Flowserve ESP3 Electronic Servo Positioner User Manual
Page 4
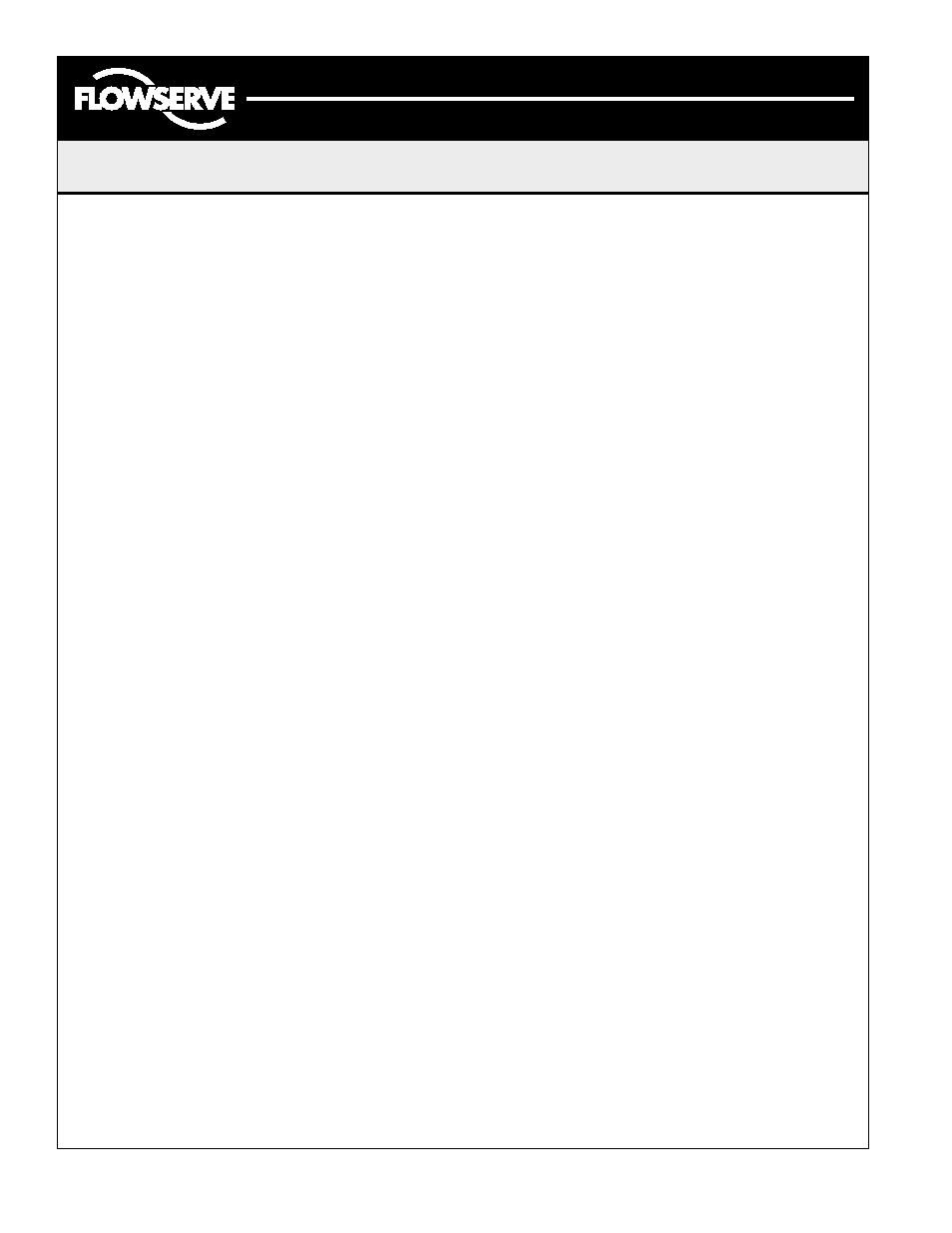
© 2001, Flowserve Corporation, Provo, Utah
3-Position Control/Dribble Control
SR Limit Switch Method
Flowserve Corporation
765 South 100 East
Phone: 801 373 3028
Flow Control Division
Provo, Utah 84606
Facsimile: 801 489 2228
Automation Business Unit
www.flowserve.com
Email: [email protected]
Automax Valve Automation Systems
Installation, Operation and Maintenance Instructions
Trouble Shooting
1.
