Nova-Tech LMI Series G - SD Metering Pump User Manual
Page 19
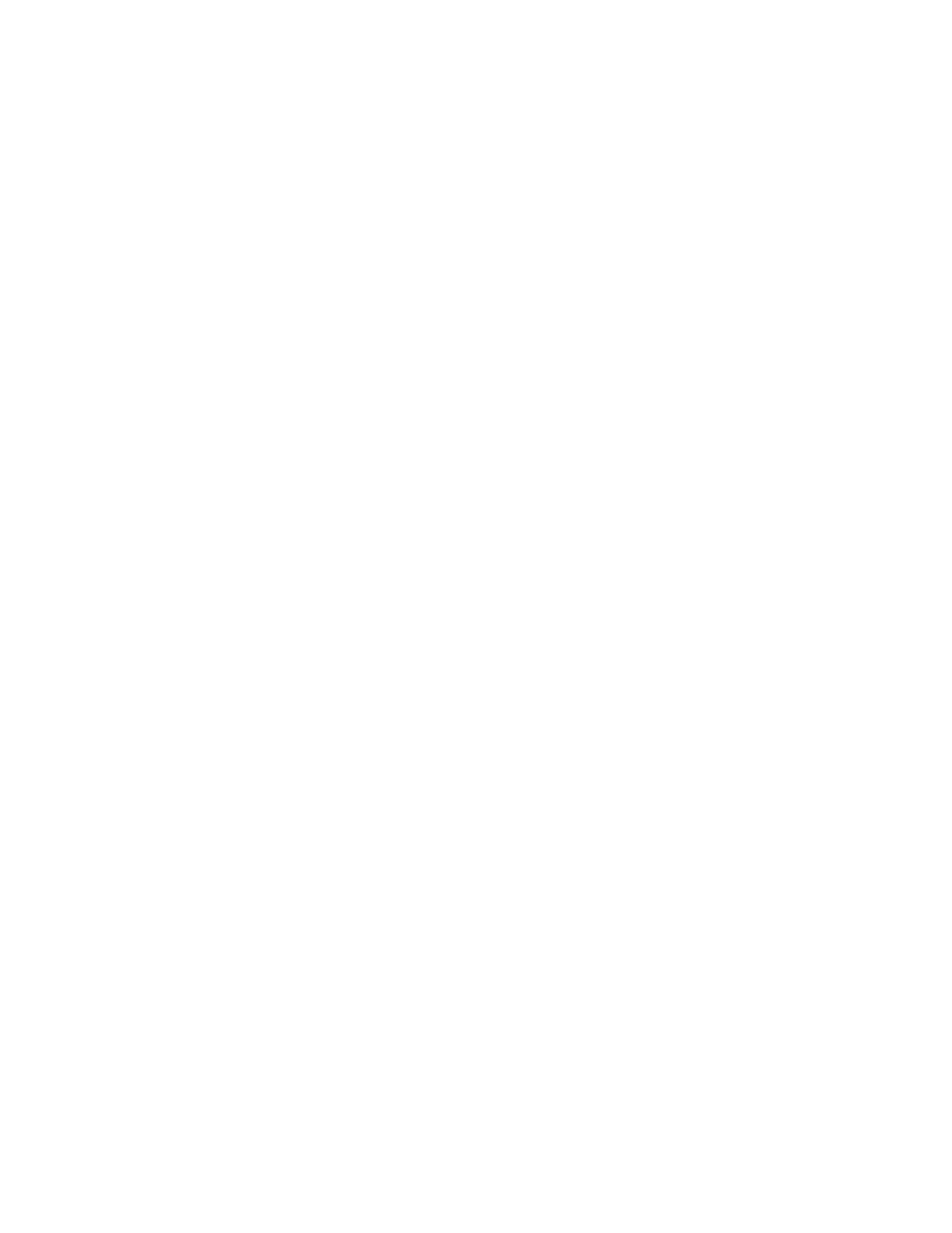
SECTION 4
MAINTENANCE
17
4.1 PREVENTATIVE MAINTENANCE
Drive
Initially, change the oil in the pump drive assembly after
the first 1000 hours of operation. Thereafter, change
drive oil on an annual basis or after every 5000 hours of
operation.
The drive should be refilled with 1 quart of Mobil SHC
629:
Viscosity @ 100
o
F = 726 SSU
Viscosity Index
= 149
ISO Grade
= 150
Diaphragm Assembly
The Series G Model D diaphragm should be replaced
annually or every 5000 hours of operation to avoid the
possibility of failure. Refer to the instructions in Sec-
tion 4.6 Diaphragm and Oil Seal Bellows Replacement.
Oil Seal Bellows
The Series G Model D oil seal bellows should also be
replaced annually. Oil seal bellows replacement requires
the removal of the diaphragm assembly, so it is recom-
mended that the oil seal and diaphragm assembly be
replaced at the same time. Refer to the instructions in
Section 4.6 Diaphragm and Oil Seal Bellows Replace-
ment.
Check Valves
As in the case of the diaphragm, LMI/Milton Roy Com-
pany recommends that check valve balls, seats, gas-
kets, and O-rings be replaced on an annual basis or
every 5000 hours of operation. If highly corrosive mate-
rial (acids, slurries, etc.) is being pumped, more fre-
quent replacement may be required. Complete instruc-
tions for replacement of worn check valves are given in
Section 4.5 Corrective Maintenance.
4.2 RETURNING PUMPS TO THE FACTORY FOR
REPAIR
Pumps can not be accepted for repair without a Return
Material Authorization. Pumps should be clearly labeled
to indicate the liquid being pumped. Process liquid
should be flushed from the pump liquid end and oil should
be drained from the pump housing before the pump is
shipped.
Note: United States of America Federal law
prohibits handling of equipment that is not ac-
companied by an OSHA Material Safety Data
Sheet (MSDS). A completed MSDS must be
packed in the shipping crate with any pump
shipped for repair. These safety precautions
will aid the troubleshooting and repair proce-
dure and preclude serious injury to repair per-
sonnel from hazardous residue in pump liquid
end. A Materials Safety Data Sheet must ac-
company all returns.
All inquiries or parts orders should be addressed to your
local representative or distributor.
4.3 ROUTINE MAINTENANCE
LMI/Milton Roy Series G pumps are carefully designed,
manufactured, assembled, and quality tested to give
reliable service with minimal maintenance. However, a
weekly maintenance check is recommended to confirm
proper operation of the pump.
Visual Check of Seal Integrity of Mechanical
Assembly, Figure 6.
Check for leaks in the following components. If leaks
exist, contact the factory for assistance.
1. Motor flange: If leaking, replace motor flange sealing
gasket (Item 11 in Figure 6).
2. Stroke adjustment knob: If leaking, replace stroke
adjustment seal (Item 160 in Figure 6).
Checking the Pump Capacity
Assuming the pump has been calibrated as described
in Section 3, the capacity can be checked by shutting
the valve from the supply vessel and opening the valve
from the calibration column to the suction side of the
liquid end. Measure the volume of pumped liquid for a
given period of time at the various settings.
If a calibration column is not installed in the suction
piping, place the foot valve (or suction line) in a calibrat-
ing chamber (graduated reservoir). Measure the volume
of pumped liquid for a given period of time at the various
settings.
Occurrence of Leak From Detection Ports
Determine whether the product collected at the detec-
tion port in the liquid end mounting assembly is lubri-
cating oil or the pumped fluid.
If the product is pumped fluid, the diaphragm has failed.
If the product is lubricating oil, the oil seal bellows has
failed. Proceed with its replacement (see Section 4.6
Diaphragm and Oil Seal Bellows Replacement).
13