Outlawpg4, Maintenance & tips, Troubleshooting – HornBlasters Outlaw CX Series User Manual
Page 5: Can’t figure it out
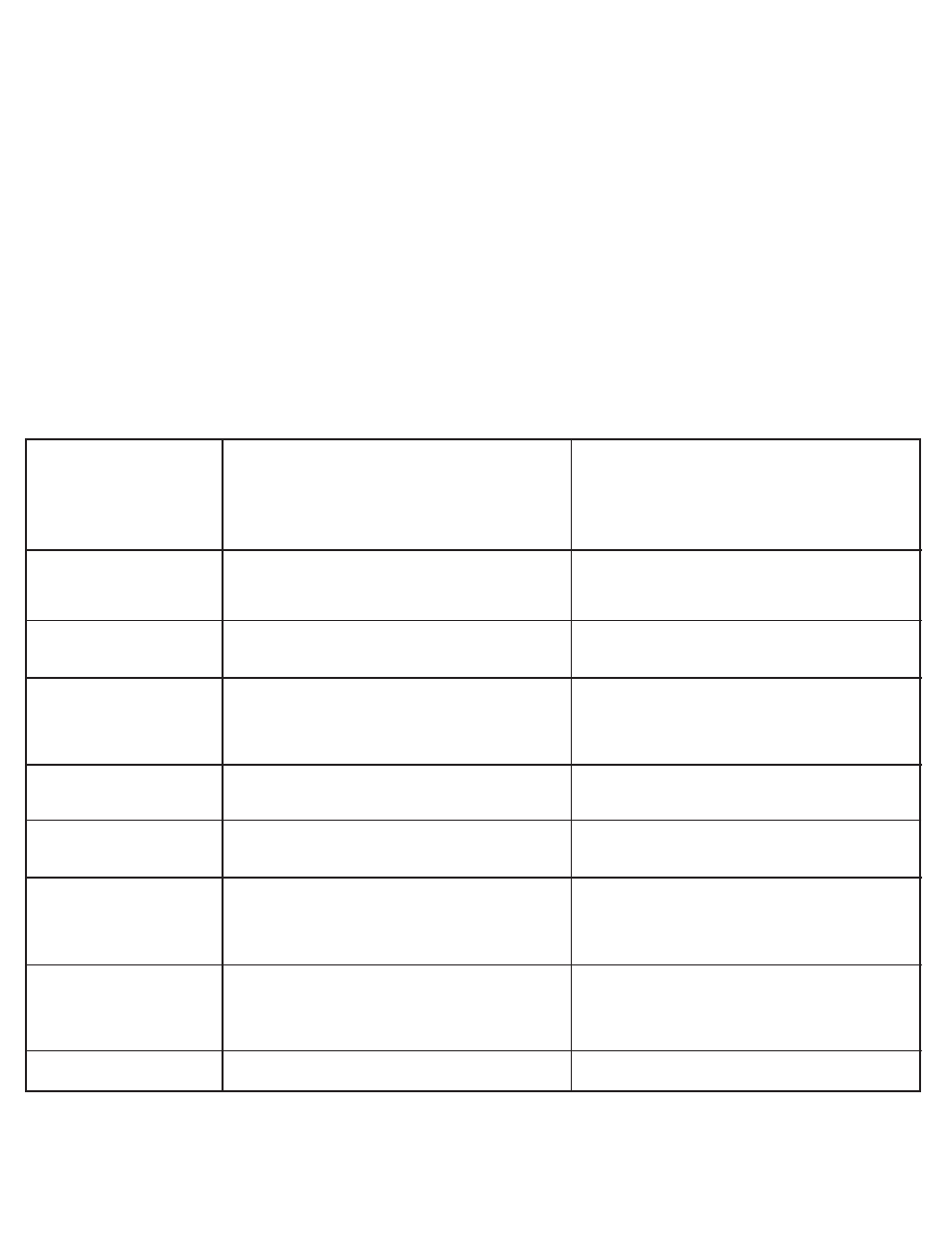
Maintenance & Tips
Disconnect electrical components and drain you air system before performing maintenance.
