Gorman-Rupp Pumps SE2D3A 115V 1P 1483930 and up User Manual
Page 19
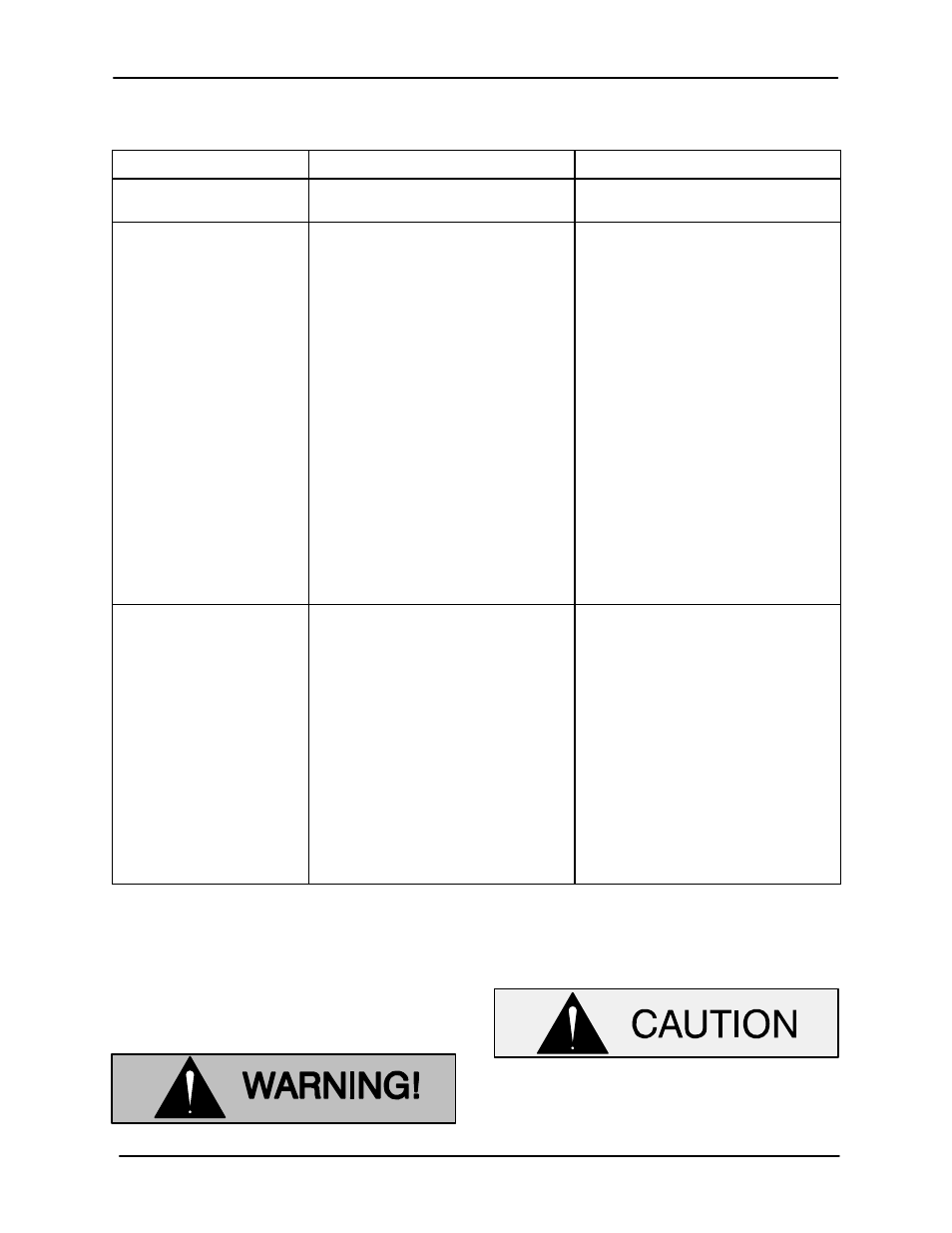
SE SERIES
OM-06495
TROUBLESHOOTING
PAGE D - 2
Table 1. Trouble Shooting Chart (cont.)
TROUBLE
POSSIBLE CAUSE
PROBABLE REMEDY
(AUTOMATIC MODE)
(CONT'D.)
Defective liquid level sensing de
vice(s) or control panel.
Repair or replace defective unit(s).
MOTOR RUNS, BUT
PUMP FAILS TO
DELIVER RATED
DISCHARGE
Discharge head too high.
Low or incorrect voltage.
Discharge throttling valve partially
closed; check valve installed im
properly.
Discharge line clogged or re
stricted; hose kinked.
Liquid being pumped too thick.
Strainer screen or impeller clogged.
Insufficient liquid in sump or tank.
Worn impeller vanes; excessive im
peller clearance.
Reduce head.
Measure control box voltage, both
when pump is running and when
shut‐off.
Open discharge valve fully; check
piping installation.
Check discharge lines; straighten
hose.
Dilute liquid if possible.
Clear clog(s). Stop pump; back flow
may flush away debris.
Stop pump until liquid level rises.
Check impeller and clearance. See
PUMP END REASSEMBLY.
PUMP RUNS WITH
EXCESSIVE NOISE OR
VIBRATION
Pumping entrained air.
Damaged or unbalanced impeller.
Discharge piping not properly sup
ported.
Impeller jammed or loose.
Motor shaft or bearings defective.
Pump cavitation.
Check liquid level in sump; check
position of pump and liquid level
sensing device(s).
Replace impeller.
Check piping installation.
Check impeller.
Disassemble pump and check mo
tor and bearings.
Reduce discharge head, or restrict
flow on low head applications.
ELECTRICAL TESTING
If you suspect that pump malfunctions are caused
by defects in the motor, power cable or control box,
perform the following checks to help isolate the de
fective part.
Obtain the services of a qualified elec
trician to troubleshoot, test and/or ser
vice the electrical components of this
pump.
Be certain to refer to the wiring diagram(s)
in the Installation Operations manual be
fore reconnecting any electrical compo
nents which have been disconnected.