Actron SCAN TOOL CP9110 User Manual
Page 8
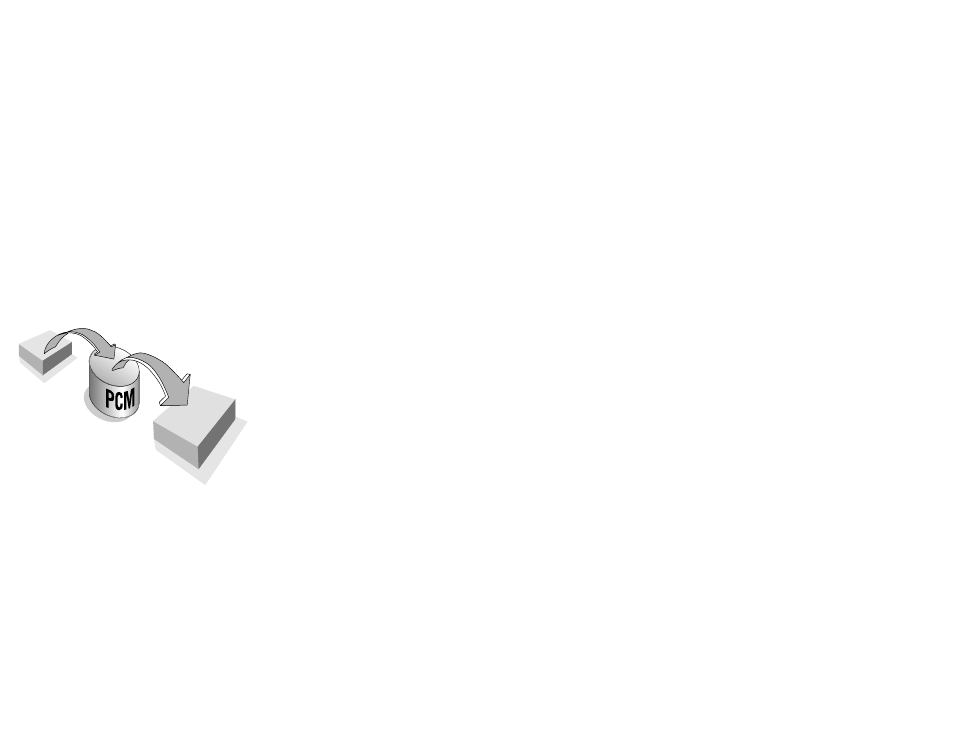
OUTPUT
AC
TUA
TORS
SENSORS
INPUT
BRAINS OF THE
COMPUTER
Some examples of sensors: thermistors
(for temperature readings), potentiom-
eters (like a throttle position sensor), re-
lays (for voltage and signal readings), and
signal generators (such as an 02 sensor).
The network of sensors has the job of
delivering information the computer needs
to know by converting it into electrical
signals the computer can understand. Sig-
nals running from sensors to the PCM are
referred to as “inputs.”
Sensors monitor key things such as:
• Engine Temperature
• Intake Manifold Vacuum
• Throttle position
• RPM
• Incoming Air Temperature
• Volume of Incoming air
• Air Fuel Ratio, in percentage ( % )
Switches and Actuators are electric de-
vices energized by the computer to allow
commands to perform a specific function.
Switches are often called relays (such as
the coolant fan switch). Actuators might
include solenoids (such as fuel injector
valves) and small motors (such as the Idle
Speed Control). Not all of the computer’s
outgoing signals are routed to switches
and actuators. Sometimes information is
sent to other system computers like trans-
mission, brakes, ignition modules, and trip
computers. Signals running from the PCM
to other components are called “outputs.”
How the computer controls fuel deliv-
ery
Engine operation and emissions perfor-
mance depend upon precise fuel delivery
and ignition control. Early computer sys-
tems controlled fuel by electronically ad-
justing the carburetor metering and jet
systems. Soon, however, this was re-
placed by the more precise fuel delivery of
fuel injection.
In an electronically carbureted system,
the computer simply controls fuel flow
based on how far the throttle is opened by
the driver. The computer “knows” how
much air can flow through the carburetor
at various throttle openings, and adds the
appropriate amount of fuel to the mixture
at the carburetor.
