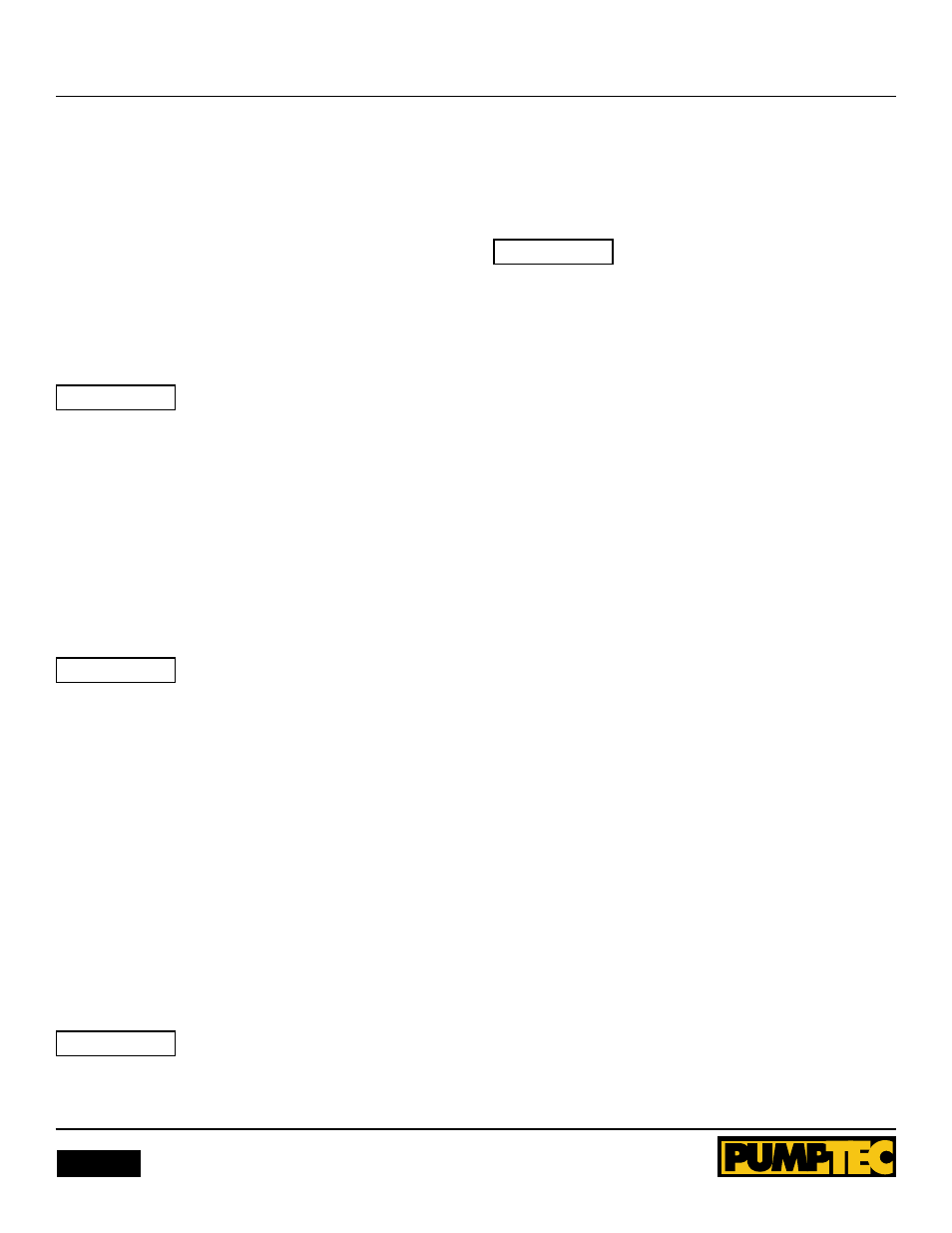
3
Version 110112
Pumptec Operating Instructions and Parts Manual
PUMP SERIES 205V | 207V
Pumptec, Inc. is not responsible for losses, injury, or death
resulting from a failure to observe these safety precautions,
misuse or abuse of pumps or equipment.
iNStALLAtiON
MOUnTIng
Pump motor set can be mounted in any position EXCEPT
with pump head higher than motor. To minimize amp draw,
noise and vibration, use appropriate flexible hose to inlet and
discharge ports.
lOCATIOn
cAutIoN!
If the pump is used in extremely dirty or
humid conditions, it is recommended pump be enclosed. Do
not store or operate in excessively high temperature areas or
without proper ventilation.
The pumping system can be mounted where it is visible, but
it must be protected from rain, dirt and chemical spray or
splashing. The pump must never be installed on a vertical
surface with the pump head higher than motor, like a capital
letter “T”, for example.
PRE-OPERAtiON
InlET COnDITIOnS
cAutIoN!
DO NOT STARVE THE PUMP
OR RUN DRY. Temperatures above 130°F will require
pressurized inlet to avoid cavitation and seal damage.
DISCHARgE COnDITIOnS
Open all valves in system prior to operation to avoid excessive
load on motor and system from a pressure spike. Follow the
instructions of proper system design. Refer to supplier if
assistance is needed.
PRESSURE REgUlATIOn
Verify pressure regulation devices are operating correctly.
nOZZlES
nozzles create pressure in most systems and they become
larger with use. larger nozzles decrease system pressure. Verify
the quality of nozzles prior to operation.
MOTOR SHAFT ROTATIOn
cAutIoN!
Motor shaft rotation must always be
counterclockwise in order to assure proper function of pump
or warranty may be void.
PUMPED lIQUIDS
Some liquids may require a flush between operations or before
storing. For pumping liquids other than water, contact your
supplier.
cAutIoN!
If the pump is used in extremely dirty or
humid conditions, it is recommended pump be enclosed. Do
not store or operate in excessively high temperature areas or
without proper ventilation.
oPerAtIoN
gEnERAl OPERATIng InFORMATIOn
Pressure is often created by forcing a volume of fluid (flow)
through a specific size hole (nozzle). Additionally, pressure can
be created by pumping into a non-expanding chamber. Pressure
is measured and stated in PSI – pounds per square inch.
Flow is created based upon the pump displacement and speed
(RPM) of the motor. Pump plunger size affects flow based upon
the same RPM. The faster the motor speed, the greater the
flow. Flow is measured and stated in gPM – gallons per minute.
The pump, driven by a motor or engine, draws fluid through a
set of valves into the pumping chamber and the fluid is then
forced out of a set of valves to exit the pump. The back and
forth movement of the plunger in the sealed pumping chamber
creates the suction and discharge actions.
Once the fluid has exited the pump it must be controlled
until it exits the nozzle or reaches the place it needs to go.
This control is achieved via the use of system components
such as an unloader or regulating valve. The pumps are
positive displacement pumps providing a specific amount of
fluid constantly while operating. This volume of fluid must
be directed out thru a nozzle or back to a tank because it
cannot be stopped completely without creating excessively
high pressure and risk of damage to pump, components,
property and person. It is recommended a safety device such
as a regulating valve be installed directly on pump head as
protection in case of a failure of another component. Pressure
switches can be used to automate pump operation, but they
must have a pressure regulating device installed as a safety
device.
Fluid can enter a pump either from a filtered tank or
pressurized fluid line.
It is common to use a tank with pumps that are mounted above
the pump. Filtration is important to maintain proper function
of the pump and system. The extent of filtration may be greater
based upon some uses such as misting with ultra-fine nozzles.