Actuator does not respond to the input signal.
A.
Verify the proper input configuration and signal polarity
connections. Measure voltage from test point ‘D’ to test
point ‘G’ should be in the range 1-5 Vdc.
Note: Signal
input circuits have reverse polarity protection, but will
not respond to reverse polarity signals.
B.
Verify the proper power connections. Refer to the
schematic on page 3.
2.
Actuator does not travel when CW or CCW LED is lighted.
A.
The calibration switch SW1 should be to the right in the
RUN position.
B.
Check the safety overtravel cams and overtravel
switches, and adjust as needed (see note 3).
C.
If actuator exceeds full CW or CCW positions, check
the feedback potentiometer voltage (see note 4).
3.
Safety overtravel switches need adjustment.
Note: On
valves with mechanical stops, the safety overtravel
switches
must be set so that the motor will disconnect prior
to hitting the mechanical valve stops.
A.
Disconnect wires from terminal block TB3 on ESP3
drive actuator CW until approx. 5 degrees past the
standard full CW position by applying 115Vac power to
the black and white motor leads or by using a wrench
to turn the manual override shaft. Adjust CW cam until
switch trips.
5.
Actuator is oscillating or is not responsive to
small input changes.
A.
Drive actuator to mid position and turn DB CCW
until both LEDs energize then immediately turn
CW until both LEDs de-energize. Turn adjustment
CW an additional 1/4 turn and operate actuator
over full range in small increments to check
operation. Voltage from test point ‘B’ to ‘G’ should
measure approximately 0.10Vdc.
B.
In high temperature and/or high cycle environments,
the thermal protection circuit in the drive
motor may be activated, causing the motor to
shut down until it cools. Reduce environment
temperature and/or cycle frequency.
6.
There is difficulty calibrating the actuator for the correct
range of operation.
A.
The zero ‘Z’ and span ‘S’ pots are 30 turn pots,
protected from overtravel. Turn both pots CW
until you hear clicking. Then turn them back CCW
15 turns to the center of their ranges. Recalibrate
starting from step 3 on page 1.
7.
Special precautions for operating the ESP3.
A.
It is always necessary to limit actuator from
repeated safety overtravel switch trippage.
B.
Always remove AC power to actuator prior to
removing input signal and apply signal prior to AC
power to actuator.
8.
Remote mounting of ESP3 card, control signal causes
inaccurate control, or long lines to transmitter cause
inaccurate control/output readings.
A.
Long input/output wire lines may add resistance
which may affect performance characteristics.
Use connecting wires having less than 10 ohms
of resistance.
B.
All signal carrying lines should be shielded,
especially if power lines are run in the same conduit.
Technical Assistance
If technical assistance is required, please have the following
information ready before calling:
A.
Actuator model number.
B.
Actuator serial number.
C.
Actuator sales order number.
D. Input signal configuration being used.
B.
While setting CW safety overtravel switch, ensure a
voltage between 0.20Vdc and 0.53Vdc is measured from
test point ‘A’ to test point ‘G’ when switch is tripped.
Otherwise see note 4 in this section.
C.
Drive the actuator CCW until approximately 5 degrees past
the standard full CCW position by applying 115Vac power
to the red and white motor leads. Adjust CCW cam until
switch trips.
4.
With the actuator in full CW position, the feedback potentiometer
voltage should read approximately 0.75Vdc from test point ‘A’ to
test point ‘G’. If the feedback pot is not set correctly, the “dead
spot” at the end of the pot’s rotation may cause over/under
travel or oscillations.
A.
With the actuator in the full CW position, move the switch
SW1 to the calibrate (left) position.
B.
Loosen potentiometer drive gear and rotate potentiometer
until approximately 0.75Vdc is measured between test
points ‘A’ and ‘G’, and then retighten drive gear.
C.
Move calibration switch SW1 to the run (right) position,
and recalibrate ESP3 zero and span adjustments,
starting with Step 3 on page 1.
LMP0003-1
(AUTO-42)
04/01
Page 4 of 4