Fuel injection is somewhat more sophis-
ticated in the way it delivers fuel. The
computer still adds an appropriate amount
of fuel to the entering air, but now it uses
fuel injectors (either in a throttle body or at
each intake port). Fuel injectors are far
more precise than carburetor jets, and
create a much finer fuel “mist” for better
combustion and increased efficiency. In
addition, most fuel injection systems have
ways of measuring exactly how much air
is entering the engine, and can calculate
the proper air/fuel ratio using lookup
tables. Computers no longer have to “es-
timate” how much air the engine is using.
In many modern systems, the computer
also uses information provided by sen-
sors to give it an idea of how well it is doing
its job, and how to do it better. Sensors can
tell the computer how warm the engine is,
how rich or lean the fuel mixture is, and
whether accessories (like the air condi-
tioner) are running. This feedback infor-
mation allows the computer to “fine tune”
the air/fuel mixture, keeping the engine
operating at its peak.
What the Computer needs to know:
• Engine operating condition. Sensors
used are: coolant temperature, throttle
14
15
position, manifold pressure (vacuum),
air flow and RPM.
• Air intake. Sensors used are: mass air
flow, manifold absolute pressure, mani-
fold air temperature and RPM.
• Air/fuel mixture status. Sensors used
are: oxygen sensor(s).
NOTE: Not all engines use every sensor
listed above.
Open and Closed Loop Modes:
Open or closed loop operation refers to
the way the computer is deciding how
much fuel to add to the air entering the
engine. During cold start and other low
demand, low temperature situations, the
computer operates in open loop mode.
This means that it is relying on a set of
internal calculations and data tables to
decide how much fuel to add to the incom-
ing air. It uses sensors such as the coolant
temperature sensor (CTS), the throttle
position sensor (TPS), and the manifold
absolute pressure sensor (MAP) to deter-
mine optimum mixtures. The important
difference here is that it
does not
check to
see if the mixtures are correct, leaving the
computer adjustment loop open.
In closed loop mode, the computer still
decides how much fuel to add by using the
sensors listed above, and by looking up
the appropriate numbers on a data table.
However, it now checks itself to determine
whether the fuel mixture is correct. It is
able to check itself by using the informa-
tion provided by the oxygen sensor(s)
(O2S) in the exhaust manifold. The oxy-
gen sensors will tell the computer if the
engine is running rich or lean, and the
computer can take steps to correct the
situation. In this way, the computer closes
the adjustment loop by checking itself and
making necessary corrections. It should
be noted that the O2 sensors must be at a
very high operating temperature (approxi-
mately 650° F) before they will begin to
feed information back to the computer.
This is why open loop mode is neces-
sary—to give the O2 sensors time to warm
up to operating temperature.
As long as the engine and O2 and Coolant
Temperature Sensors are at operating tem-
perature, the computer can operate in the
closed loop mode. Closed loop mode in-
sures that the air/fuel mixture is at the ideal
14.7:1 air/fuel ratio needed for efficient
combustion. But in stop and go cycles, the
O2 sensor may in fact cool down enough
that the computer will need to rely on a set
of internal parameters and go into open
loop mode again. In some cases, this may
also happen during extended periods of
idling. Many newer vehicles now use
heated O2 (HO2S) sensors to prevent this
condition.
In many vehicles, the computer controls
other systems related to open and closed
loop modes, including idle speed, elec-
tronic spark control, exhaust gas recircula-
tion, and transmission torque converter
clutches. In open loop mode, some of these
systems will be adjusted to speed the warm-
ing of the engine and get the computer into
closed loop mode as quickly as possible.
OBD II: The Next Horizon
In 1994, many manufacturers began equip-
ping cars with a new class of computer
technology which puts more processing
power under your dash than ever before. It
is called On-Board Diagnostics, Second
Generation, or OBD-II. It is required on all
vehicles sold in the US beginning January
1, 1996 (though most domestic manufac-
turers introduced it earlier than required),
and offers increased system monitoring
and diagnostic information. This new sys-
tem will store a library of 400 general
trouble codes and another 400 manufac-
turer-specific codes. These codes cover
Body Systems (B-Codes), Chassis Sys-
tems (C-Codes), and Power Train Systems