Festool CMS-OF User Manual
Page 15
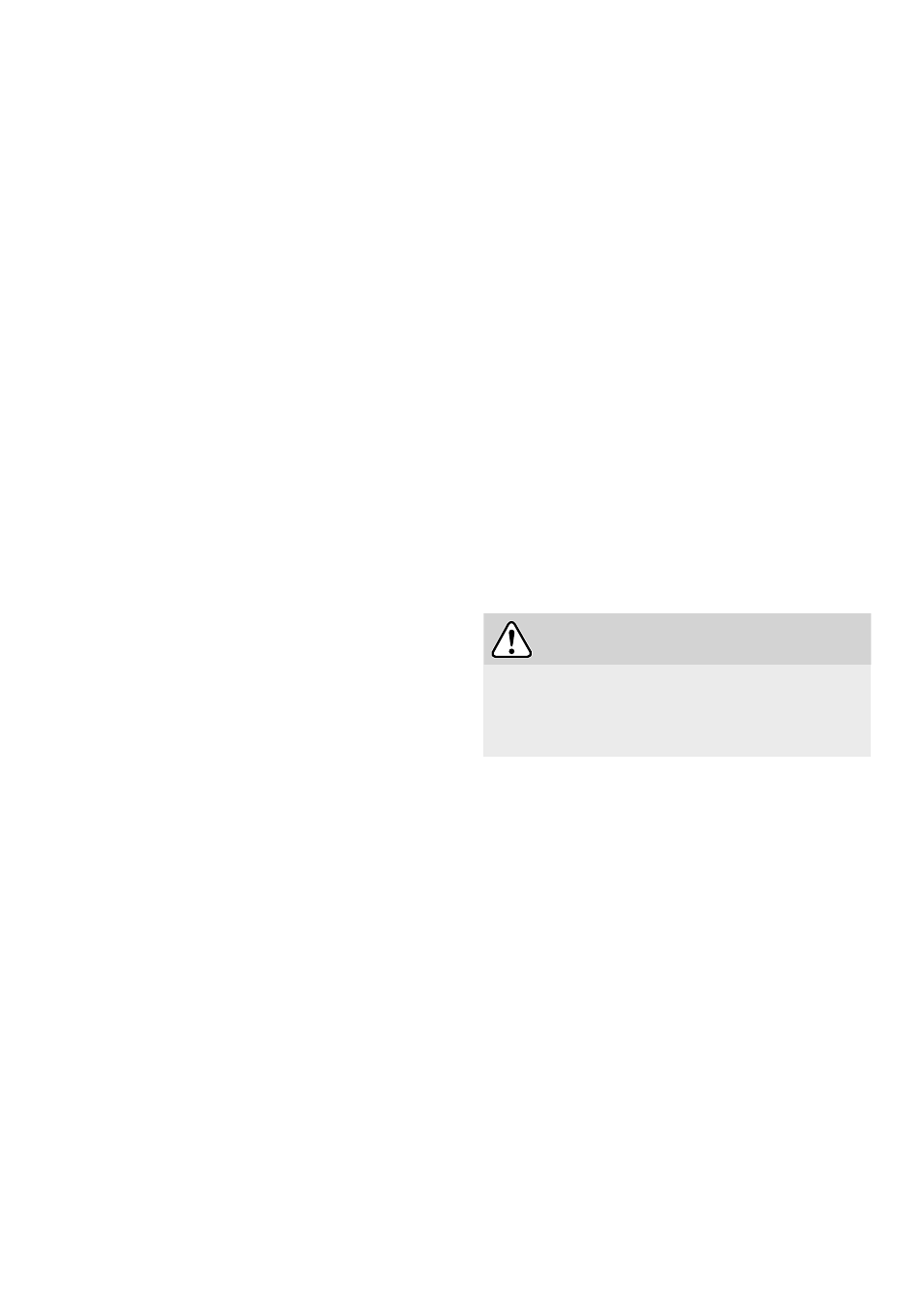
15
• Secure the router stop by inserting the two
screws [13-1] into the holes [12-1]. Use holes
[12-2] if a greater distance is required between
the routing tool and router stop.
