Operation, Service and maintenance, Inspection – Mody Pumps MSP Series User Manual
Page 5: Changing the oil
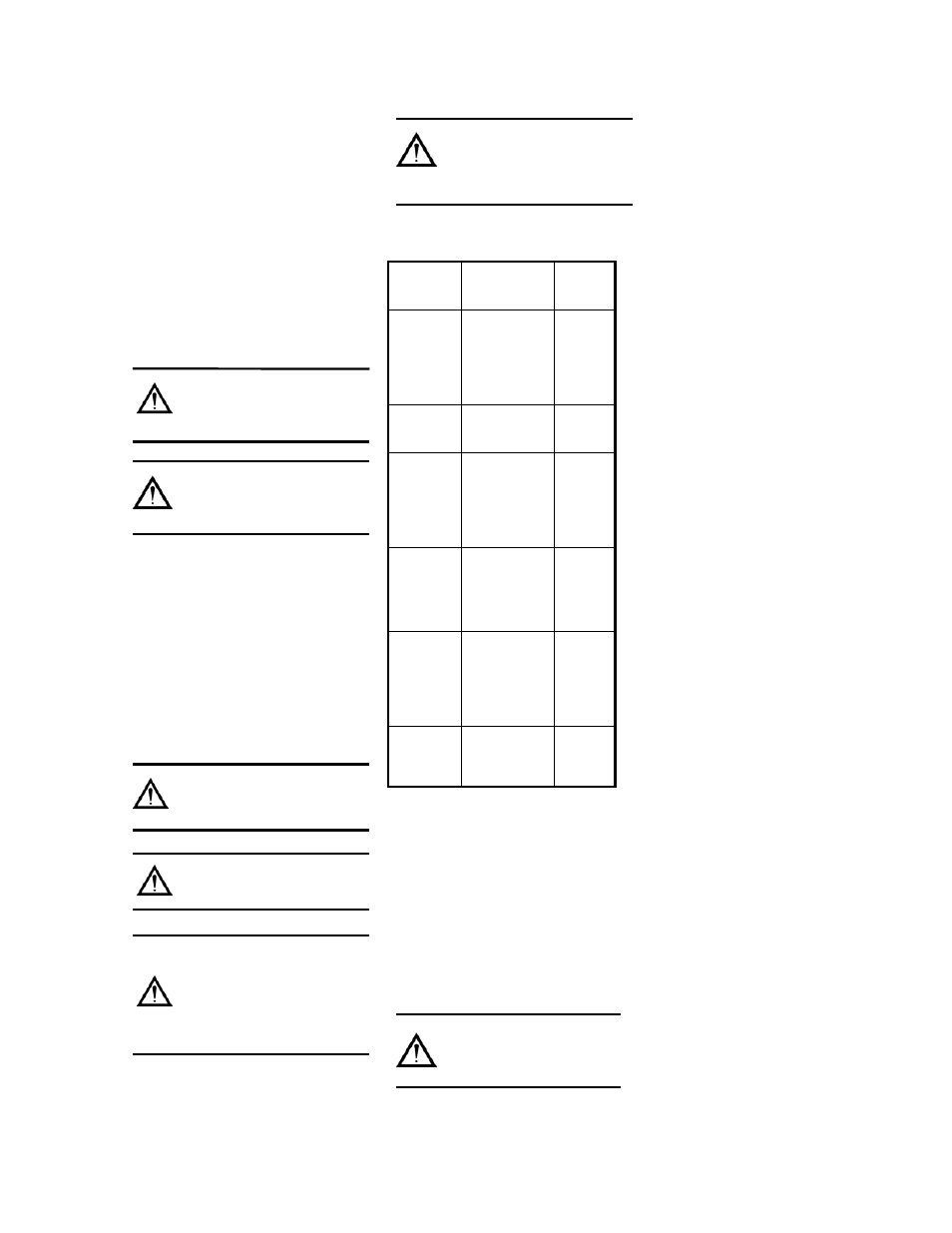
3
Operation
Before initial start-up after repair or in a new
installation, always check direction of
rotation. The pump must always rotate in an
anti-clockwise direction. If the rotation is
clock-wise, transpose two phases in the
electric control panel so that it will change to
proper rotational direction.
Be aware of the starting torque, it may be
very strong depending on the size of the
pump. Do not hold the pump when checking
the rotation. The pump must be heavily
supported and never started when hanging in
a chain without proper support when
performing a rotational check or in operation.
WARNING! As the pump will pump up to 70%
of the nominal flow at wrong rotation, never
use the visual flow rate to determine the
direction of rotation. Most times, the pump
creates heavy noise and vibration when
operates at wrong rotation.
WARNING! Do not insert your hand or any
other object into the pump volute and impeller
if any power supply is connected. Remove
physically the cable even if security devices is
activated
Service and
maintenance
Regular inspection and preventive
maintenance will ensure more reliable
operation. The pump should be inspected
every six months or more often if the
operating conditions are difficult. The cable
should be checked more frequently. For a
complete overhaul of the pump, please
contact an authorized MODY service facility
workshop or your MODY dealer.
CAUTION! When the pump or motor section
has been laid on its side, always secure it with
wedges from both sides to prevent it from rolling
away.
CAUTION! Parts must be replaced by genuine
spares, including screws, to ensure correct
strength.
CAUTION! Before maintenance and repair
work, motor leads must first be completely
disconnected from the power supply.
Never work on electrical systems during a
thunder storm.
All work on the electrical system may only be
performed by qualified electricians.
CAUTION! Before undertaking any service
work, make sure that the pump is
thoroughly clean, and bear in mind the
importance of observing good personal
hygiene. Follow your local safety
instructions.
Inspection
Pump
Section
Inspection Action
in
the event
of a
fault.
Cables
Check that the
sheath is not
damaged.
Check that the
cables are not
kinked or
nipped.
Fit a new
cable.
Correct
the fault.
Cooling
water
Check the
cooling water
level of coolant
Fill up
with
cooling
liquid.
Visible Parts
Check that all
parts are in
good condition,
and that bolts
and nuts are
securely
tightened.
Replace
worn
parts.
Tighten
any loose
bolts and
nuts.
Impeller /
Wear ring
Check that the
parts are not
worn to such an
extent that the
pump
performance is
affected.
Adjust
the wear
ring.
Shaft seal
Check that the
oil is clean and
is not mixed with
water.
See under
“Changing the
oil”.
In the
event of
slight
leakage,
change
the oil.
Hoses,
pipes and
valves
Check that the
equipment does
not leak or is
otherwise
damaged.
Adjust or
replace
defective
parts.
Changing the oil
Change of oil is done in the same way on
cooled and un-cooled pumps. Remove the
plug marked “outlet” and let the old oil pour
out through the groove under the plug.
Discard of any used oil in accordance with
local regulations. Fasten the plug so that
the lower but not the top O-ring gasket
seals. Loosen the plug marked “inlet” and
fill up with oil and then fasten both oil
plugs. Use food grade oil of same quality
and performance as Enerpar M002, white
oil.
CAUTION! In the event of inward leakage,
the oil housing may be pressurized.
When removing the oil plug, hold a piece of
cloth over it to prevent oil from splashing.
NOTE! Old oil should be entrusted to an oil
disposal company in accordance with local
regulations.