Hubbell Electric Cable Reels TMR Series User Manual
Installation and maintenance instructions, Tmr series electric cable reels
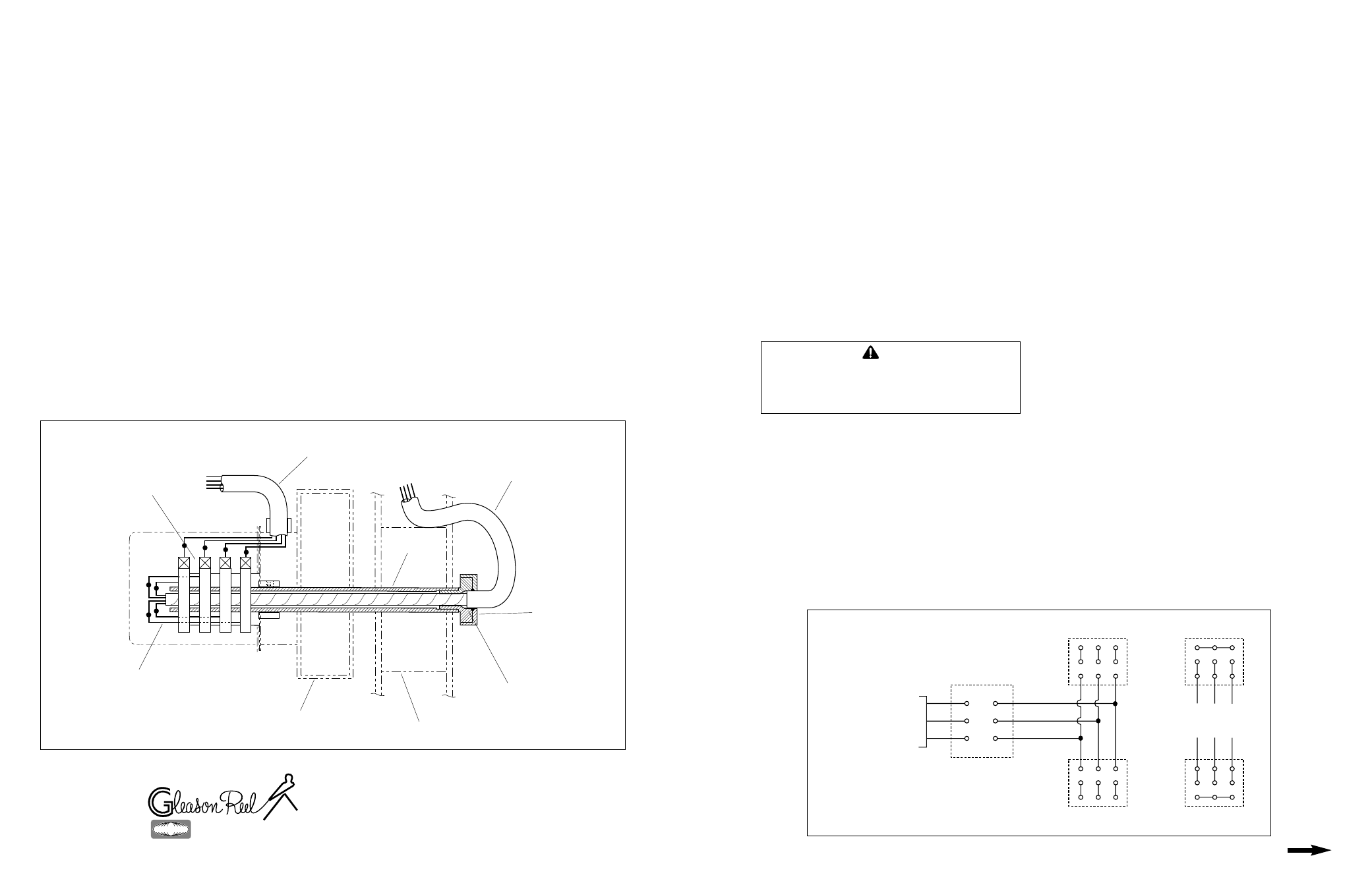
CABLE REMOVAL
Use the following procedure to remove worn or damaged cable
from reel prior to installation of new cable.
1. Move machine serviced by reel to a position closest to
reel.
2. Turn off all electric power.
3. Lock spool to prevent turning using either a spool lock
mechanism or by tying off.
4. Disconnect cable from machine junction box.
5. Remove cable from spool. Loosen cable connector (Item 11
on parts list) and disconnect conductors from slip ring.
6. Install new cable following instruction below.
CABLE INSTALLATION
Use the following procedure to replace cable or if reel was
ordered without cable. Refer to CABLE INSTALLATION
REFERENCE DRAWING, below.
1. Unspool new cable from shipping spool and lay out
to eliminate twist.
NOTE: This step is not essential, but will aid in winding
operation of the reel and prolong cable life.
2. Feed one end of the cable through cable connector on
the main shaft inside the spool and into the slip ring side.
(See drawing below).
NOTE: This may require that jacket of cable be stripped
to allow conductors to pass through shaft.
3. Connect individual conductors to appropriate rings on
collector using crimp fitting or similar connection method.
4. Tighten cable connector and U-bolt provided on
drum wrapper segments. Do not over-tighten.
