American metal ware, Brewers troubleshooting guide (cont’d), Problem possible cause solution – Grindmaster RAPS-430 User Manual
Page 8
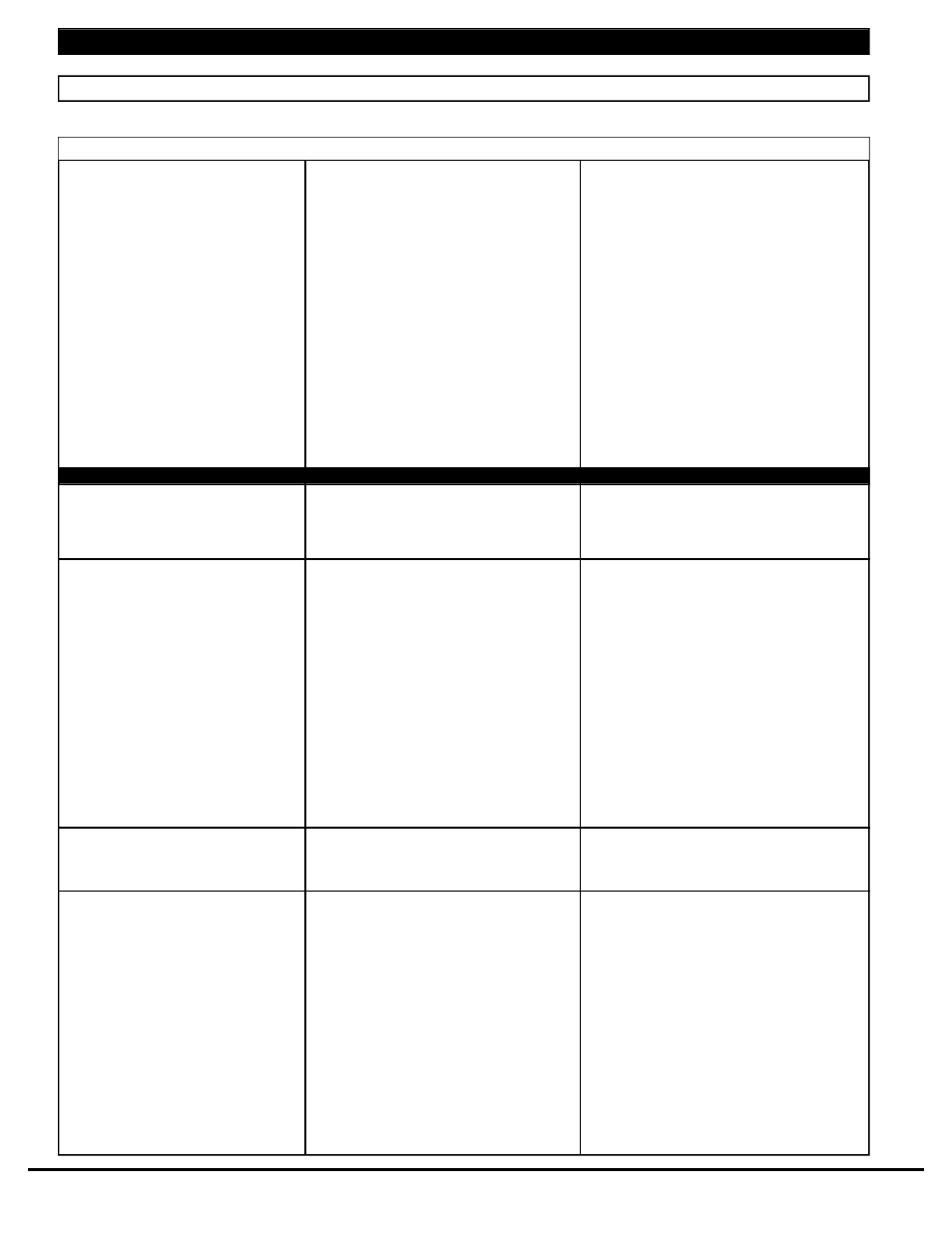
AMERICAN METAL WARE
®
BREWERS
TROUBLESHOOTING GUIDE (cont’d)
• Contactor faulty.
• Heater faulty.
• Control board is faulty.
• Heater faulty.
Tank does not heat (cont’d)
Brew recovery time is very long
Brew volume too large or too small
• Ensure that coil on heater relay is energized by
ensuring that there is 12Vac between the blue
and white wires attached to the relay. Check
each side of the contactor (Line and Load) at
each pole for continuity. If the contactor coil is
energized and there is an open circuit across
any of the contactor poles, replace contactor.
• Check resistance across element(s) with power
conductors disconnected. If resistance is much
less than 8 Ohms or much more than 15
Ohms, replace heater(s).
• Check to ensure proper connection between
connector CN2 and control board. Check for
proper connections in all heater control
circuitry. Check for proper connections between
N terminal of contactor coil and terminal block.
If connector CN2 is securely attached to control
board and all connections are secure and
functioning except there is not 120Vac across
contactor coil terminals, replace control board.
• Check resistance across element(s) with power
conductors disconnected. If resistance is much
less than 8 Ohms or much more than 15
Ohms, replace heater(s).
• Review timer settings versus portion size.
Adjust timer to desired value or select different
portion size.
• Compare time setting to either factory setting or
initial user setting to determine if it has been
changed. Adjust timer to desired value.
• Check to see that fill valve cycles on and off
frequently during brew cycle when all brew
heads are used simultaneously. Check to
ensure that water supply line is 3/8” and
pressure is between 30 and 70 psi. Supply
water at adequate pressure and flow rate.
• Visually check for clogging of holes in brew
head. Clean all hoses.
• Visually inspect brew valves at hose
connections. Clean lime from valve. Seat, cup
or entire valve may need replacement.
• Portion selected on touchpad not correct.
• Timer not set properly.
• Water supply pressure or flow rate not
adequate.
• Sprayhead clogged.
• Brew valves clogged with lime deposits.
BREWING PROBLEMS
Problem Possible Cause Solution
• Water supply pressure fluctuates.
• Check water pressure with and without other
appliances operating. Plumb water supply so
that water pressure is not significantly affected
by other appliances.
Brew volume erratic
NOTE: Small variations from batch
to batch are normal.
Brew cycle will not start
• Momentary switch to indicate container in
place (ICB only) not engaged or faulty.
• Brew circuit connections not secure.
• Circuit breaker tripped or faulty.
• Check to see that container fully engages
switch. Check for continuity across switch is
engaged. If fully engaged switch does not
complete circuit across terminal off switch,
replace switch.
• Check to see that connector (CN3 or CN4) is
securely connected to control board. Check to
see that all connections from controller through
brew valve and through N terminal of terminal
block are secure. Secure connections.
• Check to see if breaker reset button is out,
indicating a tripped breaker. If breaker is
tripped, determine cause and reset; replace
breaker if faulty.
Page 8