Gorman-Rupp Pumps 16A20-B 818301 and up User Manual
Page 34
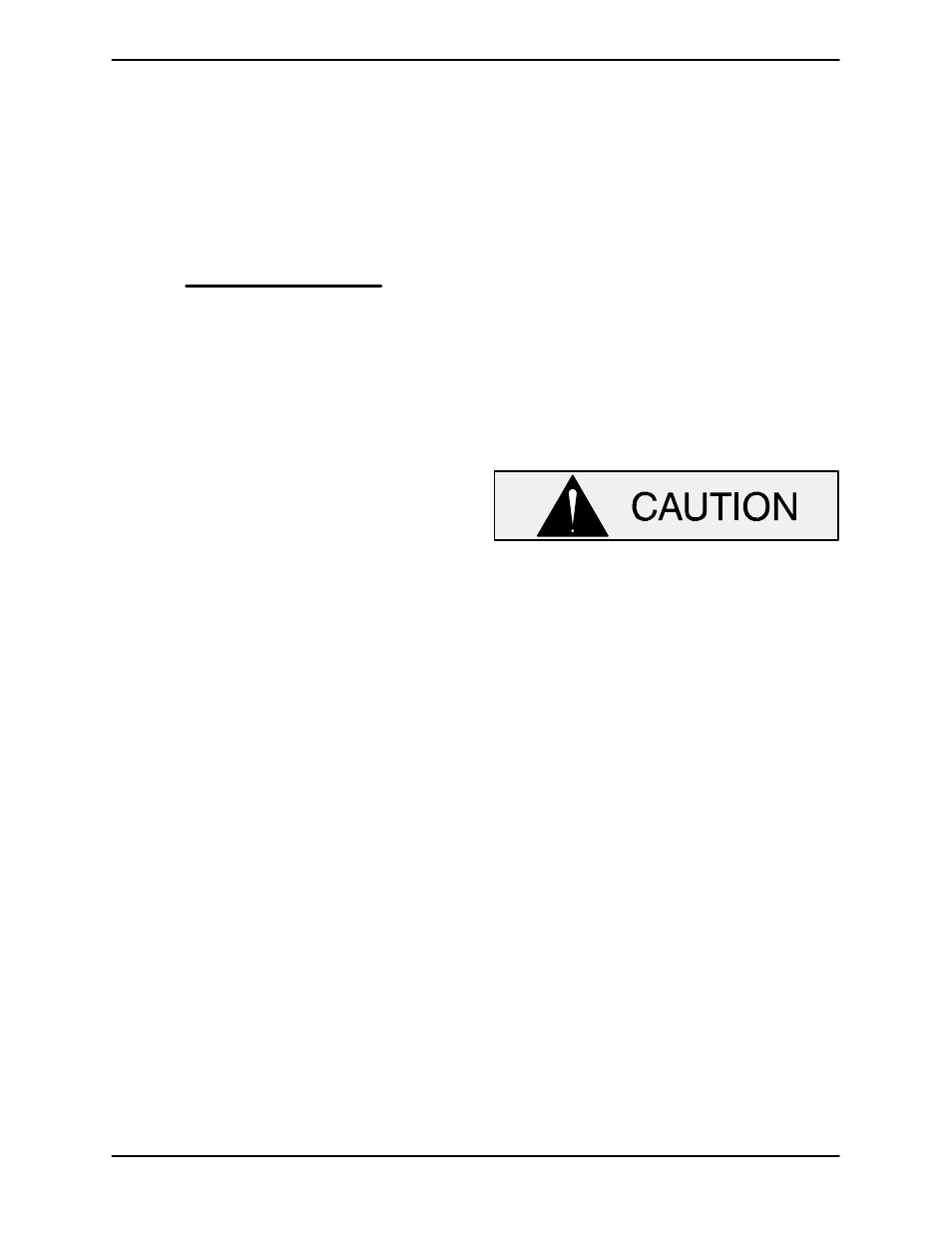
OM‐00710
10 SERIES
MAINTENANCE & REPAIR
PAGE E - 11
valve gasket (85) and weights (84 and 86) using
hardware (82 and 83). Position the assembled
check valve in the mounting slot in the seat.
NOTE
Apply `Permatex Aviation No. 3 Form‐A‐Gasket' or
equivalent compound to the suction flange and
check valve seat mating surfaces before reassemb
ly.
Replace the seat gasket (74) and secure the check
valve and seat to the pump casing with the round
head machine screws (80).
Replace the suction flange gasket (76) and secure
the suction flange to the check valve seat and
pump casing with the hardware (77 and 78).
Final Pump Assembly
Secure the pump to the base with the previously re
moved hardware. Be sure to reinstall any leveling
shims used under the pump mounting feet.
Be sure the pump and power source are securely
mounted to the base.
Install the suction and discharge lines and open all
valves. Make certain that all piping connections are
tight, properly supported and secure. Open all the
valves in the suction and discharge lines.
Be sure the pump and power source have been
properly lubricated, see LUBRICATION.
Remove the fill cover assembly (15) and fill the
pump casing with clean liquid. Reinstall the fill cov
er and tighten it.
Refer to OPERATION, Section C, before putting
the pump back into service.
LUBRICATION
Bearings
The pedestal was fully lubricated when shipped
from the factory. Check the oil level regularly
through the sight gauge (51) and maintain it at the
middle of the gauge. When lubrication is required,
add SAE No. 30 non‐detergent oil through the hole
for the air vent (34). Do not over‐lubricate. Over‐lu
brication can cause the bearings to over‐heat, re
sulting in premature bearing failure.
Under normal conditions, drain the pedestal once
each year and refill with clean oil to the middle of
the sight gauge. Change the oil more frequently if
the pump is operated continuously or installed in
an environment with rapid temperature change.
Monitor the condition of the bearing lubri
cant regularly for evidence of rust or mois
ture condensation. This is especially im
portant in areas where variable hot and
cold temperatures are common.
For cold weather operation, consult the factory or a
lubricant supplier for the recommended grade of
oil.
Seal Assembly
Fill the bottle oiler (30) with SAE 30 non‐detergent
oil. Check the oil level regularly and keep the bottle
oiler full.
Power Source
Consult the literature supplied with the power
source, or contact your local power source repre
sentative.