Maintenance – Intek 100 User Manual
Page 14
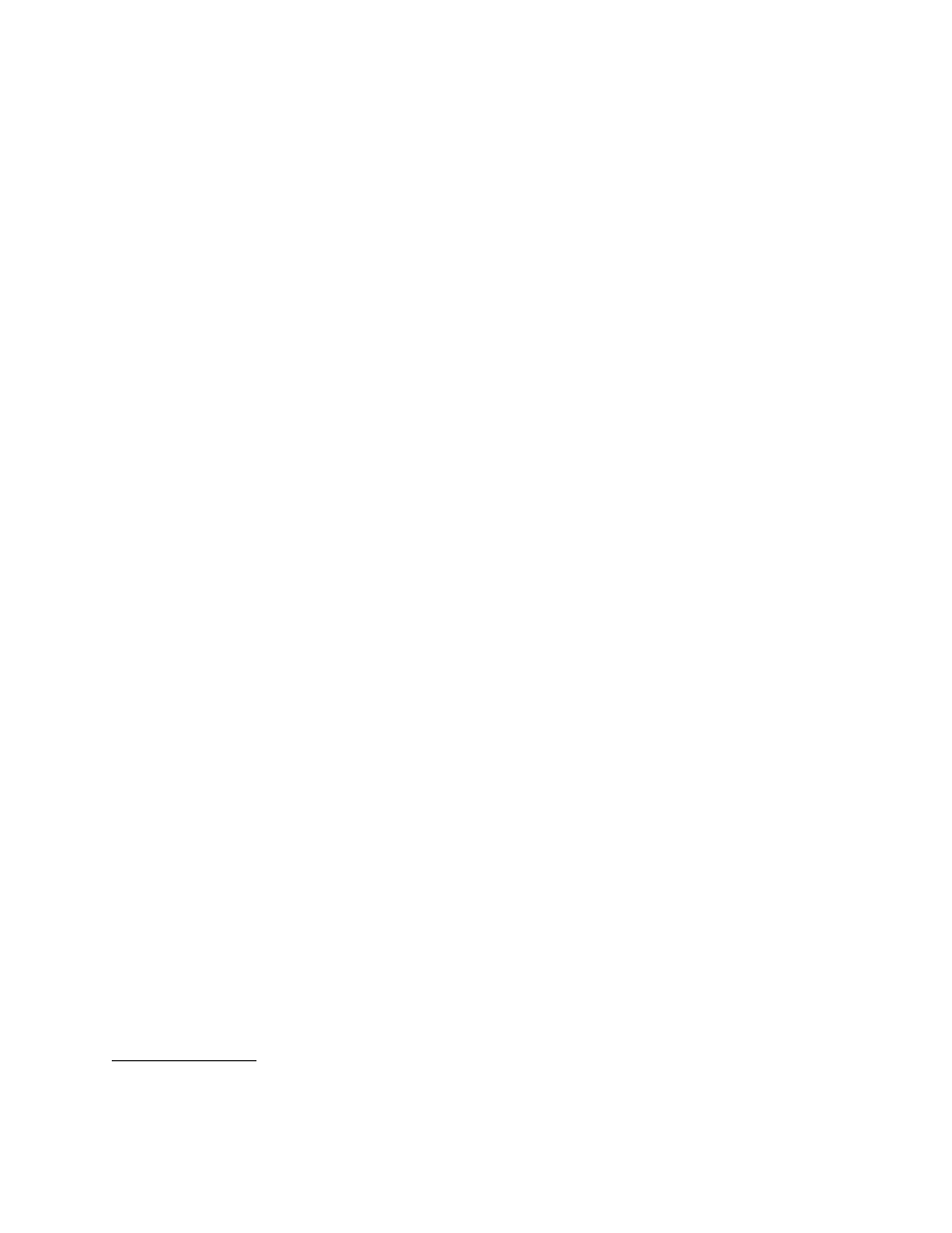
- 12 -
MODEL100 REV D.wpd
SECTION 4
!
MAINTENANCE
4.1 GENERAL MAINTENANCE
Certain precautions should be taken to insure proper performance of all models of flow instruments.
Since the measurement technique involves a signal resulting from heat transfer to the flowing medium,
care should be exercised to prevent build-up of varying layers on the walls of the transducer. Layers
such as bacterial growth, dried paints, gas bubbles and non-solubles can result in measurement below
actual flow rates. Periodic checks and cleaning should be performed to insure a clean pipe or probe
surface.
It should be part of normal maintenance procedure to check the system for proper functioning.
Experience and other observable conditions should be utilized to determine the frequency of inspection.
Long term drift in the unit calibrations is not expected, but if a single point recalibration is required,
refer to SECTION 4.2. To test the flow switch action (if that option was ordered), the flow rate should
be reduced below (for low flow switch) or raised above (for high flow switch) the switching level. Then
check and insure relay action and continuity of the shut down or warning circuits which it operates.
The joints of all intrusive probes tips should be inspected for wear and corrosion.
4.2 SINGLE POINT FIELD CALIBRATION
When field calibration is required, for any reason, the simplest adjustment is a single point linear offset,
and this should usually be tried first. All calibrations should be done at normal operating temperature.
When a single point calibration (or recalibration) is required, it is performed as follows:
Establish a known flow rate in the upper third of the calibrated range that is shown on the output
curve (Figure 2). Adjust calibration potentiometer P2 (cal), Figure1, for a correct output reading
or signal.
If P2 runs out of adjustment before the meter is reading correctly, P1 (see Board Layout P.17) can be
used to further offset the signal. Turning P1 clockwise decreases the signal. (Note: P1 has no effect
on some meters.)
Sometimes you may find the single point calibration is not sufficient to align the output over a wide flow
rate range. If so, a two-point offset/gain calibration can be performed as described below.
A.
Establish a known flow rate at the low end (10-15% of full scale) of the factory calibrated
range (Figure 2, page 18).
1
Adjust P2 potentiometer, Figure 1, for an accurate output signal.
B.
Establish a flow rate near 90-95% of full scale.
1
Adjust "Flow Span" potentiometer, P3
(Figure 1) for an accurate output signal.
C.
Repeat steps A and B until desired accuracy is achieved. Record flow vs. output relationships
for various flows and compare with output curve. Construct a new calibration curve if needed.
1
The flow meter output must have stabilized before any adjustment is made. A strip chart or data logger
monitoring of the output can be v ery helpful in determining when the flow has entered steady-state conditions,
especially at low or noisy flows.