4
General Air Horn System Maintenance
• Check your air horns for debris when appropriate and at least once a month and clean when necessary.
• Drain your air system at least every other week, to remove any condensation buildup on the inside of you air tank.
• Make sure you air compressor is clean and free from debris at all times.
• Periodically change your two stage air filter on your compressor.
Tips
• Make sure your engine is running when you air compressors are in use to insure proper voltage and to prevent damage to
your system.
• Do not run your compressor above its maximum rated working pressure. Doing so will not only void you warranty, but may
also damage your compressor.
• The air horns are pre-tuned to a locomotive chord and to their loudest possible tone. Do not adjust the tuning screw on the
horns. Doing so will void your warranty and may damage the horns if improperly adjusted.
Troubleshooting
Problem
Air horn will not sound.
1. No pressure in air tank.
2. No power or toggle switch in ‘Off’ position.
3. Blown fuse.
4. Loose connections or bad ground in air valve
circuit (circuit 1).
1. Check that air tank is pressurized.
2. Make sure all toggle switches are on.
3. Disconnect electrical components and
replace fuse.
4. Check that all electrical circuits are secure and not
corroded.
Horn tone changes when
sounded
1. A side fitting as used to connect the air source (line
from valve) to the 4-point banjo manifold.
2. Air line connecting the horns is not of equal length.
1. Check that air source (line coming from valve) is
entering the center fitting of the 4-point banjo manifold.
2. Check that the air line connecting each horn to the
4-point banjo manifold is of equal length.
Excessive moisture in horn or
safety discharge.
1. Excessive water in tank.
2. Compressor is exposed to high humidity.
1. Depressurize tank using safety, then drain tank. Tilt the
tank to drain moisture and drain more frequently.
2. Move the compressor to an area with less humidity.
Compressor will not run.
1. No power or toggle switch in ‘Off’ position.
2. Blown fuse.
3. Motor overheat.
4. Faulty pressure switch.
1. Make sure all toggle switches are on.
2. Disconnect compressor from power & replace fuse (35A).
3. Let compressor cool off for about 30 minutes for thermal
overload switch to reset.
4. Replace pressure switch.
Thermal overload protector cuts
out repeatedly.
1. Lack of proper ventilation/ambient temperature too
high.
2. Compressor valves failed.
1. Move compressor to a well ventilated area or an area
with a lower ambient temperature.
2. Replace air compressor.
Excessive knocking or rattling
1. Loose mounting bolts.
2. Worn bearing on eccentric or motor shaft.
3. Cylinder or piston ring is worn.
1. Tighten bolts.
2. Replace compressor.
3. Replace compressor.
Tank pressure drops when
compressor shuts off
1. Loose drain cock.
2. Air valve or check valve is leaking.
3. Loose connections.
4. Defective safety valve.
1. Tighten drain cock.
2. Replace air valve or check valve.
3. Check all air connections with soap and water solution
and tighten as necessary.
4. Replace safety valve.
Compressor runs continuously
and air flow lower than normal
1. Excessive air usage.
2. Loose connections.
3. Worn piston ring or inlet valve.
4. Clogged air filter element.
1. Decrease air usage.
2. Check all connections with soap and water solution
and tighten as necessary.
3. Replace compressor
4. Replace air filter element.
Can’t Figure It Out?
Compressor runs continuously
causing safety valve to open.
1. Faulty pressure switch.
2. Defective safety valve.
1. Replace pressure switch.
2. Replace safety valve.
No problem! Give us a call at 813-783-8058, or email at [email protected] and we’ll be more than happy to help you fix you system. Also feel free
to visit our online horn community, www.trainhornforums.com, for more information.