Gorman-Rupp Pumps SFV4A 1476537 and up User Manual
Page 41
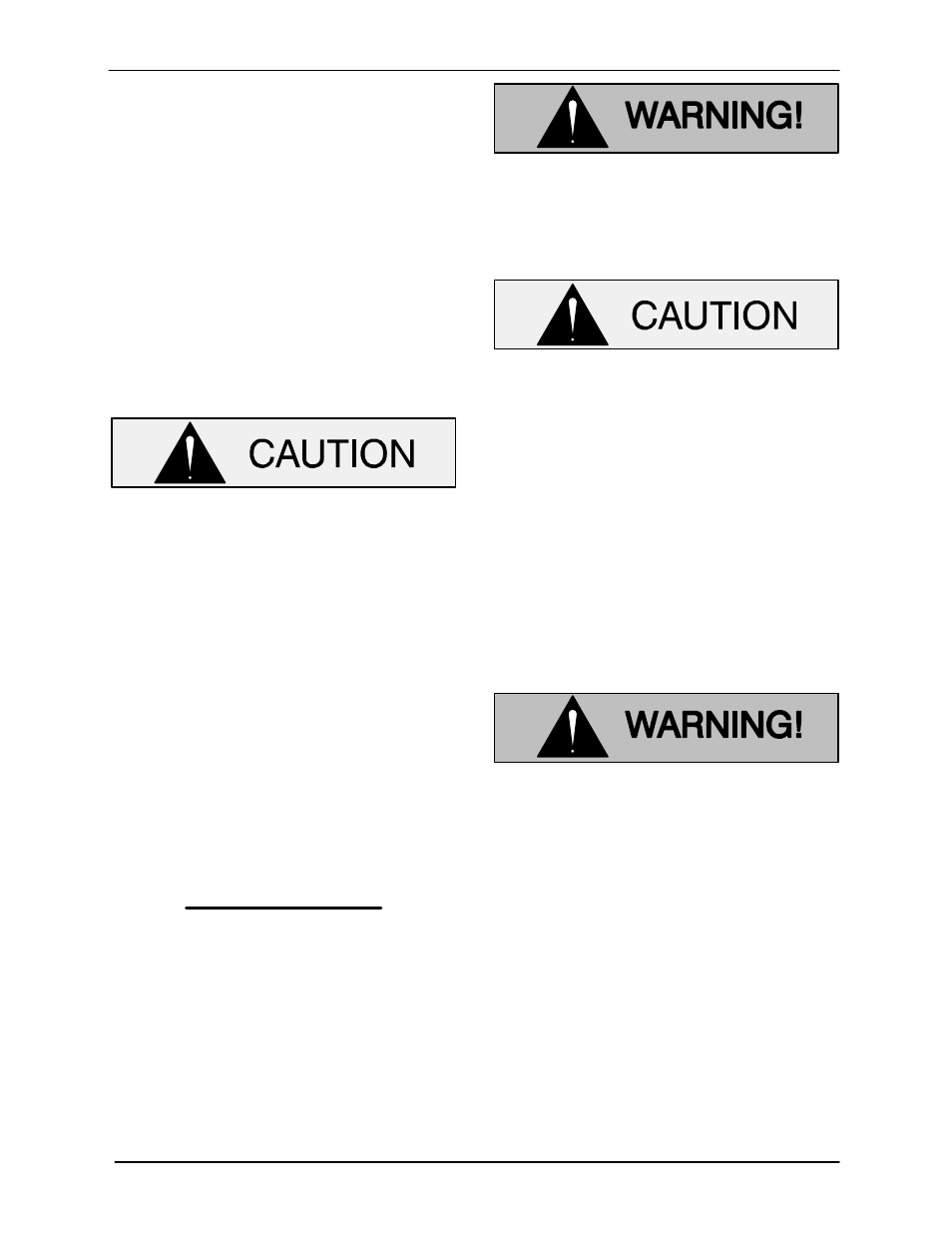
OM-06401
SF SERIES
PAGE E - 15
MAINTENANCE AND REPAIR
the intermediate until fully seated. If removed,
install a new male terminal (15) on the sensor and
position it so the moisture sensor female terminal
(14) can be easily attached.
Inspect the rotor shaft (3) for damaged threads,
scoring in the seal area, and a nicked or damaged
keyway. If the bearings were removed, inspect the
bearing areas for scoring or galling. Remove nicks
and burrs with a fine file or emery cloth. Inspect the
rotor area for separated laminations. If the shaft is
bent or damaged, or if the laminations are sepa
rated, replace the shaft and rotor (a single assem
bly).
To prevent damage during removal from
the shaft, it is recommended that bearings
be cleaned and inspected in place. It is
strongly recommended that the bearings
be replaced any time the shaft and rotor
assembly is removed.
The bearings may be heated to ease installation.
An induction heater, hot oil bath, electric oven, or
hot plate may be used to heat the bearings. Bear
ings should never be heated with a direct flame or
directly on a hot plate.
NOTE
If a hot oil bath is used to heat the bearings, both the
oil and the container must be absolutely clean. If
the oil has been previously used, it must be thor
oughly filtered.
Slide the snap ring (4) over the shaft with the bev
eled edge of the snap ring facing the rotor.
Heat the bearings (2 and 5) to a uniform tempera
ture no higher than 250
_F (120_C). Slide the bear
ings onto the shaft, one at a time, until they are fully
seated against the shaft shoulders. This should be
done quickly, in one continuous motion, to prevent
the bearings from cooling and sticking on the shaft.
Use caution when handling hot bear
ings to prevent burns.
If heating the bearings is not practical, use a suit
ably sized sleeve and an arbor (or hydraulic) press
to install the bearings on the shaft.
When installing the bearings onto the
shaft, never press or hit against the outer
race, balls, or ball cage. Press only on the
inner race.
After the bearings have been installed and allowed
to cool, check to ensure that they have not moved
out of position in shrinking. If movement has oc
curred, use a suitably sized sleeve and a press to
reposition the bearings. Make certain that they are
seated squarely against the shaft shoulders.
Use fresh solvent to clean all O‐ring surfaces of the
motor housing and intermediate (8). Inspect the
sealing surfaces for burrs, nicks and pits which
could cause a poor seal. Repair or replace as re
quire.
Most cleaning solvents are toxic and
flammable. Use them only in a well ven
tilated area free from excessive heat,
sparks, and flame. Read and follow all
precautions printed on solvent contain
ers.
Position the intermediate with the impeller end
down on some wood blocks tall enough to allow for
installation of the rotor shaft through the intermedi
ate.
Slide the assembled shaft and bearings into the in
termediate until the lower bearing seats squarely in
the intermediate bore. Secure the rotor and shaft to
the intermediate by installing the snap ring (4) in
the groove in the intermediate bore.
Install a new O‐ring (6) on the shoulder of the inter
mediate.