Spring-return actuator, Worcester controls – Flowserve 10 ACCESS I 39 Actuators with DeviceNet Interface User Manual
Page 10
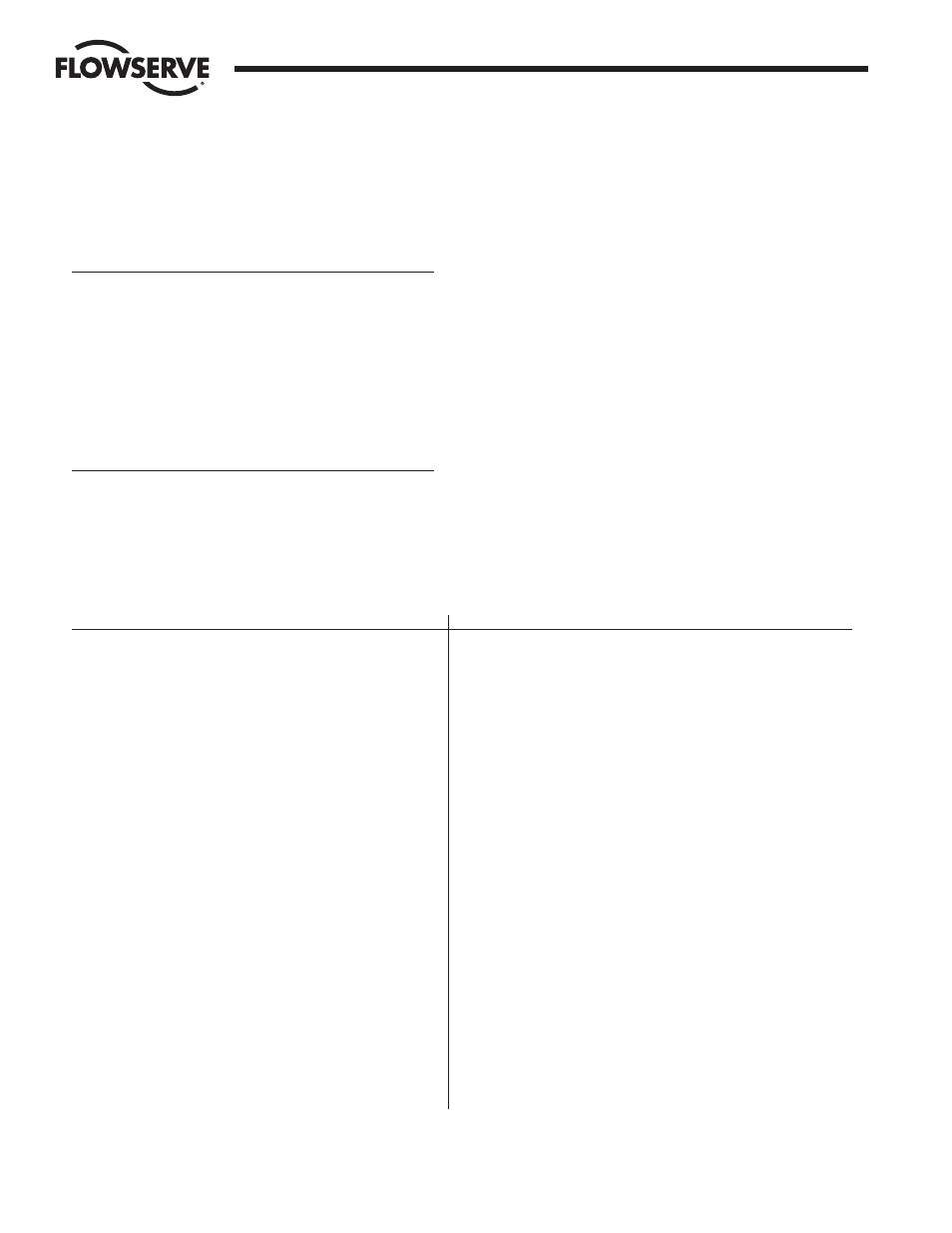
10
10, 15, 20 ACCESS I 39 Actuators with DeviceNet Interface
WCAIM2019
Flow Control Division
Worcester Controls
SPRING-RETURN ACTUATOR
1. IMPORTANT:
When less than the standard number of springs are used in each
end cap, these springs should be positioned according to the air
supply figures below.
