JIMS 2456-1 User Manual
Page 2
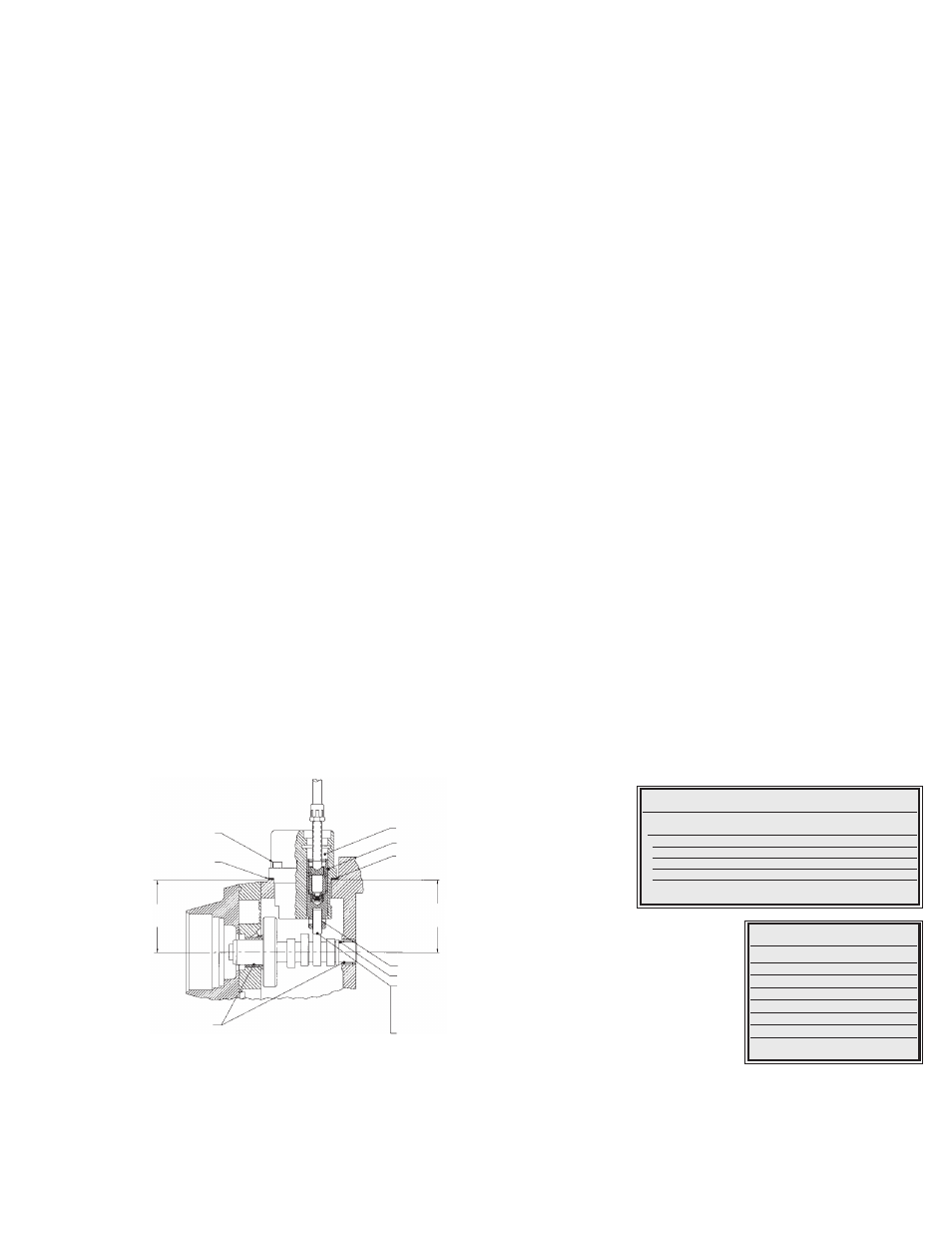
FOUR POSSIBLE REASONS THAT MAY KEEP NEW HYDRAULIC UNITS FROM WORKING PROPERLY
IMPROPER FIT • MECHANICAL • CONTAMINATION OF OIL SUPPLY • LOW OIL SUPPLY
1. IMPROPER FIT
a) Not likely, each unit goes through (2) two tests.
b) First the fit is checked twice, .0015” to .0002”.
c) Second, a hydraulic bleed down test is performed first dry, then with 5 weight oil.
