Actron SCAN TOOL CP9110 User Manual
Page 14
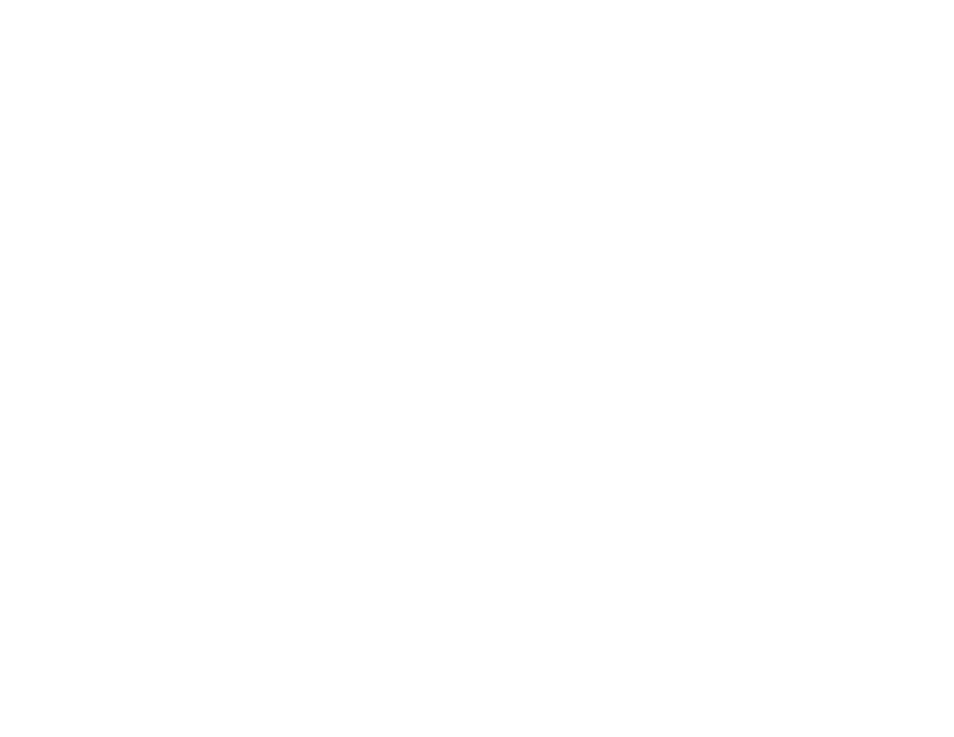
26
ESC: Electronic Spark Control. This is an ignition
system function that works on vehicles having a
knock sensor mounted on the engine block. The
knock sensor is wired to circuitry in a separate
module (early version) or inside the PCM (later
versions). If the sensor detects engine knock, the
ESC function alerts the PCM which will immedi-
ately retard the spark to eliminate the knocking
condition.
EST: Electronic Spark Timing. An ignition system
where the PCM controls the spark advance
timing. A signal called EST goes from the PCM to
the ignition module which fires the spark coil. The
PCM determines optimum spark timing from sen-
sor information – engine speed, throttle position,
coolant temperature, engine load, vehicle speed,
Park/Neutral switch position, and knock sensor
condition.
FBC: Feedback Carburetor. This is used on early
versions of computer-controlled engines. It is a
carburetor which can have its fuel delivery modi-
fied by an electronic signal from the PCM. The
signal controls a mixture control solenoid (MCS)
attached to the carburetor body.
Ford Electronic Engine Control IV (EEC-IV):
This is the name of Ford’s Powertrain Control
Module (PCM) used in all Ford cars and trucks
since the mid-1980’s. It is designed to be read by
aftermarket scan tools. Earlier versions of this
PCM were referred to as EEC-I, EEC-II, or EEC-
III, and were only accessible by the dealer via a
specific diagnostic tool. On carbureted vehicles,
Ford used a system called the Microprocessor
Controlled Unit (MCU), which is accessible through
an adapter similar to the EEC-IV’s. Other varia-
tions of the EEC-IV vehicle adapter are used on
Ford’s hybrid vehicles, such as the Probe and some
Escort/Tracer models, which use Mazda PCMs
and have different protocols and codes. Informa-
tion on these vehicles is widely available, and
most scan tools support these vehicles as well as
the standard Ford EEC-IV systems. Ford’s diag-
nostic strategy offers several avenues to access
codes and test procedures.
Fuel Injector: An electronically controlled flow
valve. Fuel injectors are connected to a pressurized
fuel supply (fuel pressure is created by a fuel pump).
No flow occurs when the injector is off (not energized).
When the injector is energized, it opens fully, allowing
fuel to flow. The PCM controls fuel delivery by varying
the amount of time the injector solenoids are turned on.
Functional Tests: These are tests of PCM-
controlled systems, such as the fuel pump, the
“Check Engine” light, and other switches and
actuators. Functional Tests are generally depen-
dent on the vehicle manufacturer’s OBD strategy
and the PCM diagnostic architecture. Functional
tests require that the scan tool have the ability to
perform bi-directional communications with the
vehicle’s PCM. This means that the scan tool
must “talk” to the vehicle’s PCM, instead of just
“listening” to the incoming vehicle data stream.
Examples of functional tests are: Chrysler’s ac-
tuator/switch tests that allow you to review the
operation of a switch as you turn it on or off from
the driver’s seat, and turning the fuel pump on
and off. On a GM vehicle, a functional test is
placing the vehicle in Ground Mode to check the
PCM’s self-test diagnostics and the “Check En-
gine” lamp operation.
