Flowserve Supplement 2 75 DeviceNet PLC User Manual
Page 3
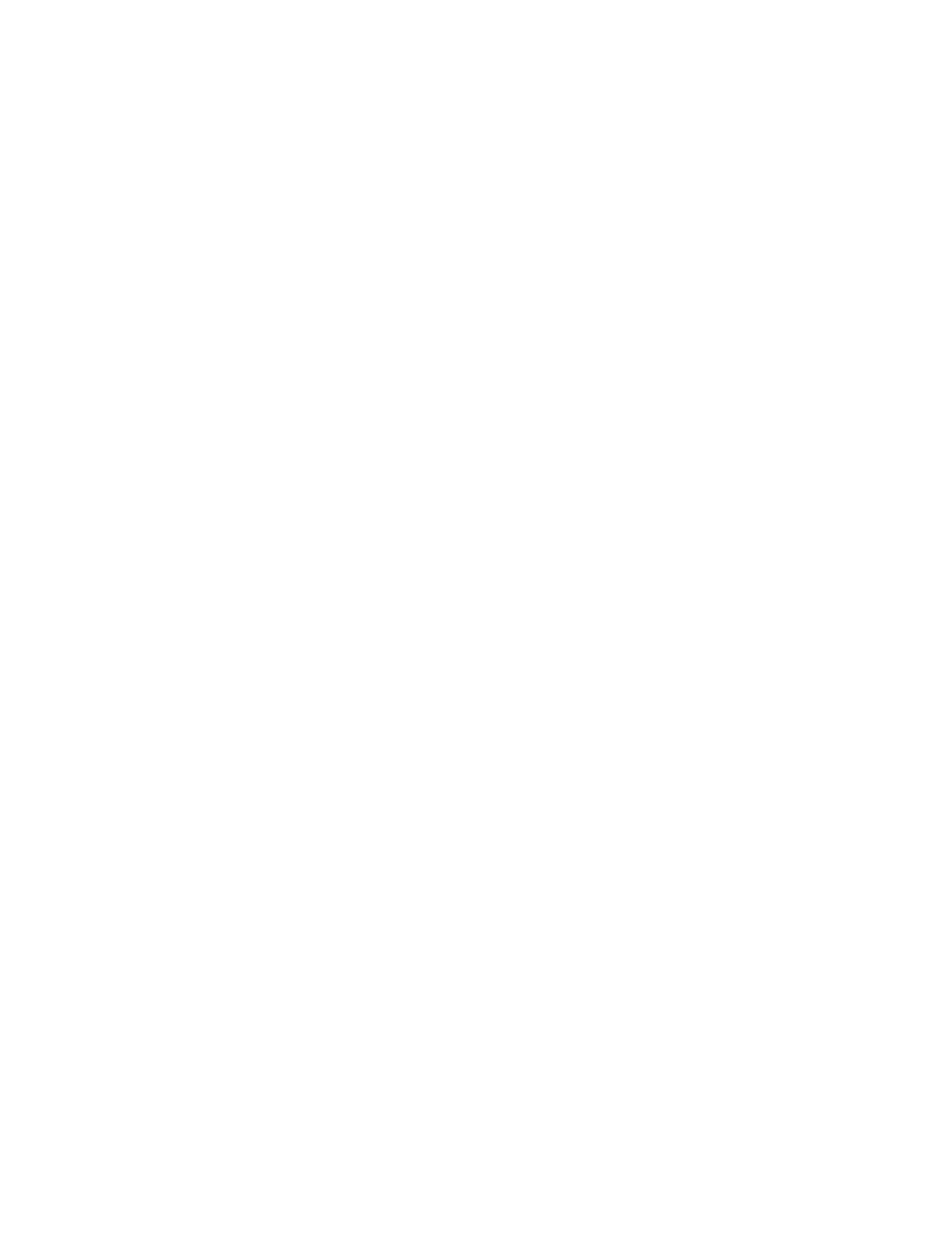
FCD WCAIM2062-00
Supplement 2: 75 DeviceNet PLC
3
14. In this example, with the scanner located in slot 4 the addresses
of I/O data in the PLC are as follows:
PLC Input Table: 11 bytes of data (output data from the slave)
BYTE-I
1:4.0 (word-O-not used)
1:4.1/0 Bit 0 Actuator Closed CW Switch
1:4.1/1 Bit 1 Actuator Open CCW Switch
1:4.1/2 Bit 2 Not used
1:4.1/3-Bit 3 Actuator CCW Relay (Coil 1) Continuity
1:4.1/4 Bit 4 Actuator CW Relay (Coil 2) Continuity
1:4.1 Bits 5-7 Not used
BYTES-2,3,4,5
1:4.1/Bit 8 to 1:4.3/Bit 7 Maintenance Counter Binary
Format
BYTES-6,7,8,9
1:4.3/Bit 8 to 1:4.5/Bit 7 Cumulative Counter Binary
Format
BYTE-10
Not used
BYTE-11
Not used
PLC Output Table: 1 byte of data (input data to the slave)
0:4.0/0- WORD-0/Bit 0 Establishes the operating mode of
the scanner
Bit 0 =1 Scanner maps I/O from the slaves. This Bit has to
be on for the outputs to be under PLC proqram control.
Bit 0 =0 Scanner stops mapping output data to the slaves.
Input data is still returned from the slaves. Outputs on the
network are not under PLC program control.
a
CAUTION: The PLC/Process Controller logic should never
set bits 5 and 6 on (1) at the same time in output word 1.
These bits control actuator CCW & CW rotation. Damage to
the relay interface module and motors will result if these bits
are set on (1) simultaneously. The output word 1 corresponds
to an actuator at Address 1.
O:4.1/0 Bits 0,1,2,3,4 Not Used
O:4.1/5 Bit 5 CCW Relay (Coil 1) Actuator goes in CCW direction
when =1 and stays in position when =0.
O:4.1/6 Bit 6 CW Relay (Coil 2) Actuator goes in CW direction
when =1 and stays in position when =0.
O:4.1/7 Bit 7 Resets Maintenance counter when =1.