JBL Synthesis K2 S9900 User Manual
Page 16
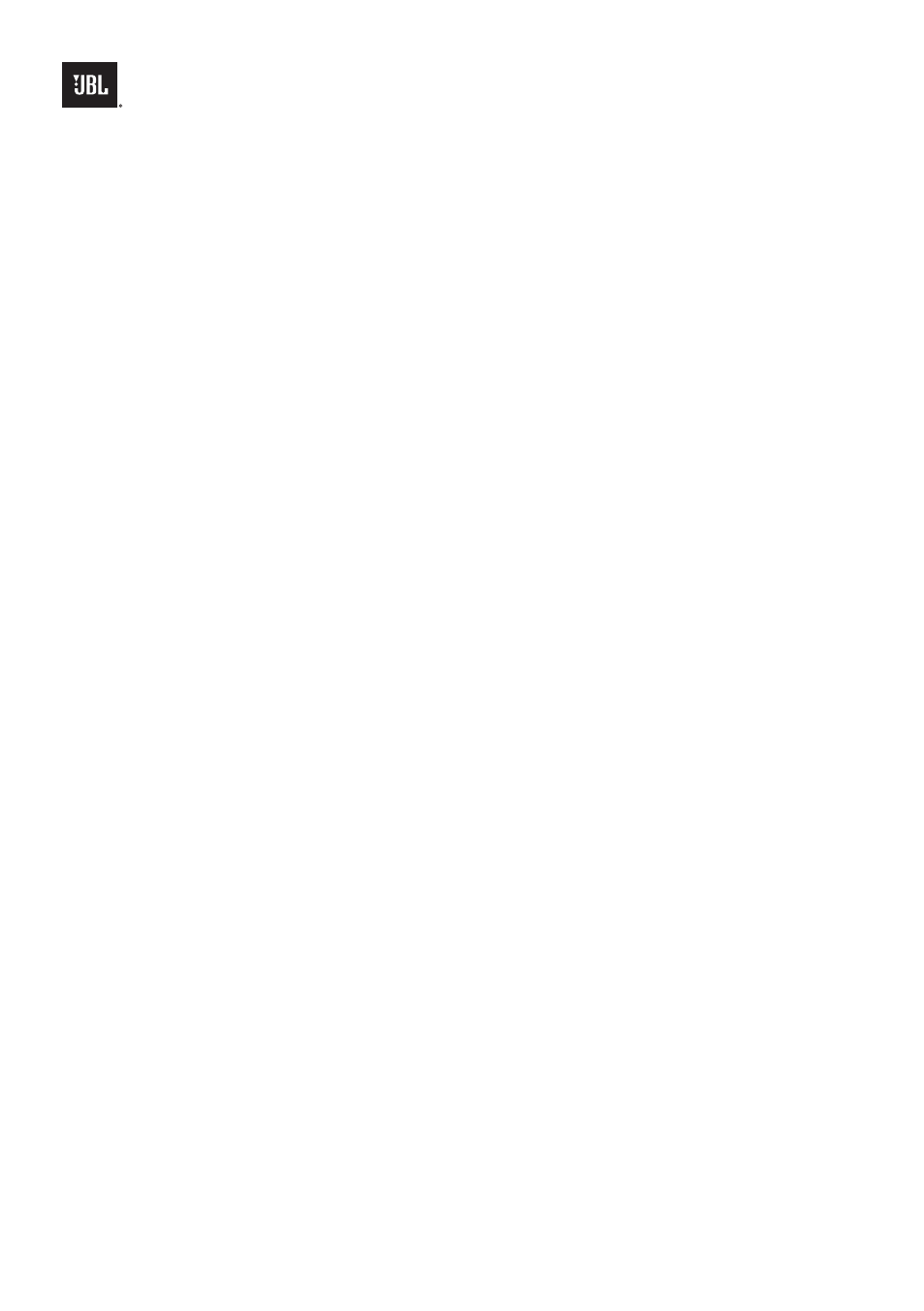
16
A high-purity copper sleeve is used for the polepiece. This greatly improves
the electrical conductivity of the copper sleeve for lower coil inductance and
thus greater high-frequency output at 15kHz and above. The copper-sleeved
pole quickly wicks away heat generated by the coil, thereby contributing to
a reduction in dynamic power compression. To compensate for the higher
resistance caused by the use of a copper-sleeved polepiece, a large magnet
area has been used, in conjunction with special high-grade and high-temperature-
grade neodymium.
The phasing plug is a traditional JBL rapid-flare, coherent-wave four-slot design.
This coherent-wave design shapes the wave output, producing a truly coincident
wave front as the sound enters the Bi-Radial horn. The diaphragm is formed
of magnesium-alloy foil and is the first JBL large-format 100mm compression
driver to use this special material. Magnesium alloy is essentially 95 percent
pure magnesium with small percentages of aluminum, zinc and other alloys
added to improve characteristics such as diaphragm forming, fatigue strength,
corrosive and acoustic properties. A proprietary thermal process is used to
form the thin sheets of magnesium alloy into the 100mm diaphragm shape
of exacting dimensions. This new process even enables the integrated JBL
Diamond surround to be formed as one piece with the dome. Forming the
diaphragms out of sheets of this magnesium-alloy foil yields greater reliability
and resistance against fatigue and corrosive failures than diaphragms formed
with 100 percent pure magnesium or aluminum.
Magnesium has very low density, slightly lower than even that of beryllium.
With such a low density, the thickness of the magnesium-alloy diaphragm could
be greatly increased while still maintaining an equivalent diaphragm mass of
approximately 3.4 grams, similar to previous designs using aluminum and
titanium. Based on this, the new magnesium-alloy diaphragm was increased
to 130 micron, about 1.7 times thicker than the standard 76-micron-thick
aluminum diaphragm. When compared to the titanium diaphragm used in the
original K2 S9500 and M9500 systems, this new magnesium-alloy diaphragm is
2.5 times thicker. This is beneficial because a thicker diaphragm creates a much
stiffer diaphragm, which pushes pistonic behavior to higher frequencies than
current aluminum or titanium diaphragms (given the same moving mass).
Better pistonic behavior means less diaphragm modal breakup at the critical
mid-band frequencies, and so the upper frequency response will be smoother
with minimal distortion spikes. The effects of this will be less distortion, and
improved and extended frequency response (Fig. 5).