Cashco 8900 User Manual
Page 11
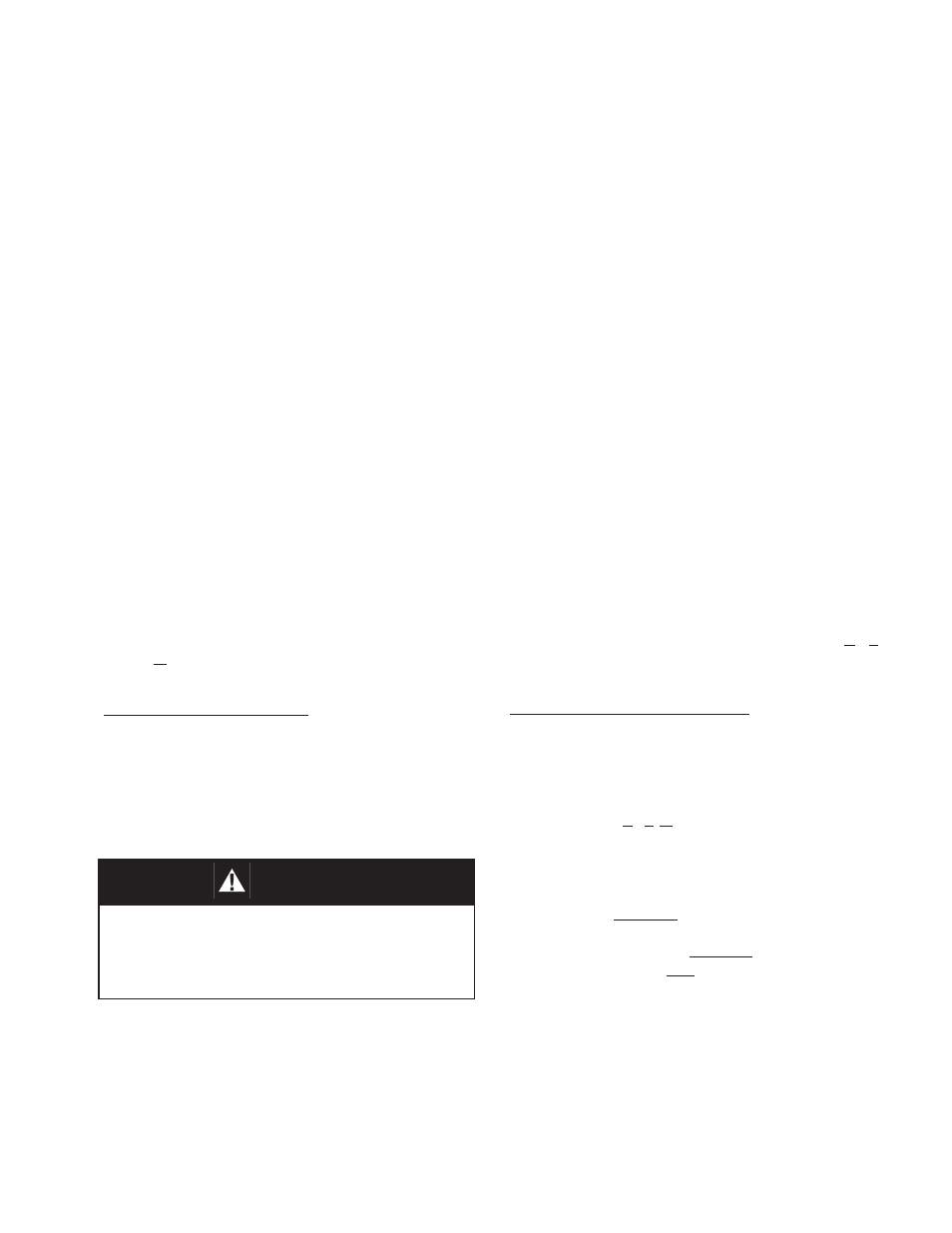
11
IOM-8900 Series
NEW REPLACEMENT UNIT:
Contact your local Cashco, Inc., Sales Rep re sen ta-
tive with the Serial Number, Product code and the
pressure / vacuum settings. With this information
they can provide a quotation for a new unit including
a complete description, price and availability.
SECTION VI
VI. ORDERING INFORMATION:
NEW REPLACEMENT UNIT vs PARTS "KIT" FOR FIELD REPAIR
To obtain a quotation or place an order, please retrieve the Serial Number and Product Code that was
stamped on the metal name plate and attached to the unit. This information can also be found on the Bill of
Material (parts list) that was provided when unit was originally shipped.) (Serial Number typically 6 digits).
PARTS "KIT" for FIELD REPAIR:
Contact your local Cashco, Inc., Sales Rep re-
sen ta tive with the Serial Number , Product code
and Pressure / Vacuum settings. Identify the
parts and the quantity required to repair the unit
from the Bill of Materials sheet that was provided
when unit was originally shipped.
NOTE: Those part numbers that have a quantity
indicated under "Spare Parts" in column "A”
refl ect minimum parts required for inspection
and rebuild, - "Soft Goods Kit". Those in col-
umn “B” include minimum trim replacement
parts needed plus those "Soft Goods" parts
from column "A".
If the "BOM" is not available, refer to the cross-
sectional drawings included in this manual for
part identifi cation and selection.
Local Sales Representative will provide quo-
tation for appropriate Kit Number, Price and
Availability.
CAUTION
Do not attempt to alter the original construction of any
unit without assistance and approval from the factory.
All purposed changes will require a new name plate with
appropriate ratings and new product code to accomo-
date the recommended part(s) changes.
20. Place upper spring canister (15) over
vacuum spring (16), align bolt holes in canister
fl anges.
21. Insert cap screws (28) into fl ange bolt
holes and tighten snug - torque to 10 ft-lbs. NOTE:
DO NOT over- tighten cap screws.
Proceed to F or G.
F.
Assemble Pallet Assembly & Counter
Weight to Flange Seat Assembly:
1. Place pallet assembly on fl ange seat (1).
Align pivot arm (46) with hinge (60) and insert hinge
pin (52). Install nut (55).
2. Use overhead support and sling to lift
counter weight (58). Align hole in weight arm (47)
with pin hole in arm assembly (46). Press pin (50)
through arm assembly (46), spacers (51) and weight
arm (47). Slip cables (17) over pin (50) ends and
install cotter pins (57).
G. Assemble Pallet Assembly & Stack
Weights to Flange Seat Assembly:
1. Place pallet assembly on fl ange seat (1).
Align pivot arm (46) with hinge (60) and insert hinge
pin (52). Install nut (55).
2. Position stack weights (64) over studs on
top of jam nuts in vent hood (11). Maintain stack
orientation, do not remove or add any weight that
will change the factory calibrated pressure setpoint.
3. Install fl at washers ( 67), lock washers (68)
and hex nuts (36). Torque to 15 ft.-lbs.