Hitachi INVERTER J300 User Manual
Page 6
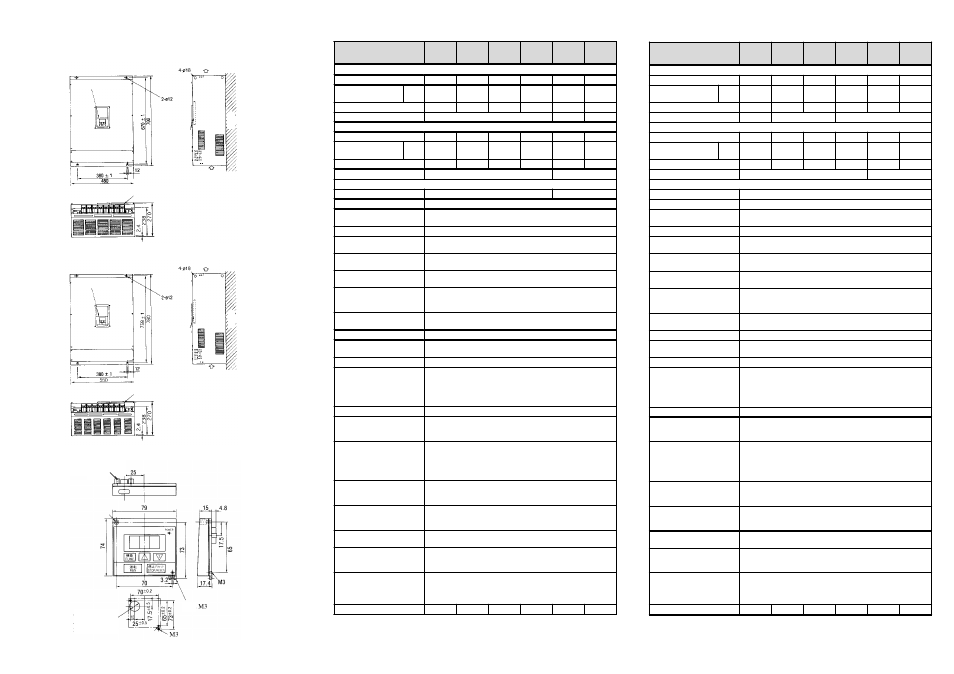
External dimensions and terminal positions part 2/2 (part 1/2 on previous page)
J300-
750 HFE4
900 HFE4
Air
Control
terminals
Main terminals
Wa
ll
Digital operator
Air
J300-1100 HFE4
Air
Control
terminals
Main terminals
Wa
ll
Digital operator
Air
Digital operator
OPE-J
Connector for
extension cable
Cutout for
connector
25mm
e.g.
T ec hn ic a l S pe ci f ic a t io ns
Inverter J 3 0 0
-
370
HFE4
450
HFE4
550
HFE4
750
HFE4
900
HFE4
1100
HFE4
Loads having constant torque
Maximum motor size in kW
37
45
55
75
90
110
Maximum motor
capacity in kVA
400V
52
62
76
103
122
150
Rated output current in A
75
90
110
149
176
217
Carrier frequency in kHz
2 – 10
2 – 6
2 – 3
Loads having quadratically rising torque
Maximum motor size in kW
45
55
75
90
110
132
Maximum motor
capacity in kVA
400V
61
75
101
122
150
180
Rated output current in A
88
108
146
176
217
260
Carrier frequency in kHz
2 – 4
2
General technical specifications
Protective structure
IP00
Rated input voltage
Three phase 380 ~ 460V +/-10%, 50/60Hz +/-5%
Rated output voltage
Three phase 0 .. 380 ~ 460VAC
(Corresponds to input voltage)
Output frequency range
0,1 ~ 400Hz
Operating principle
Sensorless Vector Control (SLV), PWM sine coded.
Power amplifier: IGBT/IPM
Overload current capacity
150% during 60s (constant torque)
115% during 30s (quadratically rising torque)
Frequency accuracy
(at 25°C +/-10°C)
Digital command: +/-0.01% of the maximum frequency
Analog command: +/-0.1% of the maximum frequency
V/F characteristics
V/F curves with constant and reduced torque;
vector control without feedback;
vector control with feedback (optional)
Autotuning
Automatic adaption to motor characteristics to make
best use of the motor driven
AVR function
Automatic Voltage Regulation usable
Acceleration/Deceleration
2 times settable between 0.01 and 3000s (using digital remote
control); linear, S-curve, U-curve
Starting torque
150% at 1Hz (constant torque)
Braking resistor
Models J300-055HFE4 and J300-075HFE4 have a built-in braking
resistor. Braking torque approx. 50% to 60% of the rated torque
using the built-in braking resistor (the rest of the J300- models have
a braking torque of approx. 10% to 15% of the rated torque using
braking with feedback to capacitor).
DC braking
Variable operating frequency, time, and braking force.
Frequency command
Digital command using the built-in digital operator keys.