2. MECHANICAL
a) Not adjusted properly, readjust per instruction sheet. For 18523-86, 18526-89 and 18522-53PG, the hydraulic unit itself needs to be at
.100 ± .010 below snap ring. For 1029-53 kit the hydraulic unit itself needs to be .050 ± .010 below the snap ring. Some shovel models
from 1978-1980 have tappet blocks with oil drain holes to low. If running a higher lift cam then stock, and sometime even stock, these
blocks will allow oil pressure to bleed off from the tappets, this is most common in the front tappet block.
b) A bent pushrod, loose valve guides, broken valve spring, valve hitting piston, valve hitting valve, rocker bushing loose, rocker tip wear at
valve stem, and lifter roller hitting tappet block. All will cause a noisy valve train.
c) Gear lash: if you did not change the cam at the time you installed new hydraulic units and had no gear lash, but a slight whine motor
when motor was cold, it is safe to say you are OK in this area.
d) Hydraulic valve spring broke, is not allowing valve to seal. We have not seen this on any JIMS
®
hydraulic units.
e) If this is the case the hydraulic unit will not hold oil pressure, to check this hold pushrod with your hand (with lifter on the heel of cam valve
shout) push down on pushrod. Hydraulic unit will feel spongy. Do not mistake this for no oil getting to tappet. If all tappets are spongy this
is no oil. If just one tappet is spongy and has been readjusted, and still will not pump up, replace tappet.
3. CONTAMINATION OF OIL
a) Hydraulic unit may work for a minute and then become noisy, most of the time it is more then one hydraulic unit that will be contaminated
to the point of being stuck in the downward position.
b) Readjust per instruction sheet. If hydraulic unit will not come back up to the top of snap ring, replace hydraulic unit and wash out the entire
oil system.
4. OIL PRESSURE AT NORMAL OPERATING TEMPERATURE, AT ABOUT 2,000 R.P.M., SHOULD BE 12-35 P.S.I..
a) Check lifter filter screen. ( Big Twin )
b) Make sure your getting oil to the lifters. Install oil pressure gauge for top end oil.
c) Lifter to tappet block clearance is best at .0007”-.0012”.
d) Lifters work best with 20w-50w motorcycle oil.
e) If lifters are quiet when cold or low r.p.m., and become noisy as r.p.m. is increased, there is not enough oil pressure or to much clearance
from lifter to block bore. (see “C”)
f) To isolate a possible noisy hydraulic lifter start with a cool motor and the lifter you think is making the noise. With that lifter on the heel of
cam, valve shut, adjust pushrod so lifter unit is all the way compressed down ( very important ) this adjustment will make the pushrod tight
which will bleed down the hydraulic lifter. It will sometimes take (5) five minutes, or longer, to bleed down. Do not rotate engine while
pushrods are tight. Go to the point where pushrod will spin with your fingers. Adjust down a little more until pushrod becomes tight ( you
can just barely turn with your fingers ). Start bike, if it is quiet then you have found the lifter that was not working properly. If it’s still noisy
continue with the next lifter until you have located the the noisy one. Readjust per instruction sheet, or replace lifter.
PROPER TORQUE OF SCREWS
FLATNESS OF GASKET
CLEARANCE BETWEEN
LIFTER AND BORE
SQUARENESS OF BORES
TO LIFTER BLOCK FACE
SQUARENESS OF TAPPET
BLOCK BORE TO CAM LOBE
SQUARENESS OF AXLE TO ROLLER
CAM SHAFT END PLAY
PARALLELISM OF ROLLER TO CAM LOBE
MAINTAINING COMPLETE SURFACE CONTACT
OPTIMUM CONDITION WITH ROLLER MAKING
FULL CONTACT ON CAM LOBE RESULTS FROM
MAINTAINING CLOSE TOLERANCES
MAINTAINING PARALLELISM
FROM THE DECK TO THE CENTER
LINE OF THE CAM (INSIDE)
MAINTAINING
PARALLELISM
(OUTSIDE)
CENTERLINE OF CAM BUSHING
IN CAM COVER IS COAXIAL
TO CAM ROLLER BEARING IN CASE
➋
➌
➋
➎
➒
➐
➐
➎
➍
➑
➏
The following is sometimes mistaken for noisy tappets:
A. The most common being the clearance between cam gear and pinion gear (referred to as gear lash). If you did not change the cam at the
time of installing this kit and had no gear lash but a slight whine when motor was cold it is safe to say you are OK in this area.
B. Rocker arm end play .004” to .010” is good.
C. Oil pressure at normal operating temperature about 2000 r.p.m. should be 12-35 p.s.i. on Big Twin models, and 10-17 p.s.i at 2500
r.p.m. on XL models.
D. Check valve to guide clearance.
“From the Track... To the Street!”
555 Dawson Drive, Camarillo, CA 93012 • Phone 805-482-6913 • Fax 805-482-7422
Pushrod Adjustments
Distance
Distance
Threads
Wrench
Total Travel
per turn
per flat
per inch
Flats
Distance
.0417
.0069
24
15
.1042”
.0357
.0059
28
17
.1011”
.0313
.0052
32
18
.0937”
.025
.0042
40
24
.100”
.0192
.0032
52
30
.0962”
Popular Pushrods
JIMS
®
32
Slim-Jims
Andrews
28
Andrews
32
Crane
24
Time Savers
Crane
32
H.D.
32
S & S
32
Rivera
40
Taper Lite
❶
REV E
9-08
No.2272-IS
2