Troubleshooting – Lincoln Electric FLEXTEC 450 CE User Manual
Page 31
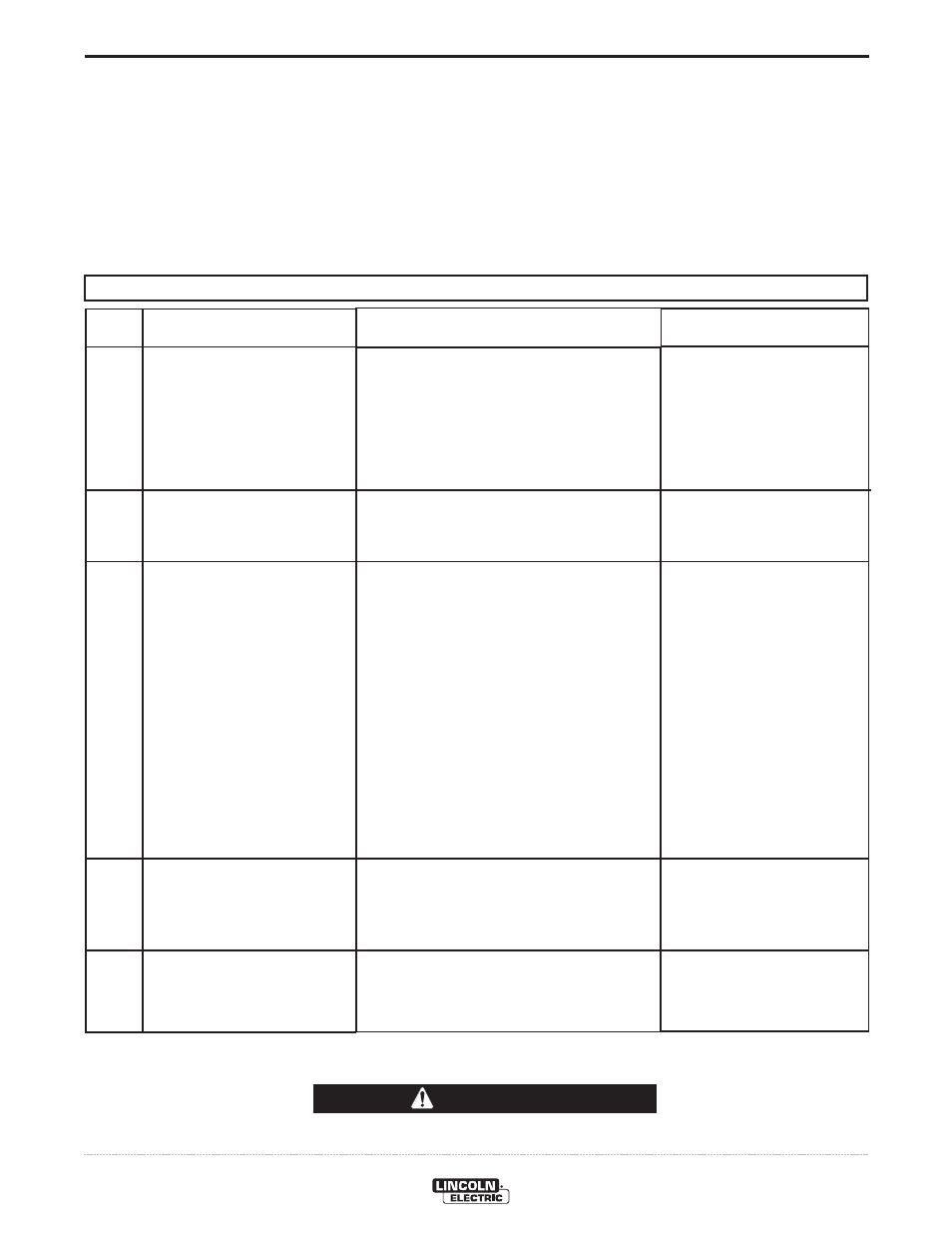
E-4
TROUBLESHOOTING
E-4
FLEXTEC™ 450 CE
Observe all Safety Guidelines detailed throughout this manual
If for any reason you do not understand the test procedures or are unable to perform the tests/repairs safely, contact your
Local Lincoln Authorized Field Service Facility for technical troubleshooting assistance before you proceed.
CAUTION
USING THE STATUS LED TO TROUBLESHOOT SYSTEM PROBLEMS
Errors are displayed on the user interface. In addition, there are status lights on the control pc board and the
switch pc board that contain error sequences.
Included in this section is information about the Status Lights and some basic troubleshooting charts for both
machine and weld performance.
The status lights on the main control board and the switch pc board are dual-color LEDʼs. Normal operation for
each is steady green.
(For Code 11942 only)
Error Codes for the FLEXTEC™ 450 CE
Error
Code#
21
31
36
45
712
Description
Device that controls sequence
of the welding operation halt-
ed due to an error.
Primary Over Current.
Thermal Fault
VRD™ Voltage limit exceeded.
Communication Fault
Check the input power (voltage and fre-
quency). Verify the primary reconnect is
properly configured for the input voltage.
Machine shut off output due to elevated
internal temperatures.
During OCV, the voltage exceeded allow-
able VRD™ levels.
• Verify dip switch settings are correct for
the input voltage.
CAN communication between the control
pcb and switch pcb has been interrupted.
Weld Terminals Remote:
Re-trigger to recover from
error.
Weld Terminals Local:
Toggle Remote/Local Switch
to recover from error.
Machine needs to be turned
off and back on to reset.
1. Check for material block-
ing intake or exhaust lou-
vers.
• Blow air in the rear lou-
vers to clear dirt from the
fan.
Note: The Fan As Needed
circuitry automatically
shuts off the fan 5 minutes
after welding has stopped.
2. Welding output ratings
may have been exceeded.
Allow the machine to cool
down and reset.
Machine needs to be turned off
and back on to reset.
Inspect harness for damage /
loose connections.
Corrective Action
Possible Cause