5. Wind the cable onto the reel spool by hand rotating
spool.
6. Connect free end of cable to machine junction box.
COLLECTOR REPLACEMENT
1. Turn off all power to reel.
2. Remove collector cover and gasket.
3. Disconnect electric leads to and from collector.
4. Remove drive stud bolt from bearing housing.
5. Remove plug plug from hole in side of housing. Insert
long 1/8” Allen wrench through hole and loosen two set
screws in collector locking collar Set screws are at 90
O
to one another..
NOTE: Older reels may have lock screws which must be
removed to reach set screws holding collector to shaft.
6. Slide collector off shaft.
7. Install new collector by reversing above steps.
Printed in USA
Bulletin No. 053151.a
®
HUBBELL
®
A Hubbell Company
GLEASON REEL CORP.
P.O. Box 26 • 600 South Clark St
Mayville, WI 53050–0026
Phone 920–387–4120
Fax 920–387–4189
Cable
(Output)
Connect leads
to collector
NOTE:
Strip cable to inside
of gland. Wrap
leads with electrical
tape thru shaft.
Spool
Frame/Gear Case
Collector
Reel
Shaft
Cable Gland
Thread gland into
shaft. Thread cable
thru gland and shaft.
Tighten gland cover
to secure cable.
Cable
(Input)
CABLE INSTALLATION REFERENCE DRAWING
CONTINUED ON BACK PAGE
INSTALLATION and MAINTENANCE INSTRUCTIONS
TMR SERIES ELECTRIC CABLE REELS
DESCRIPTION
The TMR series reel is designed to automatically lift and
retrieve electric cable. The reel incorporates a rotating hollow
shaft with spool mounted outboard on one end and collector
assembly on the opposite end. The main shaft, rotating on
two flange block bearings, is driven by an electric torque motor
through a chain drive. The torque motor has an electronically
released break holding the spool stationary when the reel is
not in use.
INSTALLATION
1. Thoroughly inspect reel upon receipt for damage that may
have been caused in shipping.
2. Mount reel with the main shaft horizontal and level and
with the spool centerline in line with the cable tray. Mount
at recommended height so that proper distance from the
center of the spool to the cable tray is maintained.
3. Remove collector cover. Connect conduit to line entrance
of collector housing and connect wires to brushes of
collector assembly. Brush terminals are number coded.
Be careful that incoming wires do not put strain on brush
terminals and cause brush misalignment. Replace
collector cover.
4. Connect motor to electric line of proper specification as
stamped on motor nameplate. Refer to wiring diagram
(below, in terminal box or on name plates. 3-lead
polyphase and 2-lead single phase do not require
diagram). Provide suitable overload protection based on
full load ampere rating shown on nameplate as
recommended by control manufacturer. Protect wiring circuit
with proper fuses selected according to local codes.
Exceeding designed lift distance may lead
to poor cable spooling and
erratic operation because the electric motor
will have insufficient torque.
CAUTION
OPERATION
The reel is activated when power is supplied to the torque
motor through the main starting control of the equipment.
Care should be taken to see that all electrical connections are
made before power is turned on to the collector ring and
torque motor. All nuts and bolts should be checked to see that
they are tight. Check to make sure collector ring brushes are
aligned on rings.
MAINTENANCE
GENERAL LUBRICATION: All bearings provided with grease
fittings are lubricated at the factory before shipment. They
should be regreased periodically depending on the running
time of the reel, more often if used in dusty conditions. Parts
with bearing assemblies not provided with grease fittings are
equipped with sealed bearings and do not require lubrication.
CHAIN CASE: Every three months, remove cover from chain
case, check chain tension, and lubricate chain using a lithium
based heavy duty chain lubricant.
TORQUE MOTOR GEAR REDUCER: See section 5.2.2 of
the enclosed brake motor operation instructions for grease
lubrication. This gear reducer is filled with grease when used
with 600 RPM torque motor.
TORQUE MOTOR: Reel is equipped with a Demag torque
motor. See enclosed brake motor operation instructions.
INSPECTION: Every six months inspect entire reel to see that
all nuts, bolt, screws, and set screws are in place and tight and
that no parts show undue wear. Yearly (more often depending
on duty cycle), check brushes on collector rings. Replace
brushes when worn to the shunt
SUPPLY VOLTAGE
230V or 460V
3 PHASE 60Hz
REEL MOTOR
CONTROL PANEL
(Supplied by customer
NOTE: Reel start/stop circuit should be wired into main machine
power master switch (not to machine travel drive motors). Frequent
starting and stopping of torque motor is not recommended.
Torque motor should be wired to wind cable only. Torque motor
compensates for direction change when cable is unwound.
NOTE: Be sure blower motor is also wired up with motor.
TORQUE MOTOR
3/60Hz/460V
BLOWER
3/60Hz/460V
BLOWER
3/60Hz/230V
TORQUE MOTOR
3/60Hz/230V
L3
L2
L1
T3
T2
T1
T3
1
2
3
1
2
3
7
8
9
7
8
9
4
5
6
4
5
6
1
2
3
1
2
3
7
8
9
7
8
9
4
5
6
4
5
6
T2
T1
WIRING DIAGRAM