Analog 0–5V and 0–10V (input impedance 30kOhm) and
4–20mA (input impedance 250Ohm); optional digital input
Intelligent digital inputs
8 inputs configurable as: Forward run, Reverse run, Free run mode,
Reset, Jog, 7 multistage speed settings, Ext. DC braking, 2. Setting,
2. Stage accel/decel, External alarm, USP function, Software lock,
frequency command from analog input O or OI, Motor poten-
tiometer, Motor free run, Factory setting, etc.
Outputs
Analog output current, output frequency, and torque.
Transistor output with signals for frequency arrival, motor
running, torque alarm; Alarm output
Other functions
Optimized acceleration and deceleration times using fuzzy logic,
engergy saving mode, electronic thermal, jump frequency,
upper/lower limits, PID control, etc.
Protective functions
Overcurrent, overvoltage, undervoltage, overload, excessive
temperature, ground fault, braking resistor overload, etc.
Directives and standards
CE-EMC directive in conjunction with optional radio noise
filter and installation according to installation guidelines;
CE low voltage directive
Operating environment
Ambient temperature: -10~50°C with constant torque
and -10~40°C with quadratically rising torque.
Humidity: 20-90% RH (non condensing); Installation altitude:
1000m or less
Overall weight (approx.)
36
46
46
70
70
80
T ec hn ic a l S pe ci f ic a t io n s
Inverter J 3 0 0
-
055
HFE4
075
HFE4
110
HFE4
150
HFE4
220
HFE4
300
HFE4
Loads having constant torque
Maximum motor size in kW
5.5
7.5
11
15
22
30
Maximum motor
capacity in kVA
400V
9.0
11
16
22
33
40
Rated output current in A
13
16
23
32
48
58
Carrier frequency in kHz
2 – 16
2 – 12
2 – 10
Loads having quadratically rising torque
Maximum motor size in kW
7.5
11
15
22
30
37
Maximum motor
capacity in kVA
400V
11
16
22
30
41
51
Rated output current in A
16
23
32
44
59
74
Carrier frequency in kHz
2 – 8
2 – 4
General technical specifications
Protective structure
IP20
IP00
Rated input voltage
Three phase 380 ~ 460V +/-10%, 50/60Hz +/-5%
Rated output voltage
Three phase 0 .. 380 ~ 460VAC
(Corresponds to input voltage)
Output frequency range
0,1 ~ 400Hz
Operating principle
Sensorless Vector Control (SLV), PWM sine coded.
Power amplifier: IGBT/IPM
Overload current capacity
150% during 60s (constant torque)
115% during 30s (quadratically rising torque)
Frequency accuracy
(at 25°C +/-10°C)
Digital command: +/-0.01% of the maximum frequency
Analog command: +/-0.1% of the maximum frequency
V/F characteristics
V/F curves with constant and reduced torque;
vector control without feedback;
vector control with feedback (optional)
Autotuning
Automatic adaption to motor characteristics to make
best use of the motor driven
AVR function
Automatic Voltage Regulation usable
Acceleration/Deceleration
2 times settable between 0.01 and 3000s (using digital remote
control); linear, S-curve, U-curve
Starting torque
150% at 1Hz (constant torque)
Braking resistor
Models J300-055HFE4 and J300-075HFE4 have a built-in braking
resistor. Braking torque approx. 50% to 60% of the rated torque
using the built-in braking resistor (the rest of the J300- models have
a braking torque of approx. 10% to 15% of the rated torque using
braking with feedback to capacitor).
DC braking
Variable operating frequency, time, and braking force.
Frequency command
Digital command using the built-in digital operator keys.
Analog 0–5V and 0–10V (input impedance 30kOhm) and
4–20mA (input impedance 250Ohm); optional digital input
Intelligent digital inputs
8 inputs configurable as: Forward run, Reverse run, Free run mode,
Reset, Jog, 7 multistage speed settings, Ext. DC braking, 2. Setting,
2. Stage accel/decel, External alarm, USP function, Software lock,
frequency command from analog input O or OI, Motor poten-
tiometer, Motor free run, Factory setting, etc.
Outputs
Analog output current, output frequency, and torque.
Transistor output with signals for frequency arrival, motor
running, torque alarm; Alarm output
Other functions
Optimized acceleration and deceleration times using fuzzy logic,
engergy saving mode, electronic thermal, jump frequency,
upper/lower limits, PID control, etc.
Protective functions
Overcurrent, overvoltage, undervoltage, overload, excessive
temperature, ground fault, braking resistor overload, etc.
Directives and standards
CE-EMC directive in conjunction with optional radio noise
filter and installation according to installation guidelines;
CE low voltage directive
Operating environment
Ambient temperature: -10~50°C with constant torque
and -10~40°C with quadratically rising torque.
Humidity: 20-90% RH (non condensing); Installation altitude:
1000m or less
Overall weight (approx.)
7.5
7.5
13
13
21
36
12
13
14