Gorman-Rupp Pumps VG8D3-B 1221466 and up User Manual
Page 8
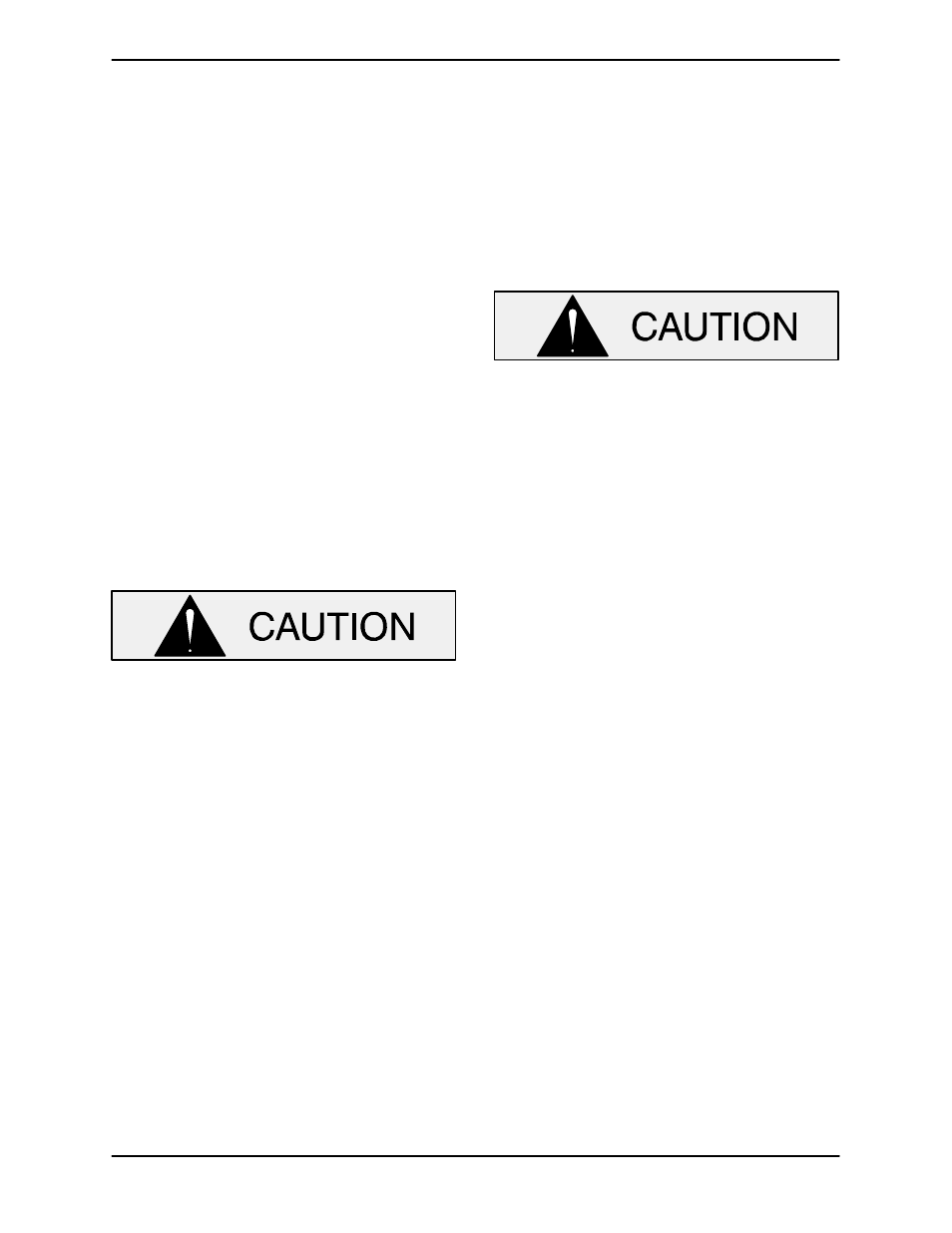
OM-02819
VG SERIES
PAGE B - 2
INSTALLATION
PREINSTALLATION INSPECTION
The pump assembly was inspected and tested be
fore shipment from the factory. Before installation,
inspect the pump for damage which may have oc
curred during shipment. Check as follows:
a. Inspect the pump for cracks, dents, damaged
threads, and other obvious damage.
b. Check for and tighten loose attaching hard
ware. Since gaskets tend to shrink after dry
ing, check for loose hardware at mating sur
faces.
c. Carefully read all warnings and cautions con
tained in this manual or affixed to the pump,
and perform all duties indicated. Note the di
rection of rotation indicated on the pump.
Check that the pump shaft rotates counter
clockwise when facing the pump suction.
Only operate this pump in the direction in
dicated by the arrow on the pump body
and on the accompanying decal. Refer to
ROTATION in OPERATION, Section C.
d. Check all lubricant levels and lubricate as
necessary. Refer to LUBRICATION in the
MAINTENANCE AND REPAIR section of this
manual and perform duties as instructed.
e. If the pump and
power source have been
stored for more than 12 months, some of the
components or lubricants may have ex
ceeded their maximum shelf life. These must
be inspected or replaced to ensure maxi
mum pump service.
If the maximum shelf life has been exceeded, or if
anything appears to be abnormal, contact your
Gorman‐Rupp distributor or the factory to deter
mine the repair or updating policy. Do not put the
pump into service until appropriate action has
been taken.
POSITIONING PUMP
Lifting
Use lifting equipment with a capacity of at least
3,510 pounds (1592,1 kg). This pump weighs ap
proximately 702 pounds (318,4 kg), not including
the weight of accessories and base. Customer in
stalled equipment such as suction and discharge
piping must be removed before attempting to lift.
The pump assembly can be seriously
damaged if the cables or chains used to lift
and move the unit are improperly wrapped
around the pump.
Mounting
Locate the pump in an accessible place as close as
practical to the liquid being pumped. Level mount
ing is essential for proper operation.
The pump may have to be supported or shimmed
to provide for level operation or to eliminate vibra
tion.
SUCTION AND DISCHARGE PIPING
The size of the system piping is not always deter
mined by the nominal suction and discharge port
diameter. Factors such as suction lift, discharge
elevation, and friction losses for the complete sys
tem must be considered to be sure your applica
tion allows the pump to operate within the safe op
erating range shown on page E‐1. In any case, the
suction line should never be smaller than the pump
inlet.
Materials
Either pipe or hose maybe used for suction and
discharge lines; however, the materials must be
compatible with the liquid being pumped. If hose is
used in suction lines, it must be the rigid‐wall, rein
forced type to prevent collapse under suction. Us
ing piping couplings in suction lines is not recom
mended.
Line Configuration
Keep suction and discharge lines as straight as
possible to minimize friction losses. Make mini