Gorman-Rupp Pumps 02K11-X2 3P 684441 and up User Manual
Page 17
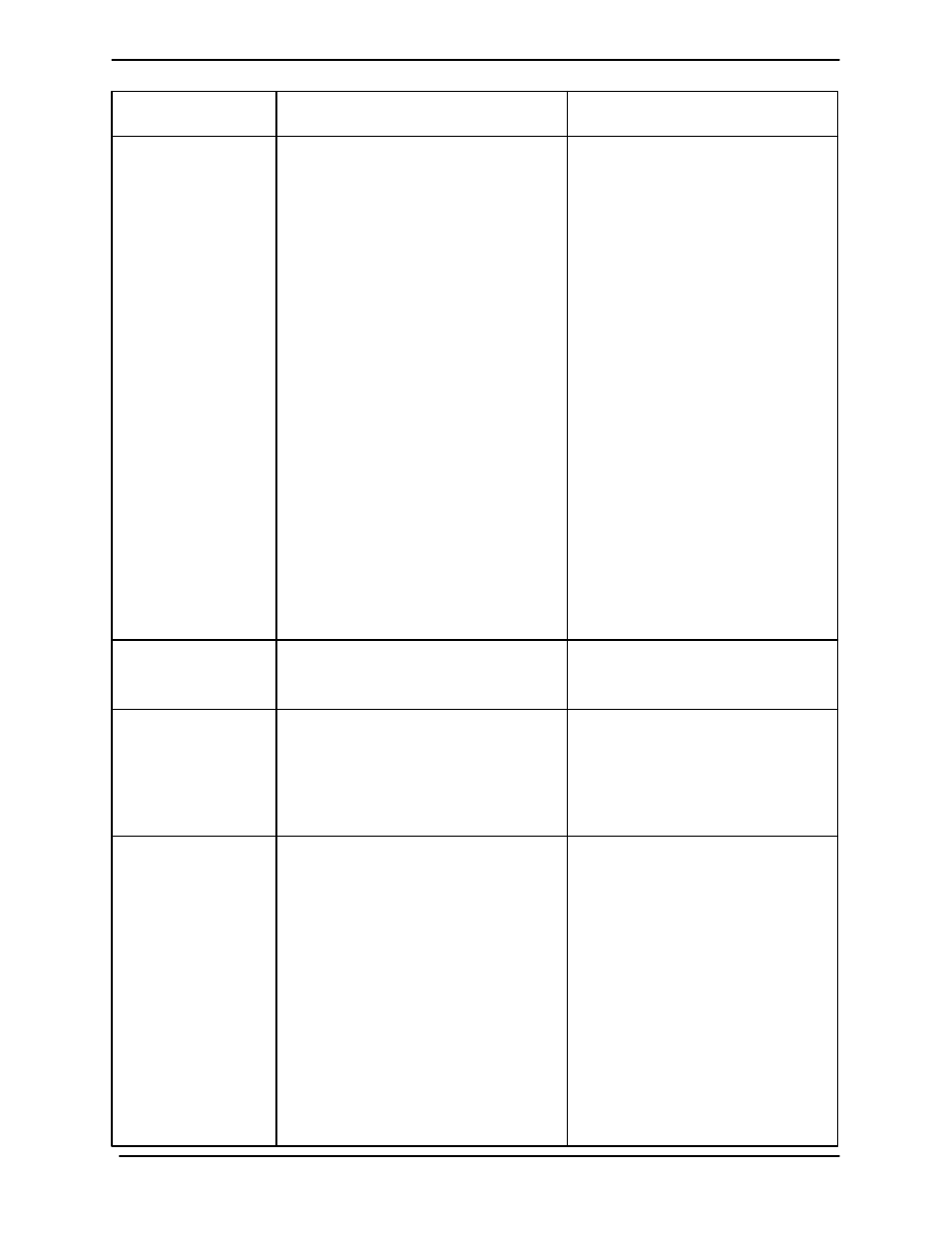
OM-01161
0 SERIES
TROUBLESHOOTING
PAGE D - 2
TROUBLE
POSSIBLE CAUSE
PROBABLE REMEDY
PUMP REQUIRES
TOO MUCH
POWER
PUMP CLOGS
FREQUENTLY
Impeller or other wearing parts worn
or damaged.
Replace worn or damaged parts.
Check that impeller is properly
centered and rotates freely.
Impeller clogged.
Free impeller of debris.
Discharge head too low.
Adjust discharge valve.
Liquid solution too thick.
Dilute if possible.
Liquid solution too thick.
Dilute if possible.
Discharge flow too slow.
Open discharge valve fully to in
crease flow rate, and run power
source at maximum governed
speed.
PUMP STOPS OR
FAILS TO DELIVER
RATED FLOW OR
PRESSURE (cont.)
Strainer clogged.
Check strainer and clean if neces
sary.
Suction intake not submerged at
proper level or sump too small.
Check installation and correct sub
mergence as needed.
Suction lift or discharge head too high.
Check piping installation and install
bypass line if needed. See INSTAL
LATION.
Low or incorrect voltage.
Measure control box voltage, both
when pump is running and when
shut off.
No voltage at line side of circuit
breaker.
Check power source for blown fuse,
open circuit breaker or control box,
broken lead, or loose connection.
EXCESSIVE NOISE
Impeller clogged or damaged.
Pump or drive not securely mounted.
Pumping entrained air.
Locate and eliminate source of air
bubble.
Secure mounting hardware.
Clean out debris; replace dam
aged parts.
Cavitation in pump.
Reduce suction lift and/or friction
losses in suction line. Record vac
uum and pressure gauge readings
and consult local representative or
factory.
Pump running backwards.
Check direction of rotation and cor
rect by interchanging any two motor
leads at control box. (See Pump Ro
tation, Section C).