Structures, drawbar, circle and moldboard – Milton CAT 24M User Manual
Page 6
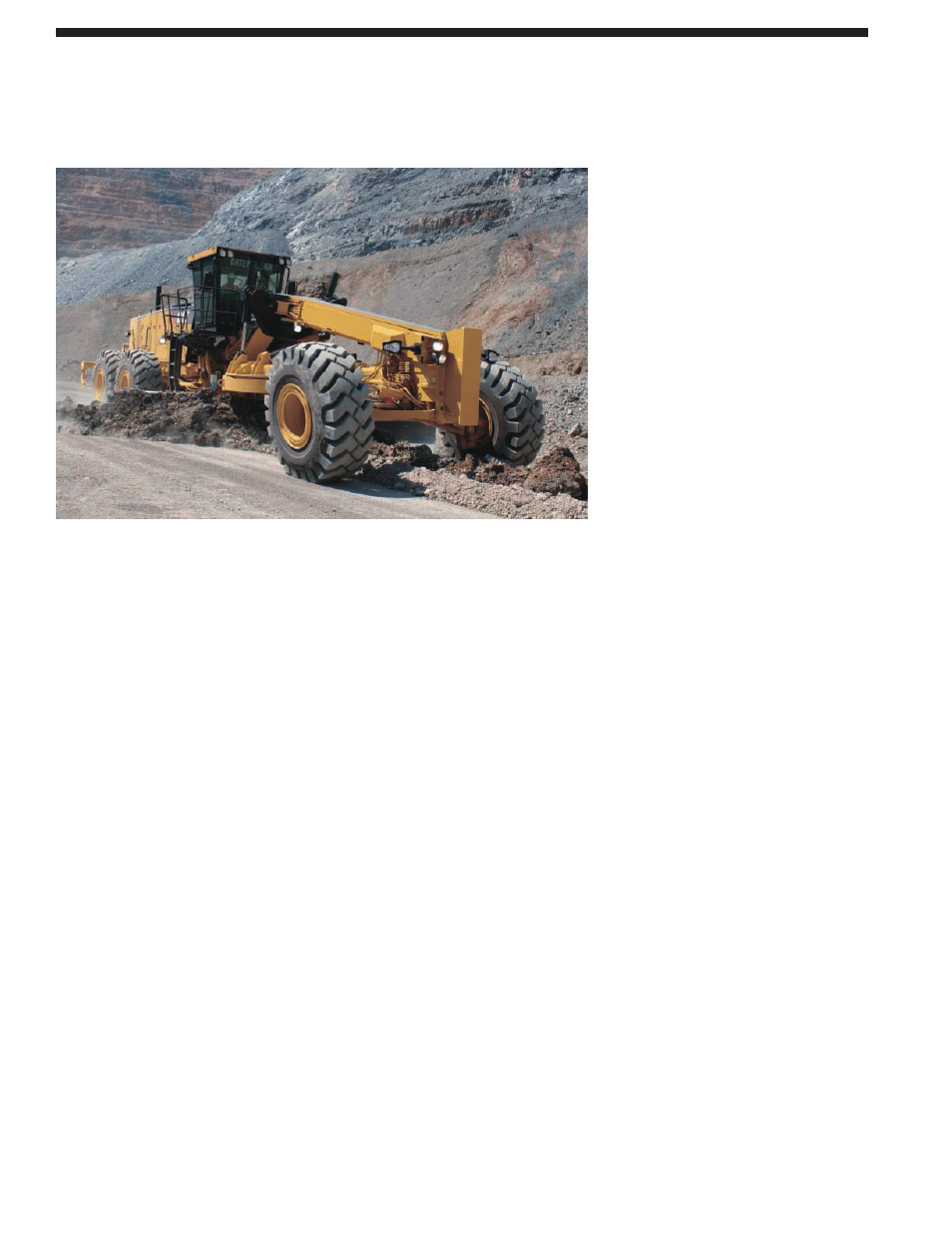
Front Frame Structure. Continuous top
and bottom plate construction provides
consistency and strength. The flanged
box section design removes welds from
high stress areas, improving reliability
and durability.
Rear Frame Structure. Two steel plates
running the full length of the rear frame
are integrated with the box section hitch.
This helps resist torsion loads and ensure
structural durability. The integrated steel
tube unifies the rear frame and supports
the engine, while helping the frame
withstand heavy-duty applications.
Articulation Hitch. A large tapered
roller bearing at the lower pivot carries
loads evenly and smoothly. A mechanical
locking pin prevents frame articulation
to ensure safety when servicing or
transporting the machine.
Circle Construction. A one-piece forged
steel circle is built to stand up to high
stress loads and provide structural
durability. The front 240° of circle teeth
are hardened to reduce wear and ensure
component reliability.
Adjustable Rear Circle Drive.
An adjustable rear circle drive makes
serviceability easier and faster, and
also reduces component wear by
keeping components tight.
Drawbar Construction. The A-frame
drawbar features a box-section design
for high strength and optimum durability.
Yoke Plate. Full-length yoke plate
gives strength, support and protection
to the circle.
Aggressive Blade Angle. With a long
wheelbase the operator can obtain
aggressive moldboard angles, so material
rolls more freely along the length of the
blade. This is particularly helpful when
handling very dry materials or cohesive
soils. Better material control gets the
job done faster, requires less power
and saves fuel.
Replaceable Wear Inserts. Tough,
durable wear inserts reduce rotational
friction for maximum circle torque and
longer component life. They are located
between the drawbar and circle, and
between the support shoes and circle.
High load-resistant brass wearstrips
are placed between the blade mounting
group and moldboard. This sacrificial
wear system can be replaced easily
and helps keep components tight
for fine grading.
Moldboard. The optimal curvature and
large throat clearance help move material
quickly and efficiently. Heat-treated
moldboard rails, hardened cutting edges
and end bits, and large diameter bolts
assure reliability and longer service life.
Push Plate/Counterweight. A front
mounted push plate/counterweight can
be added on the 24M.
Ripper. The 24M standard ripper is made
to penetrate tough material fast and rip
thoroughly for easier material movement
with the moldboard. The ripper includes
three shanks with the ability to add four
more if needed.
6
Structures, Drawbar, Circle and Moldboard
Rugged structures and DCM design deliver maximum durability and productivity.