Size 10–20
70 psi - 8 springs - 4 per end cap.
Remove center spring.
60 psi - 8 springs - 4 per end cap.
Remove center spring.
50 psi - 6 springs - 3 per end cap.
Use three on a diagonal.
40 psi - 4 springs - 2 per end cap.
Use two in opposite corners.
The values listed below are for standard and less than the
standard air pressure as required per the ordering code.
NOTE: Maximum Operating Pressure Does Not Change.
Ordering Code
4
5
6
7
( )
Supply Pressure (psi)
40
50
60
70
80
Actuator Size
End of Spring Torque (in-lb)
10
35
55
75
75
95
15
65
105
145
145
185
20
125
195
265
265
335
2. If a spring-return actuator is being repaired due to a failed spring,
REPLACE all the springs in this actuator, as well as any other
parts which may have been damaged.
3. When replacing the springs in a spring-return actuator, place the
springs in the end cap pocket after thoroughly lubricating each
spring. Be generous with lubricant!
4. With the springs pointing up and the end cap on a solid surface,
place the actuator body over the springs and the proper end cap.
(Each end cap can only be mounted to just one end of the
actuator body, as there is a “fool proof” pin in the end cap which
aligns with a hole in the body.)
5. Force the body down and begin by engaging two end cap screws
(5C) by hand through the end cap. Take each end cap screw up in
SMALL and EQUAL turns. Once the end cap is temporarily
secured to the body, turn the actuator over to its normal position
and uniformly take up the four end cap screws. Uniformly load all
the springs to prevent any spring from buckling.
6. In a similar manner, as in the previous steps, replace the springs
in the other end of the actuator body.
PARTS LISTING
ITEM
QTY.
DESCRIPTION
ITEM
QTY.
DESCRIPTION
1
1
Actuator Body
14
Varies
Springs - See Table on Page 12
2
1
Shaft (10-2039)
15A
2
End Cap O-rings
3
2
Pistons
15B
4
Guide Rod O-rings
4
2
Guide Rods
15C
2
Piston O-rings
5A
1
ACCESS End Cap
15D
1
Top Shaft O-ring
5B
1
End Cap
15
1
Bottom Shaft O-ring
5C
8
End Cap Screws (Metric)
15F
1
Shaft Clip
5D
1
Cover “Z”
15G
1
Top Pinion Bearing
5E
1
Caution Nameplate “Z”
15H
1
Bottom Pinion Bearing
5F
1
Cover “W”
16
1
Wiring Diagram - Not Shown
5G
1
O-ring - Cover
17
1
Position Indicator
6A
4
End Cap Bearing (Split-Ring Style)
18
2
Drive Screw
6B
2
Piston Bearing (Split-Ring Style)
19
2
Probes
7A
1
Control Block Assembly
20
2
O-rings - Probe
7B
-
Not Used
21
4
Washers - Probe
7C
-
Not Used
22
2
Retaining Clips - Probe
7D
4
Control Block Bolts
23
2
Spring - Probe
8A
1
Solenoid Assembly
24
1
Printed Circuit Board (Circuit Board Shown)
8B
2
Solenoid Exhaust Port Fittings
25
2
Printed Circuit Board Mounting Screws
8C
1
Solenoid Exhaust Tubing
26A
1
Limit Switch (Proximity Sensor) Assembly - Left
9A
1
Gasket - Control Block (Double-Acting) (Fig. 2)
26B
1
Limit Switch (Proximity Sensor) Assembly - Right
9B
1
Gasket - Control Block (Spring-Return) (Fig. 2)
27
4
Mounting Screws - Limit Switch (Proximity Sensor)
10
1
Thrust Bearing
28
2
Switch (Sensor) Adjustment Screw
11
1
Nameplate
29
2
Switch (Sensor) Adjustment Spring
12
2
Piston Set Screws (if any)
13
1
Conduit Plug - Not Shown
To order proper parts, please specify the actuator size, model, and revision number. Use the standard nomenclature listed above.
The rebuilding kits include Items 15A thru 15H, 6A and 6B, 10, and stainless steel washers. Color of some replacement parts, such as bearings, may vary from the parts removed.