Align the router stop with reference to the scales
[13-3] and markings [13-4].
If necessary, you can use the screws [14-2] to
adjust the perpendicularity of the router stop in
relation to the bench surface on both sides.
• Unscrew the rotary knob [15-1] on the press-
down fi xture.
• Slide the press-down fi xture all the way into the
opening [15-2] on the router stop.
• Tighten the rotary knob [15-1].
7.2
Adjusting the router stop
Adjusting the rulers
The distance between the two rulers on the router
stop and the cutting circle of the cutter tool must
always be between 2 mm to 5 mm [16]. Adjust the
distance as follows:
• Loosen the screws [17-1] and [174].
• Slide the rulers [17-2] and [17-3] apart.
• Set the routing tool in the required position (see
7.7 Adjusting the routing tool height).
• Move the rulers [17-2] and [17-3] until they are
between 2 and 5 mm from the cutting circle of
the routing tool.
• Tighten the screws [17-1] and [17-4].
If the adjustment range of either ruler is insuf-
fi cient:
• Loosen the screws [14-1] on both sides of the
router stop.
• Move the ruler to the required position.
• Tighten the screws [14-1] on both sides.
Adjusting the router stop in parallel
Proceed as follows to adjust the entire router stop
for profi le routing, for example:
• Loosen the screws [18-1] and [18].
• Move the router stop to the required position Y
(overhang of the cutting circle in relation to the
rulers) [16].
Align the router stop with reference to the scales
[13-3] and markings [13-4].
• Tighten the screws [18-1] and [18-2].
Adjusting the runout ruler
Proceed as follows to adjust the runout ruler
[19-5] in relation to guide ruler [19-1]:
• Loosen the screw [19-2].
• Use a strip of straight material to align the guide
and runout rulers in relation to one another.
• Only turn the dial ring [19-3] to reset to zero.
• Turn the adjusting wheel [19-4] to set the desired
dimension X (overhang of the guide ruler in rela-
tion to the runout ruler). The distance between
each line on the dial ring [19-3] is 0.1 mm - one
full turn of the ring represents 1 mm.
• Tighten the screw [19-2].
Adjusting the press-down fi xture
Adjust the bearing shoe on the press-down fi xture
so that the workpiece is guided straight and does
not stray to either side. The bearing shoe prevents
inadvertent contact with the cutter tool.
• Unscrew the rotary knob [20-5].
• Lower the vertical bearing shoe [20-3] down to
the workpiece.
• Tighten the rotary knob [20-5].
• Loosen the screw [20-4].
• Slide the horizontal bearing shoe [20-1] down
to the workpiece. If the workpiece is wider than
the adjustment range of the horizontal bearing
shoe, turn the horizontal bearing shoe verti-
cally.
To turn the horizontal bearing shoe, release the
lever [20-2] and swivel the complete press-down
fi xture upwards.
WARNING
Risk of injury
•Before working with the machine, always
swivel the press-down fi xture down again until
the lever [20-2] engages.
• Tighten the screw [20-4].
7.3
Fitting the curved guard
Install the curved stop (curved guard) when
performing routing work on cambered (curved)
workpieces.
• Secure the curved guard [21-2] by inserting the
three screws [21-1] in the three holes [21-5] and
attach the guide rail [21-3] by inserting the long
screw in the hole [21-4].
7.4
Adjusting the curved guard
Adjust the curved guard until the transparent
protective cover [22-1] rests on the workpiece.
• Loosen the two screws [22-2].
• Adjust the height of the protective cover [22-1]
so that it rests on the workpiece.
• Tighten the two screws [222].
Adjust the guide rail:
• Loosen the screw [22-5].
• Adjust the angle and height of the rail until the
tip rests against the ball bearing guide on the