Kemppi Master S 400 User Manual
Page 12
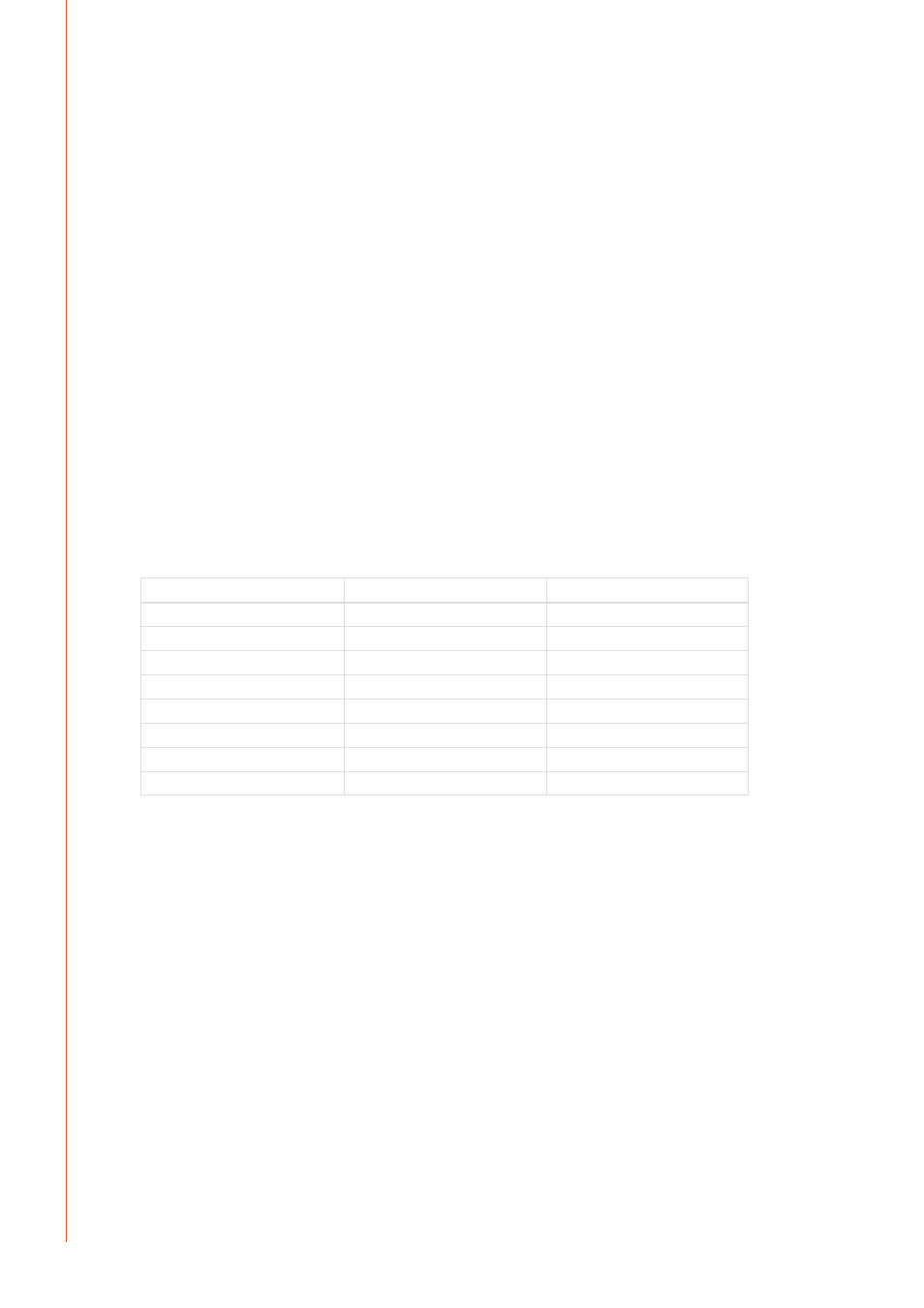
EN
Site your equipment in a suitable location, ensuring there is adequate cable length to
complete the weld pass. Before you start welding, ensure you are comfortably positioned in
front of the work piece, and that you are well balanced with your weight equally distributed.
Ensure that the power source current setting is correct for the electrode size selected. Draw
the welding face shield over your eyes. (Electronic welding face shields like Kemppi Beta
90X allow you to see the welding start point more accurately and better concentrate on the
welding process. This reduces the possibility of arc flash.)
NOTE!
Ensure that others in the welding area are aware that you're going to weld.
To establish the arc, scratch the electrode on the surface of the work piece.
As the arc starts, move the welding electrode at a pulling angle. The boundary of the slag
formed is visible after the molten weld. It must be behind the molten weld. The distance of
the slag boundary from the molten weld can be adjusted with the welding current and the
angle of the electrode. Throughout the welding, concentrate on the length of the arc and
keep it as short as possible. The length of the arc increases easily as the electrode decreases in
length during the welding. End welding by moving the welding electrode slightly back to the
completed weld and then lifting the electrode straight away from the work piece.
Your completed weld bead should be straight and of even width and bead height, consistent
in its appearance. Travel too slowly during welding and the weld pool will get too big and may
burn through the weld piece, too fast and the resulting weld will be too small and may have
slag entrapments and/or poor strength. After welding, the solidified slag on the weld surface
should easily remove with a chipping hammer. Ensure you wear eye and face protection when
removing the slag from the weld surface.
3.3.4 Electrode welding parameter table
Electrode diameter (mm)
Rutile E6013 (A)
Basic E7018 (A)
1.6
30–60
30–55
2.0
50–70
50–80
2.5
60–100
80–110
3.25
80–150
90–140
4.0
100–200
125–210
5.0
150–290
200–260
6.0
200–385
220–340
7.0
280–410
3.3.5 Arc force
Adjusting arc force by turning the ArcForce knob will affect the roughness of the arc. Factory
setting for all electrode types is zero. If the value is set to -9...-1 the arc is softened and the
amount of spatter decreases when welding at the upper end of the recommended current
range of the electrode. If the value is set to 1...9 the arc gets rougher.
The value is shown on the right display during the adjustment.
3.3.6 Hot start
HotStart increases the current for the arc ignition momentarily. With very thin work pieces hot
start is generally not needed (depends on the electrode type).
The hot start value is selected between 0 and 10. Zero shuts HotStart off (no HotStart) and 10
sets it to HotStartMax. Factory setting is 5.
The value is shown on the right display during the adjustment.
Master S 400, 500
10