Ground: The return path for current to flow back
to its source (Usually the negative battery termi-
nal). It is also the reference point from which
voltage measurements are made (the connec-
tion place for the negative (-) test lead from a
voltmeter).
Inputs: Electrical signals running into the PCM.
These signals come from sensors, switches or
other electronic modules. They give the PCM
information about vehicle operation.
KOEO: Key On, Engine Off. A test mode where
the PCM is active and feeding data parameters,
but the engine is not running. Because the
engine is not running, some data parameters
may not be accurate or available in this mode. On
Ford vehicles, KOEO testing is the only way to
read memory codes stored in the PCM.
KOER: Key On, Engine Running. A test mode
where the PCM is active and feeding data param-
eters, and the engine is running. Since the
engine is running, most data parameters should
be available and accurate.
Knock: See “Detonation.”
Knock Sensor: This sensor is used to detect
engine detonation (or “knock”). When spark
knock occurs, the sensor emits a pulsing signal.
Depending on the vehicle, this signal either goes
to the PCM or a separate ESC (Electronic Spark
Control) module. Then the spark advance is
retarded until detonation stops. The sensor
contains a piezoelectric element and is threaded
into the engine block. Vibrating the element
generates the signal pulse. Special construction
27
makes the element sensitive only to engine
vibrations associated with detonation (“knock-
ing”).
MFI: Multi-Port Fuel Injection. See “MPFI” defini-
tion.
MIL: Malfunction Indicator Lamp. Also known as
a Check Engine Light or CEL.
Mode: A type of operating condition, such as “idle
mode” or “cruise mode.”
MPFI: Multi-Port Fuel Injection. A fuel injection
system using one (or more) injector(s) for each
cylinder. The injectors are mounted in the intake
manifold, and fired in groups rather than individu-
ally.
M/T: Manual transmission or manual transaxle.
NOx: Oxides of Nitrogen. A pollutant. The EGR
system injects exhaust gases into the intake
manifold to reduce these gases at the tailpipe.
On-Board Diagnostics (OBD): As vehicle manu-
facturers developed on-board diagnostics for
their service procedures and to meet EPA regu-
lations, the first phase of this computerization
was referred to as OBD. This technology started
in the late 1970’s and carried through to the early
1980’s. Most of these early systems were very
crude, especially when compared to today’s
OBD. Many required a manufacturer-specific tool
to read trouble codes and other computer infor-
mation. This technology used a feedback loop
system to monitor exhaust emissions and pro-
vided computer control of the vehicle’s fuel
system.
On-Board Diagnostics, Phase I (OBD-I): By
1985, the California Air Resources Board (CARB)
had called for more uniform diagnostic systems
to be used on vehicles sold in California. Com-
bined with federal exhaust emission regulations
enacted in the early 1990’s, CARB required that
all vehicles sold in California have an integrated
PCM structure that monitored all critical emis-
sions components. Manufacturers found that it
was simpler to incorporate this system into all their
vehicles built in the USA. In fact, by the end of
1986, most diagnostic procedures were uniform
within each manufacturer, providing an opportu-
nity for generic scan tools to come to market for
the home mechanic.
On-Board Diagnostics, Phase II (OBD-II): With
the passing of the 1990 Clean Air Act Amend-
ment, the EPA imposed more stringent require-
ments which include the addition of multiple
oxygen sensors, one before the catalytic con-
verter and one after to provide the PCM with
information on catalyst efficiency and condition.
There are also computer-controlled EGR, fuel
pressure regulators, and smart ignition systems.
In addition, OBD-II requires a common diagnostic
connector and location, as well as an industry-
standard data message, both defined by an
industry committee made up of engineers from
most major manufacturers and the SAE. Vehicle
manufacturers are required by law to provide at
least a minimum amount of data for emissions
programs to access the critical emissions data
available through OBD-II. OBD-II began to ap-
pear in vehicles in late 1994, and is required
equipment on all cars sold in the US after January
1, 1996.
Open (Circuit): A break in the continuity of a
circuit such that no current may flow through it.
Open Loop (O/L): This is when the control system
performs an action (expecting a certain result),
but has no way of verifying if the desired results
were achieved. Example: The PCM operates a
fuel injector expecting a certain amount of fuel to
be delivered (The PCM assumes everything in the
fuel system is performing properly). In open loop
operation, the PCM has no way of checking the
actual amount of fuel delivered. Thus, a faulty
fuel injector or incorrect fuel pressure can change
the amount of fuel delivered and the PCM would
not know it.
In general, a control system operates in open
loop mode only when there is no practical way to
monitor the results of an action. Example: Fuel
delivery during cold engine warm-up. The com-
puter runs in open loop mode because the
oxygen sensor is not hot enough to send a signal.
Without the sensor signal, the computer cannot
check the actual amount of fuel delivered.
O2S: Oxygen Sensor. The oxygen sensor is
threaded into the exhaust manifold, directly in the
stream of exhaust gases. The PCM uses the
sensor to “fine tune” fuel delivery. The sensor
generates a voltage of 0.6 to 1.1 volts when the
exhaust gas is rich (low oxygen content). The
voltage changes to 0.4 volts or less when the
exhaust gas is lean (high oxygen content). The
sensor only operates after it reaches a tempera-
ture of approximately 349°C (660°F).